5
1
9780444510471
Six Sigma Quality for Business and Manufacture available in Hardcover, eBook
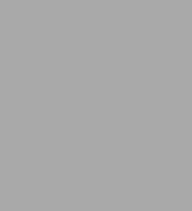
Six Sigma Quality for Business and Manufacture
by Joseph M J Gordon
Joseph M J Gordon
- ISBN-10:
- 0444510478
- ISBN-13:
- 9780444510471
- Pub. Date:
- 10/25/2002
- Publisher:
- Elsevier Science
- ISBN-10:
- 0444510478
- ISBN-13:
- 9780444510471
- Pub. Date:
- 10/25/2002
- Publisher:
- Elsevier Science
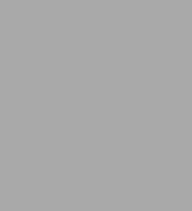
Six Sigma Quality for Business and Manufacture
by Joseph M J Gordon
Joseph M J Gordon
$340.0
Current price is , Original price is $340.0. You
Buy New
$340.00
$340.00
340.0
In Stock
Overview
Six Sigma is Business and Industry's newest recognized quality program. This text provides information and instructions for new and current quality professionals in order to help employ methods to attain Six Sigma defect quality assurance within their company.All areas of business and manufacture are covered. Detailed checklists, questionnaires and forms assist personnel in developing their own programs to 'prevent' problems from occurring and to solve new and long-term problems in services and manufacturing. Examples and formulae are provided for use to determine if, when and then how much a process may be adjusted for reaching higher quality assurance levels. Knowledgeable readers will be able to use this comprehensive text immediately in the workplace.
Product Details
ISBN-13: | 9780444510471 |
---|---|
Publisher: | Elsevier Science |
Publication date: | 10/25/2002 |
Pages: | 572 |
Product dimensions: | 6.00(w) x 9.00(h) x (d) |
Table of Contents
Preface | v | |
Acknowledgments | vii | |
Chapter 1. | How Companies Use Six Sigma to Improve Processes and Prevent Problems | 1 |
Programs That Can be Initiated | 2 | |
Quality Implementation Tools | 3 | |
Six Sigma Programs | 3 | |
Six Sigma Risk and Fault Abatement | 4 | |
Defect Reduction | 5 | |
Where Can Six Sigma Breakthrough Occur | 8 | |
Measure--Analyze--Improve--Control | 11 | |
Program Analysis | 13 | |
Check Lists for Six Sigma Analysis | 14 | |
Selecting the Six Sigma Program | 15 | |
Establish Quality Improvements | 19 | |
Quality Function Deployment | 21 | |
Six Sigma Program Implementation Guidelines | 22 | |
Training | 28 | |
Communication | 30 | |
References | 31 | |
Chapter 2. | Six Sigma Implementation Process | 33 |
Rate of Six Sigma Implementation | 40 | |
The Key is Managing for Six Sigma | 40 | |
Designing for Six Sigma | 42 | |
Processing for Six Sigma | 43 | |
Rates for the Employment of Six Sigma Methodologies | 44 | |
Establishing the Base Line for Six Sigma Improvement | 45 | |
Determine Your Baseline Quality Level for Six Sigma Analysis | 46 | |
Monthly Improvement Rate Significance for Change | 50 | |
Quality Function Deployment | 57 | |
Establishing QFD Operations | 58 | |
Steps in the QFD Implementation Process | 60 | |
QFD Analysis Conclusions | 66 | |
Selecting Six Sigma Black Belt and Team Candidates | 69 | |
Six Sigma Black Belt Selection | 70 | |
Black Belts Embed Six Sigma Methods into Company Culture | 77 | |
Selection of a Champion for Six Sigma Team Success | 79 | |
Personnel Requirements | 81 | |
Selecting Team Members | 82 | |
Define Six Sigma Team Roles | 83 | |
Quality Team Charter | 84 | |
Team Member Task Assignments | 90 | |
Company Departmental Organization and Responsibility | 91 | |
Six Sigma Data Collection | 93 | |
Establish Data Collection | 93 | |
Training Options | 95 | |
Technical Six Sigma Knowledge Required for Quality Improvement | 97 | |
Goal Setting | 97 | |
Planning and Implementation Processes | 98 | |
References | 98 | |
Chapter 3. | Reasons for Implementing Six Sigma | 99 |
Contributor to Quality Example | 99 | |
How Tight is Six Sigma Quality | 100 | |
Initial States of Implementation of Six Sigma for Business and Manufacturing | 101 | |
Anticipated Early Six Sigma Results | 107 | |
Six Sigma Team Skills | 107 | |
Problems Identified to Complexity | 112 | |
Analysis of Complex Problems or Process Improvements | 112 | |
How a Six Sigma Team Solved a Problem | 113 | |
