Total Quality Management: A Cross Functional Perspective / Edition 1 available in Paperback
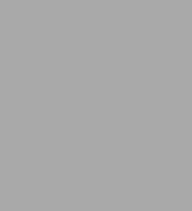
Total Quality Management: A Cross Functional Perspective / Edition 1
- ISBN-10:
- 0471108049
- ISBN-13:
- 9780471108047
- Pub. Date:
- 04/19/1996
- Publisher:
- Wiley
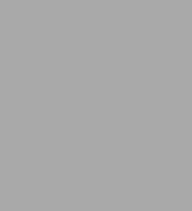
Total Quality Management: A Cross Functional Perspective / Edition 1
Paperback
Buy New
$266.75Buy Used
$174.43-
-
SHIP THIS ITEM
Temporarily Out of Stock Online
Please check back later for updated availability.
-
Overview
Product Details
ISBN-13: | 9780471108047 |
---|---|
Publisher: | Wiley |
Publication date: | 04/19/1996 |
Pages: | 656 |
Product dimensions: | 7.72(w) x 9.41(h) x 1.17(d) |
About the Author
Lawrence P. Carr
Ismael Dambolena
Robert J. Kopp
John Martin
Farshad Rafii
Phyllis Fineman Schlesinger
Table of Contents
1. Quality as a Strategy 1The Global Battleground 2
The PIMS Study 4
The History of Quality in the United States 6
A New Theory of Quality 9
The MIT Commission Findings 12
The New Management Approach 14
TQM and the Corporate Strategy 16
Does TQM Work? 17
Overview of the Book 20
Key Terms 21
Assignments 21
Case Study: Provisions, Inc.—The Cooked Meat Division 22
Bibliography 23
2. What is TQM? 25
Introduction 25
The First Approach: Defining Quality? 26
The Transcendent Approach 26
The Product-based Aproach 26
The User-based Approach 27
The Manufacturing-Based Approach 27
Value-based Approach 28
The Second Approach: TQM Practices 31
ISO Standards 31
The Malcolm Baldrige National Quality Award 34
The International Quality Study 34
The Third Approach: The Philophies of Leading Sages 37
Deming 37
Juran 40
Crosby 43
Feigenbaum 45
Ishikawa 48
Tagachi 49
Summarizing the Philosophies 51
The Fourth Approach: Evolution of Quality Thinking in Japan 52
Summary 58
Key Terms 39
Assignments 59
Bibliography 61
3. The Baldrige Award 63
Introduction 64
Overview of History, Purpose, and Operations 64
Legislation 64
Aware Purpose 65
Roles and Responsibility 65
Applications for the Award 66
The Award Criteria 66
Positioning the Award Criteria 68
The Evaluation System for Applicants 71
Values and Concepts 71
Criteria Framework 73
Scoring Guidelines 74
Business Factors 75
The Board of Examiners 76
Appointment and Training 76
Establishing Standards and Consistency 77
Code of Conduct 77
Applicant Evaluation and Feedback 79
Review 79
Consensus Review 79
Site Review 80
Judges’ Recommendations 80
The Feedback Report 80
The Award Criteria in Practice 81
Developing the Core Values 81
Customer-Driven Quality 83
Leadership 84
Continuous Improvement and Learning 84
Employee Participation and Development 84
Fast Response 85
Design Quality and Prevention 85
Long-Range View of the Future 86
Management by Fact 86
Partnership Development 87
Corporate Responsibility and Citizenship 87
Results Orientation 88
Impact of the Baldridge Award 88
U.S, Industry and Government 88
The Characteristics of Successful Applicants 90
The Stale Awards 90
Overseas Leadership 92
The Baldrige Aware and ISO 9000 Standards 93
Use in Education 94
Future of the Award and Continuous Improvement 94
Summary 95
Key Terms 96
Assignments 96
Case Study 101
Case Study: Colony Fasteners, Inc. 113
Bibliography 117
4. Measures of Quality Product and Quality Process: The Traditional Approach 119
Introduction 119
The Evolution of the Cost of Quality 122
The Traditional Cost-of-Quality Model 122
Conformance Costs 123
Nonconformance 123
Limitations to the Cost of Quality 129
Summary 133
Key Terms 133
Assignments 133
