Facility Inspection Field Manual: A Complete Condition Assessment Guide / Edition 1 available in Paperback
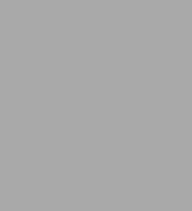
Facility Inspection Field Manual: A Complete Condition Assessment Guide / Edition 1
- ISBN-10:
- 0071358749
- ISBN-13:
- 9780071358743
- Pub. Date:
- 11/06/2000
- Publisher:
- McGraw-Hill Professional Publishing
- ISBN-10:
- 0071358749
- ISBN-13:
- 9780071358743
- Pub. Date:
- 11/06/2000
- Publisher:
- McGraw-Hill Professional Publishing
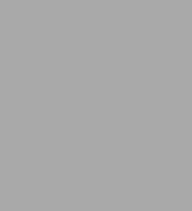
Facility Inspection Field Manual: A Complete Condition Assessment Guide / Edition 1
Paperback
Buy New
$54.95Buy Used
-
-
SHIP THIS ITEM
Temporarily Out of Stock Online
Please check back later for updated availability.
-
Overview
How do you efficiently manage facility infrastructure? You turn to this hands-on, answer-packed, time- and money-saving guide designed for every facility manager who has to do more with less. It shows you how to conduct seamless facility condition inspections that provide an overall snapshot of the current condition of your facility, generating enormous amounts of priceless information that will help you reduce or eliminate downtime and keep your facility humming.
This comprehensive, portable toolkit packs everything you need to:
* Continually assess the condition status of every aspect of a building: all of its systems and equipment, components and subcomponents
*Identify deficiencies before they become major problems
* Get better performance from every system
Product Details
ISBN-13: | 9780071358743 |
---|---|
Publisher: | McGraw-Hill Professional Publishing |
Publication date: | 11/06/2000 |
Series: | First-Choice Field Manuals |
Pages: | 428 |
Product dimensions: | 5.00(w) x 8.00(h) x 0.87(d) |
About the Author
Richard P. Payant has more than 7 years of experience as Director of Facilities Management at Georgetown University and more than 23 years' experience with the Army Corps of Engineers. A certified plant engineer and facility manager, an adjunct professor at George Mason University, and the author of several professional publications, he has an M.A. in business management/public administration from Central Michigan University and a B.S. from Norwich University.
Read an Excerpt
Chapter 1: The Need For A Condition Assessment Program
IntroductionFacility managers today are plagued with requirements to save money. As such, benchmarking, downsizing, improving productivity and efficiency, streamlining supply, purchasing, and partnering are just a few of the initiatives ongoing in many facility departments today. "Doing more with less" is now a reality.
Traditionally, part of the annual facility funding request was based on reducing backlog in order to improve conditions within specific facilities. From a facility manager's perspective, this was the best way to obtain funding; however, on the financial management side, it often fell on deaf ears. Facility managers, therefore, have had to become better versed in financial concepts in order to justify the financial benefit of the funding they sought. Today, they have to think in terms of what contributes to the organization's bottom line. The more active role they can take in financial and budgeting matters, the more effectively their responsibilities can be accomplished.
Life of a Facility
Facilities are similar to the human body. They have a useful life, they age, live and breathe, and eventually they have final disposition. For example, the mechanical and electrical systems in a building are similar to the heart and lungs of the body; the energy management control systems are similar to the human brain; and the various environmental and life safety alarm systems are similar to the body's nervous system; the exterior envelope of the building corresponds to the body's skin.
As human beings take care of their bodies, they perform better; buildings are the same. If building systems are properly maintained and kept in good state of repair, their useful life is extended, they are actually cheaper to maintain, and less possibility exists for building sickness.
Life expectancy of a facility today is different than it, was 20, 30 or even 50 years ago. Much of the difference is due to changes in types of materials used. A hundred years ago, slate was a common material used for roofs. A slate roof, although expensive to install, has a 100-year life expectancy. Today, however, other types of roof systems and materials are used, and these changes have changed the life expectancy of roofs. Mechanical systems were commercially introduced primarily after World War II (over 50 years ago). These systems have been redesigned and upgraded to the point, today, where in some cases it may be cheaper to dispose of the system than to try to repair or rebuild it.
Consequently, in this country we are seeing an aging infrastructure. "Deferred maintenance," in the last 10 years, has become a well-known concept, entailing enormous amounts of money to be expended. Good preventive and predictive maintenance programs and a method of inspecting facilities are important steps to slow down deferred maintenance growth.
As stated earlier, facilities are aging and are continuously being renovated, often in piecemeal fashion. These renovations can be for modernization and upgrade reasons or for change of mission. Many renovations are limited in scope due to funding restraints and many times result in cosmetic change with few or no infrastructure improvements. This fragmentation can lead to inefficiency of mechanical systems, customer complaints due to dissatisfaction with their facility or space environmental conditions, and eventually higher utility bills and maintenance costs. Consequently, recommissioning of the entire facility on a periodic basis (every few years) may be needed. This can be done by hiring a commissioning agent, but that will be expensive. As an alternative, it may be possible to free up an in-house mechanical engineer, who, using checklists in this book, could conduct periodic inspections of entire facility systems. This information can then be used to feed into either the organization's capital plan or the deferred maintenance list.
Knowledge Is Power
The knowledge and information possessed by the facility manager have the power to transform a reactive maintenance program into a proactive one. A proactive maintenance organization is one that optimizes future benefits, i.e., maximizes return on investment. Funding, therefore, has become the standard of performance-in other words, what value the organization is getting for its maintenance dollar. Because maintenance protects the capital investment of equipment, systems, and physical plant, it should be considered an investment in the future.
Inventory
To maximize return on investment of physical plant assets, the facility manager must have good information on the distinctive elements and status of the assets managed. A detailed inventory of the physical plant's equipment, and the components that make up that equipment, is imperative and forms the basis for preventive maintenance, predictive maintenance, space utilization, and capital asset replacement analysis.
Equipment, Systems, and Structures Inspections
Few facilities management activities have as much potential to influence facilities improvements and funding as formal scheduled inspections. Total building, equipment, and system inspections are an essential part of and overall facilities management plan...