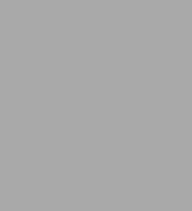
The Sewing Answer Book: Solutions to Every Problem You'll Ever Face; Answers to Every Question You'll Ever Ask
432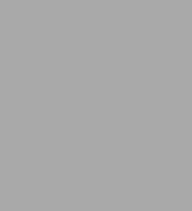
The Sewing Answer Book: Solutions to Every Problem You'll Ever Face; Answers to Every Question You'll Ever Ask
432eBook
Available on Compatible NOOK devices, the free NOOK App and in My Digital Library.
Related collections and offers
Overview
This informative and encouraging guide offers proven solutions to all of your most stubborn sewing problems. With a question-and-answer format that makes it easy to find what you need, Barbara Weiland Talbert includes tips on selecting the perfect patterns, choosing the right size needles, comparing seam types, and much more. No matter your sewing experience or whether you prefer to use a machine or sew by hand, The Sewing Answer Book will help you hone your skills while inspiring you to try new and exciting techniques.
Product Details
ISBN-13: | 9781603423786 |
---|---|
Publisher: | Storey Publishing, LLC |
Publication date: | 07/23/2010 |
Sold by: | Hachette Digital, Inc. |
Format: | eBook |
Pages: | 432 |
File size: | 9 MB |
About the Author
Barbara Weiland Talbert is a noted quilting and sewing author, columnist, editor, and designer whose writing has been featured in publications including Sew News and Sewing Savvy. She has extensive experience teaching sewing seminars and solving the problems of stitchers of all levels. Visit her at www.joyofsewing.com
Read an Excerpt
CHAPTER 1
Setting Up Your Sewing Room
The quality of the tools and equipment you use affects the final results. The top three essentials are: a sewing machine with an array of basic presser feet, a good iron, and an adjustable ironing board. Many sewers would also recommend a serger as essential. Good lighting and a comfortable cutting surface are also necessary. After these major expenses are covered, adding special tools for special functions as your budget allows will make your sewing experience more fun and enjoyable.
Sewing-Machine Primer
For starters, you need a sewing machine in good working order. If in doubt about what to buy, check with a respected sewing teacher or expert at your local fabric store for his or her recommendations.
Q: I learned on my grandmother's machine, and I'm ready to buy my own. What should I look for in a sewing machine?
A: Today's machines are not like your grandma's or even your mother's first machine. Built-in decorative and utilitarian stitches, an array of automatic buttonholes, automatic needle threaders and thread cutters, sensors that let you know when the bobbin thread is running low — these are just a few of the innovations that sewers now enjoy. Computers make it possible to program your own stitch patterns and save your favorite stitch settings on some machines. The list of features is endless, so it's essential to shop carefully for your machine. Ask for hands-on demos, and test-drive the machines you are considering. Buy one with the features that you most need. Then learn how your new machine works; most dealers offer training classes with sewing-machine purchases to jump-start your experience.
A basic machine with a balanced straight stitch and a basic zigzag stitch is essential. Built-in utility stitches are also helpful.
A sewing machine is a major purchase. You may not replace it for many years — or you may decide to upgrade to a pricier model with more "bells and whistles" later. Before you shop, check out sewing publications and Consumer Reports. Ask other sewers about their machine experiences and opinions. If you've never sewn, read about how the sewing machine works and what the basic parts are before you go shopping so you can ask the right questions. (See pages 76–78.)
HERE ARE A FEW THINGS TO CONSIDER:
* Know your budget. Don't be persuaded to buy a machine with features you don't need. Hold your ground on this one.
* Know what types of sewing you plan to do, so the dealer can help you choose the best machine for your purposes. If you plan to quilt more than sew, you may want a machine with features that quilters love and use a lot.
* Look at different models and brands within your price range and test-drive them all. Keep notes.
* Take along fabrics for test stitching: a firmly woven one(such as denim) and a lightweight one (like muslin), plus a T-shirt knit and something slippery. Test straight and zigzag stitches, plus the buttonholes. Examine the stitch quality on each one. Do you like what you see?
* Buy from a local dealer where help is just a phone call or quick trip away. If you're not comfortable with a dealer during the sales pitch, don't buy from him or her. You want a comfortable, long-term relationship where you can get help, lessons, and repairs from someone you trust.
Q: Which presser feet do I need for my sewing machine?
A: Most machines come with a basic set of presser feet, those most used for basic sewing. These include the straight-stitch, zipper, all-purpose zigzag, and the blind-hem feet. Many include a clear or open-toe embroidery/appliqué foot, a special buttonhole foot, and another for sewing buttons on by machine (see page 388).