Case Study: Matthews-Thornton Manufacturing Co. 134
Bibliography 137
5. Measures of Quality Product and Quality Process: The Emerging Cost-of-Quality Model 139
Introduction 139
Other Methods to Measure the Cost of Quality 140
Sustaining Cost of Quality: The Xerox Story 144
Lessons from Xerox 151
Accounting Support of TQM 151
Other Measures of TQM 152
Information Systems Support 155
Implementation 155
Summary 156
Key Terms 157
Assignments 157
Cost of Quality Assignment 158
Case Study: Materials and Control Corporation 160
Bibliography 163
6. Continuous Improvement: Basic Tools 165
Overview of Continuous Improvement 165
Relationship of Chapters 6, 7, and 8 to Continual Improvement 167
Data Types and Summaries 168
Types of Data 168
Populations and Samples 169
Data Summarization 169
Tabular and Graphic Summarization of Numeric Data 170
Tabular Summaries for Numeric Data: Frequency Distributions 170
Graphic Summaries for Numeric Data: Histograms and Stem-and-Leaf Displays 172
Other Graphic Tools 179
Graphs for Categorical Data: Bar Charts, Pie Charts, and Pareto Diagrams 179
Graphs for Time-Ordered Data: Run Charts 185
Flow Diagrams 185
Cause-and-Effect Diagrams 188
Cautionary Note on Graphs 190
Facilitating Data Collection: Check Sheets 190
Numeric Data Summarization 192
Measures of Location: The Mean and the Median 192
Measures of Spread: The Standard Deviation, Variance, Range, and Percentiles 194
A Graphic Display of Numeric Summaries: The Box Plot 196
Graphing the Relationship Between Two Variables: The Scatter Diagram 196
The Seven-Step Method for Continuous Improvement 199
The Seven Steps 200
Relation to the PDCA Cycle 201
Summary 203
Key Terms 203
Assignments 204
Case Study: Accelerating Improvement 207
Case Study: Motorola-Codex 221
Bibliography 230
7. Continuous Improvement: Statistical Process Control 231
Introduction 231
The Seven Basic Tools 232
Control Charts 232
Sources of Variation 232
Introduction to Control Charts 232
Attributes and Variables 235
Control Charts for Attributes 236
p Charts and np Charts 236
c Charts and u Charts 238
Control Charts for Variables 241
X-bar Charts and R Charts 243
Control Charts for Individuals 243
Out-of-Control Patterns 244
The Development of Control Charts 248
The Development of p Charts 248
np Charts 252
c Charts 252
u Charts 252
X-bar Charts 253
R Charts 253
Control Chart for Individual Measurement 254
Moving Range Control Chart 254
Statistics, Probability, and Random Variables 254
Inferential Statistics 254
Random Sampling 256
Enumerative and Analytical Studies 256
Probability 257
Random Variables and Probability Distributions 258
The Expectation of a Random Variable 259
The Variance and Standard Deviation of a Random Variable 262
Discrete Versus Continuous Random Variables 262
The Normal Distribution 264
The Standard Normal Distribution and Normal Probability Tables 265
Finding Probabilities for Normal Distribution: The General Case 270
Problems Where Areas Are Given 273
The Behavior of Samples 275
The Behavior of Sample Means: The Central Limit Theorem 276
The Behavior of Sample Ranges 281
The Behavior of Sample Proportions 281
Statistical Basis for the Development of Control Charts 286
p Charts 286
np Charts 288
c Charts and u Charts 289
X-bar Charts 289
R Charts 293
Control Chart for Individual Measurements 294
Moving Range Control Chart 295
References 295
Summary 295
Key Terms 296
Assignments 296
Case Study: Understanding the Trade Deficits 305
Bibliography 307
8. Continuous Improvement: Some Advanced Tools 309
Introduction 309
Enhancing the Seven-Step Method 310