References | 124 | |
Chapter 4. | Design Your Operations for Six Sigma Manufacture | 125 |
Six Sigma Design Matrix | 125 | |
Elimination of Seventy to Eighty Percent of Final Design Problems with Six Sigma | 126 | |
Design Steps for Six Sigma Production | 129 | |
Failure Mode and Effects Analysis (FMEA) | 133 | |
Use of Check Lists for a FMEA | 135 | |
Use of Trouble Shooting Guides for a FMEA | 136 | |
FMEA Team Development | 136 | |
Assumptions for the FMEA Process | 139 | |
Manufacturing Cell Equipment and Operations | 139 | |
Manufacturing Cell External Support Systems | 140 | |
Supplier and Customer--Past and Future Requirements | 140 | |
Maintenance One of the Keys to Six Sigma Quality Operation | 141 | |
Preventative Maintenance the Company Goal | 141 | |
Benefits to Company Production Schedule | 143 | |
Use of the Maintenance FMEA | 143 | |
Occurrence | 146 | |
Detection for Prevention of Problems | 148 | |
Predicative Methods | 149 | |
Cause and Effect Analysis | 149 | |
Example of Cause and Effect Analysis | 150 | |
Example of Poor Lot Control | 153 | |
Problem Analysis, Cause and Affect | 154 | |
Final Analysis of the Problem | 155 | |
Conclusion, the Prevention of a Problem | 156 | |
Documentation | 156 | |
Taking Action--What and How | 158 | |
What Action Should be Taken? | 158 | |
Corrective Action | 159 | |
How is Action Taken | 159 | |
Immediate Action | 160 | |
Problem Solving Matrix | 165 | |
Preventive Actions | 167 | |
References | 169 | |
Chapter 5. | Six Sigma Education and Using the Existing Quality Methods and Procedures | 171 |
The Need for a Company Champion | 173 | |
Categorize and Analyze Quality Problems | 174 | |
Problem Solving Categories | 176 | |
Conformance Problems | 176 | |
Product Deviation Problem | 179 | |
Engineering Change Request (ECR) | 180 | |
Unstructured Performance Problems | 184 | |
Efficiency Problems | 185 | |
Six Sigma Goal Setting | 186 | |
Product Design Problems | 188 | |
Process Design Problems | 189 | |
Tools for Implementing Six Sigma | 191 | |
Process Mapping for Six Sigma Team Actions | 192 | |
Profile Process Improvement | 193 | |
Six Sigma Program Requirement Overview | 196 | |
Six Sigma Team Training | 197 | |
The Tools for Six Sigma Problem Solving and Prevention | 199 | |
Statistical Process Control | 200 | |
Process Control Charting | 205 | |
Calibration | 208 | |
How to Determine the Variables to Monitor | 210 | |
Establishing Control Limits for the Process | 211 | |
Determining the Critical Product Dimensions | 212 | |
Process Control Charting | 214 | |
Control Charts | 215 | |
Measurement Process Control Chart Calculations | 217 | |
Control Chart Calculation Procedure | 222 | |
Control Limit Calculations | 222 | |
Data Collection | 227 | |
Who Should Collect the Data | 230 | |
Data Presentation for Monitoring Control | 232 | |
How Should Data be Used | 232 | |
Who Uses the Data and When | 234 | |
What to do When Out of Control Occurs | 235 | |
Who Makes the Changes and What Changes are Made | 235 | |
How Long to See the Effects of a Process Change | 235 | |
Consider a DOE (Design of Experiments) | 237 | |
Statistical Process Control for Complex Problems | 239 | |
Statistical Process Control Charts | 240 | |
Process Limits | 241 | |
Data Subgroups | 243 | |
Out of Control Situations | 244 | |
References | 245 | |
Chapter 6. | Achieving an Effective Six Sigma Deployment Plan | 247 |
Selecting the Program for Six Sigma | 247 | |
The Analysis of the Organization and Cost of Quality | 249 | |
Cost of Quality Prevention Areas | 249 | |
Cost of Quality for Six Sigma | 250 | |
Prevention Versus Correction | 253 | |
Appraisal Cost | 253 | |
Calculating Cost of Product Quality | 254 | |
Quality Return on Investment | 260 | |
Deploy Six Sigma by Functional Area, Product, Process and Department | 261 | |
Program Management Representatives | 263 | |
Pareto Charts | 263 | |
Standard of Flexible Implementation Design Across Varied Business Units | 266 | |
ISO9000 Improvements Based on Six Sigma Results | 266 | |
Balance the Rate of Deployment for Maximum Effectiveness | 267 | |