Each presser foot is designed for a specific purpose; the bottoms differ on many of them. The flat sole of the all-purpose foot rides smoothly over straight and utility zigzag stitches without thread buildup. It's the most-used foot on zigzag machines because it's wide enough to hold fabric securely against the feed dogs.
A straight-stitch foot has a small needle hole and a smooth sole. It's best used with a straight-stitch needle plate and is appropriate only for straight stitching. For decorative zigzag stitches, use the special zigzag foot, which has a small channel on the bottom.
For satin stitching and other heavy embroidery stitch patterns, use the open-toe embroidery/appliqué foot (see next question). Its wide channel glides smoothly over embroidery-stitch buildup without snagging or flattening the stitches. A flat-bottomed foot will hang up on them, causing stitch problems. This foot enables you to see edges when satin-stitching over appliqué edges and doing other decorative machine stitching. The buttonhole foot has two parallel channels to accommodate the stitched "legs" of the buttonhole. A blind-hem foot has a special built-in guide that runs along the hem fold for accurate stitching (see pages 312–313).
Q: Will I need any other presser feet for special techniques?
A: You can do most sewing with the basic presser feet. Specialty feet make easier work of many sewing techniques. Consider adding the following to your collection as your funds and projects warrant. Your dealer can show you how each foot works for the purpose intended — and often additional "Why didn't I think of that?" uses. Ask about other specialty presser feet and how to use them.
A ¼" patchwork foot (even if you don't plan to make quilts) helps you stitch an accurate ¼" seam allowance for home-decor projects as well as for some garment-sewing techniques. It's my most-used presser foot.
A walking foot is essential for preventing fabric layers from shifting when stitching thick fabrics and multiple layers. It grips and feeds the top layer of fabric while stitching, just as the feed dogs do the bottom layer. The foot is designed to prevent the machine from pushing the top fabric layer forward, eliminating stretched and puckered seams and uneven layers at the end of a seam. A walking foot is especially useful on denim and corduroy, as well as heavy home-decor fabrics such as upholstery tapestries. It's also essential for machine-quilting through layers of fabric and batting. Some machines have a built-in even-feed mechanism, making a walking foot unnecessary.
Note that the length and shape of the shank on presser feet varies from machine to machine — long, short, and slant-needle are the most common — so you must know the machine brand and model number before purchasing. Bernina feet have a unique clamp-on configuration and many machines now have a universal shank with snap-on presser feet.
Q: Why and when would I use a straight-stitch foot and needle plate?
A: Choose them for beautiful straight stitching without puckering on lightweight fabrics. The needle plate has a small, round hole; using it with the narrower straight-stitch foot usually improves the stitch quality and tension. It also helps prevent skipped stitches, because there is no extra room for the needle to push the fabric layers into the hole (called "flagging") like there is in a zigzag plate. It is often used with a spring-loaded embroidery foot for decorative free-motion stitching and quilting; because you move the fabric in many different directions when free-motion stitching, stitch tension can be problematic.
Q: Are there general care guidelines for all sewing machines?
A: Just like an automobile, your machine needs servicing to keep it in top running order and to eliminate frequent trips to the dealership. The more you sew, the more often your machine will require servicing. For general maintenance:
* Protect your machine(s) with a cover to prevent dust, dirt, pet hairs, and other contaminants from accumulating inside. Buy a cover, make one, or slip a pillowcase over the machine.
* Change needles after eight hours of sewing to avoid skipped stitches, broken thread, and damage to the fabric or your machine.
* Plug your machine into a high-quality surge protector to safeguard against lightning, poor wiring, and power surges. Turn off the machine and turn off the breaker on the surge protector when your machine is not in use.
* Clean and oil the machine after finishing a project or after every 8 to 10 hours of sewing (see Cleaning and Oiling Tips).
Q: Is it okay to use magnetic pin dishes near my computerized sewing machine?
A: Check your manual or ask your machine dealer. Some machines may be affected, while others are not.
Q: I bought my machine secondhand and have no manual. What do I do?
A: Visit your local dealer for help. You may be able to locate manuals online in downloadable PDF files. See Resources for website addresses.
Q: Can I use generic parts and attachments on my machine?
A: It's best to use replacement parts made specifically for your machine model. Generic parts may invalidate your warranty. Generic presser feet for special sewing applications (sewing on bead strings, for example) are fun to add to your sewing-machine toolbox. Purchase the one that has a shank like the one on your machine.
What About a Serger?