Developing an Affinity Diagram 311
Electronic Brainstorming 318
Process Capability and Six-Sigma Quality 319
The Cp Index 320
The Cpk Index 321
Six Sigma Quality 323
Taguchi’s Loss Function 325
The Goal Post View of Quality 325
The Loss Function 326
Design of Experiments 331
Case Discussion: Product Improvement by Application of Taguchi Methods 333
The Factor Listing 334
The Orthogonal Array and Experimental Results 334
An Analogy 335
Randomization and Fractional Factorial Experiments 336
The Signal-to-Noise Ratio 336
Analysis of Results 337
Conclusions 338
Summary 339
Key Terms 340
Assignments 340
Case Study: Product Improvement by Application of Taguchi Methods 341
Appendix 8.1: Steps for Building an Affinity Diagram 353
Appendix 8.2: How Signal-to-Noise Ratios Work 356
Bibliography 358
9. Customer Measurement I: Traditional Multi-Attribute Methods 359
Introduction 360
Multi-Attribute Model 361
Identifying Important Attributes 362
Plot Existing Objects in Attribute Space: Employ Data Reduction
Techniques to Improve Data Interpretation 363
Measure Consumer Perceptions Via Rating Scales 366
Determine the importance Weights of Attributes 368
Base New Product Design on Filling Gaps in the Perceptual Space 368
Market Segmentation 369
Case Studies 369
Johnson Wax Enhance Conditioner 369
Suzuki Samurai 371
Telecom Inc. 371
Conjoint Analysis 374
Implications and Discussion 380
Summary 381
Key Terms 382
Assignment 382
Case Study:ABC Snacks 384
Bibliography 389
10. Customer Measurement II: Quality Function Deployment 391
Introduction 392
QFD and the House of Quality 393
An Overview of QFD 394
Building the House of Quality; An Example 397
Customer Inputs/Voice of Customer 397
Technical Inputs 397
Key Output: EC Weights and Target Values 398
Implications 398
Research Methodology Issues 398
Developing a List of CAs 399
Grouping and Labeling CAs 399
Measuring Attribute Importance 399
Qualitative Research Emphasis 400
The Kano Questionnaire 400
Implementing QFD—The Manager’s View 402
Organizational Behavior Implications 403
Case Studies 404
Puritan-Bennett Spirometers 404
Bharat Earth Movers Ltd. 405
Closing Thoughts 405
Summary 409
Key Terms 410
Assignments 410
Voice of the Customer Assignment 411
Constructing the House of Quality Assignment 413
Case Study; Quality Function Deployment at Knight Inc. 415
Bibliography 422
11 Initiating TQM: Managing Change 425
Introduction 425
Theories of Organizational Change 425
Types of Change 427
Understanding The Model for Change; Creating Dissatisfaction with the Status Quo 428
Understanding the Model for Change: The New Model of Managing 430
Understanding the Change Model: Implementation 432
Understanding the Change Model: Cost of the Change 434
Theory to Practice: Implementing TQM 435
TQM and Organizational Structure 445
Implementing TQM Programs 447
Implementing TQM 449
Summary 452
Key Terms 452
Assignments 452
Case Study: Ilank Snow and East Coast Electric: Instituting TQM 454
Bibliography 459
12. Employee Practices in Total Quality Management Organizations 461
Introduction 461
Employee Involvement and TQM: Similarities and Differences 462
Employee Involvement; Technique Adoption 464
Employee Involvement: Program Elements 466
Employee Involvement and Total Quality Management 466
HR Policies and TQM 469
A Model for Organizational Design 470
Organizational Structures 470
Management Processes 473
Selection Techniques 473
Development and Training 474
Rewards and Incentives 474
Performance Management 474
Pay Systems and Rewards 475
Summary: HR Systems 476