Kaizen | 268 | |
Six Sigma Programs | 270 | |
Six Sigma Opportunities for Problem Prevention | 271 | |
Reengineering Existing Infrastructure to Facilitate Six Sigma | 275 | |
How to Balance the Rate of Deployment for Optimum Effectiveness | 276 | |
Example of Change Correctly Implemented | 276 | |
References | 278 | |
Chapter 7. | Six Sigma Improvements in Business and Manufacturing | 279 |
Obtain Improvements in Business and Manufacturing, Bench Marking and Indicators | 279 | |
Software Systems for Six Sigma Quality | 280 | |
Six Sigma (Business) Order Entry Software Requirements | 281 | |
Manufacturing Data Entry | 282 | |
Bar Code Tracking | 282 | |
Benchmarking | 283 | |
Six Sigma Impact on in Place Quality Systems | 284 | |
Applying Six Sigma Tools for Continued Improvement | 285 | |
Product Capability | 286 | |
Fun and Enjoyment Implementing Six Sigma | 288 | |
Testing | 288 | |
Metric Example | 288 | |
An Example of Problem Solving | 289 | |
Process-Capability | 291 | |
Process-Capability Index | 295 | |
Types of Testing, Appraisal, Confirmation and Characterization | 296 | |
Confirmation Testing | 297 | |
Process Test Control (Destruction Test) | 298 | |
Characterization Testing | 299 | |
Confirmation | 299 | |
Variance Ratio | 300 | |
The Risk of Making a Bad Decision | 302 | |
Tracking Manufacturing Using Existing Process Indicators | 305 | |
Verification of Six Sigma Manufacturing Capability | 306 | |
What Really is Six Sigma and Improved Process Control | 307 | |
Six Sigma Methodology | 309 | |
Implementing the Six Sigma Process | 311 | |
Implementing the Six Sigma Improvement Program | 312 | |
Six Sigma Program Development | 317 | |
Six Sigma Pays Its Own Way | 318 | |
Procedures for Implementing Six Sigma | 320 | |
Step 1 | Assessment of the Company Organization | 320 |
Step 2 | Executive Action Planning Workshop | 324 |
Couple the Six Sigma Program to the Company Vision Statement | 325 | |
Step 3 | Gathering Information | 326 |
Step 4 | Just-In-Time Training | 328 |
Optimization the Key to Achieving Six Sigma Capability | 330 | |
References | 330 | |
Chapter 8. | Six Sigma Keys to Success are Control, Capability and Repeatability | 333 |
The Three Keys to Six Sigma Success | 334 | |
Maintaining Process Control | 334 | |
Measure, Analyze, Improve and Control the Process | 335 | |
Example of Base Line Capability | 336 | |
The Twelve Step Improvement Process | 338 | |
Validate the Measurement System for Process Control | 341 | |
Measurement of Process Performance | 343 | |
Six Sigma Process Capability | 344 | |
Non-Normal Distribution Curves | 344 | |
Instability Index | 345 | |
Obtaining Six Sigma process control in "Real Time" | 346 | |
Box-Jenkins and EWMA Charts | 347 | |
Process Adjustments | 349 | |
Defining Process Stability and Repeatability | 350 | |
Real Time Process Stability is Defined | 351 | |
How to Use the Box-Jenkins Bounded Manual Adjustment Chart | 351 | |
Real Time Process Stability | 352 | |
Use of the Box-Jenkins Manual Adjustment Chart | 355 | |
How and When to Adjust the Process | 357 | |
The Bounded Box-Jenkins Manual Adjustment Chart | 358 | |
Computing Standard Error for EWMA | 362 | |
When Should the Process be adjusted? | 364 | |
Potential When an Adjustment is Made | 365 | |
Implement Change with Six Sigma Methodologies | 366 | |
A Better Way to Generate Ideas for Change | 371 | |
Lean Manufacturing Principles | 372 | |
Implement Meetings of Substance | 378 | |
Eight (8)--D Problem Solving Methodology | 380 | |
Organizational Change Experience for Excellence | 386 | |
Tracking Six Sigma Continuous Improvement | 387 | |
Improved Work Flow, Pulled versus Pushed | 388 | |
Communication. Before and After Six Sigma Implementation | 389 | |
Deploying Six Sigma to Customers and Suppliers | 389 | |
References | 392 | |
Glossary | 393 | |
Appendix A. | Check Lists for Business and Manufacture | 427 |
Appendix B. | DOE (Design of Experiments) | 465 |
Appendix C. | Six Sigma Quality Control SPC Forms and Data | 481 |
Index | 553 |
From the B&N Reads Blog
Page 1 of