People Policies and TQM; Teams and Teamwork 476
Teams in TQM 477
Building Teams 478
Leadership .Roles in Teams 482
Self-Managing Work Teams 483
Unions and Total Quality Management 484
Empowering Organizational Members 486
Summary 488
KeyTerms 488
Assignments 489
Developing Performance and Task Deployment Assignment 489
Case Study: Upper Valley Health Clinic 494
Bibliography 499
13 TQM and the Product Development Process 501
Introduction 501
Structuring the Development Process 502
Structuring the Work 502
Aggregate Project Plan 505
Organizing the Resources 505
Defining the Product 507
The “Fuzzy Front End” 508
Consequences of Poor Definition and Management 508
Product. Definition 508
Identifying Customer Requirements 509
Setting Target Specifications 509
Creating Concepts 510
Selecting and Refining a Concept 511
Designing and Developing the Product 511
Architecture and Modularity 512
Advantages of Modularity 512
Conscious Architecture 512
Design for Manufacturability 513
Design for Assembly 513
Design to Cost 515
Design for Usability 515
Prototype-Test-and-Refine 516
Concurrent Engineering 517
Design Iterations 518
Design Structure Matrix 518
Implementing Concurrent Engineering 519
Summary 519
Key Terms 520
Assignments 520
Case Study: Plus Development Corp (A)—Abridged 522
Bibliography 529
14. Reengineering and TQM: The Role of Information Technology 531
IT and Process Improvement 532
Differences Between TQM and Reengineering 532
The Impact of IT on the Bottom Line 533
Making an Impact with IT 534
A Reengineering .Methodology 535
Stage 1–Business Goals and Constraints 535
Stage 2–Selecting a Process for Improvement 538
Stage 3–Creating the New IT-Based Process 540
Stage 4–Developing the Systems are the Organization Structures 541
Stage 5–Effecting the Culture Change and implementing tire System 544
Post-Reengineering 546
Quality Information Systems 547
Communication of QI Team Activities 547
Process-Related Information for QI Teams 548
Operational Information to Support Corporate Goals 550
Summary 556
Key Terms 557
Assignments 557
Case Study: Morewood Enterprises 558
Bibliography 559
15. Benchmarking 561
Introduction 561
Traditional Approaches to Gathering Information 563
The Evolution of Benchmarking 564
Competitive Benchmarking 566
Benchmarking Product Characteristics 566
Benchmarking Product. Costs 567
Examples of Cost Benchmarking 568
Process Benchmarking 570
An Example of Process Benchmarking 572
Process Flow Mapping 573
Strategic Benchmarking 577
An Example—Benchmarking Diversity 578
Key Issues in Benchmarking 581
What Should Be Benchmarked? 581
Who Should Be on the Team? 581
Who Should Be Selected as Benchmarking Partners? 582
What Legal Issues Are Involved? 583
What Arc Some Common Pitfalls? 584
The Partner’s Perspective 584
Handling Benchmarking Requests 585
Benefits of Being a Host 586
Criteria for Screening Requests 586
Maximizing the Benefit from an Information Exchange 587
Summary 588
Key Terms 588
Assignments 589
Case Study. Simon Alphin: The Benchmarking Study 591
Case Study: Shawmut Industrials—Marta’s Visit 592
Bibliography 593
16. Landmarks on the TQM Road 595
Others That Failed 596
Some Who Are Succeeding 597
The Wallace Company 599
Florida Power & Light 601
The Xerox Story 602
Building Union Support for TQM 604
Building Management Support for TQM 606
Xerox after Winning the Baldrige 609
Landmarks on the TQM Road. 611
The First Landmark:. Awareness 611
The Second Landmark: Understanding 613
Thu Third Landmark; Maturity 615
Summary 618
Assignments 618
Bibliography 619
Author Index 620
Subject Index 622