You can sew just about anything without a serger, but many sewers would find it difficult to part with theirs. Sergers can do many basic sewing functions and are wonderful for sewing knits, but if you must choose between machines, invest in a sewing machine first. Once you've stitched a seam with a serger, there's no room for fitting errors. The cutting blade that operates during stitching cuts away excess seam allowance.
Q: How is a serger different from a sewing machine?
A: A serger is most commonly used for seams in knits and for seam finishing, as well as for finishing a hem with a neat rolled edge on garments and home-decor items. At its most basic, a serger will make a seam while trimming and overcasting the edge — all in one step. This speeds up the sewing and finishing process. A serger cannot backstitch, make buttonholes, embroider, or do traditional topstitching and zipper applications. Like traditional sewing machines, sergers also have special presser feet for special techniques. See Resources for books that cover special serger techniques.
The most basic serger has one or two needles and two loopers, each one requiring its own thread. As the serger runs, a sharp blade moves up and down, making a neatly cut edge on the fabric layer(s), while the upper and lower loopers "knit" their threads over the freshly cut edge. The looper threads are caught into a line of stitches made by the needle thread. The entire process creates a truly ravel-free seam finish. Today, there are sergers with as many as ten threads for special techniques.
Q: Three or more threads? Doesn't that create a threading and tension nightmare?
A: Threading a serger can be intimidating at first, but once you learn how and start using your serger for seam and edge finishing, you'll wonder how you managed without it. After some hands-on threading experience at the dealer, take it home and thread, unthread, and rethread several times until the process is second nature. Keep your manual handy for threading and tension adjustments to create the traditional overlock stitch, as well as the rolled-edge and other seam and edge finishes. Take a beginning class at your dealership. Watch for classes at your local fabric store or community college.
Cutting Tools
Buy the very best cutting tools you can afford; they will last a lifetime if you take good care of them. To ensure clean cuts for accurate sewing, every sewer needs a dressmaker's shears, a few pairs of sewing scissors for different cutting tasks, and rotary-cutting equipment.
Q: What kind of scissors should I buy? Do I really need a rotary cutter?
A: Dressmaker's shears are essential for cutting out the pieces for any project. These 8" to 10" shears have two long, sharp blades with looped handles to fit your fingers and thumb. The long blades make it easy to make long, smooth cuts. The bent handle allows the bottom blade to glide smoothly along the cutting surface below the fabric; otherwise, you must lift the fabric and pattern from the cutting surface, resulting in inaccurate cuts with choppy edges. Bent-handled shears are also available with microser-rated blades for cutting thin, slippery, and slick-surfaced fabrics. If the shears you are considering don't slice easily through four layers of medium-weight fabric, look for a different pair.
Sewing or embroidery scissors are needed for cutting threads and trimming fabric edges. For all-purpose cutting, invest in 5"- or 6"-long sewing scissors (also called trimmers or tailor's scissors) with a pointed blade and a blunt blade. Embroidery scissors have two fine, sharp points for clipping threads and for cutting single layers or delicate fabrics. They are smaller, usually 3 ½" to 5" long.
A rotary cutter, mat, and ruler make cutting bias strips and rectangular shapes, such as pockets and waistbands, a breeze. You may also use them for other cutting tasks.
A seam ripper is essential for "unstitching" mistakes.
Q: Do I need pinking shears?
A: These special bent-handle shears (also called "pinkers") make zigzag cuts for finishing seam and hem edges, making those edges less prone to raveling. You can also use pinkers to trim and clip enclosed seams (see pages 282–286), or for making a decorative edge on firmly woven, nonwoven, or knit fabrics. Similar blades are also available for rotary cutters, along with blades for cutting other fancy decorative edges. To check for quality, make a test cut from the second tooth out to the tip along the edge on scraps of a lightweight and a heavyweight fabric. If the cutting is difficult or uneven, consider a different brand. Look for a deep, rather than shallow, sawtooth cut for the most ravel-resistant finish. This is a major purchase that can wait if you have budget restrictions.
Q: Are there any guidelines for caring for my sewing scissors and shears?
A: Keep your cutting tools out of the hands of nonsewers. Find a secure hiding place or mark them in a way that means "for sewing only." For example, tie a pink ribbon to the handle of each pair to indicate "hands off." Other care guidelines include:
* Use your cutting tools for fabric only. Keep a pair of general purpose craft scissors handy for cutting paper, cardboard, or plastic for templates.
* Wipe blades clean after use to remove lint and thread buildup; lint from tough man-made fibers like polyester and nylon is abrasive and can dull scissor blades. Store scissors and shears in a dry location to prevent rust.
* Sharpen periodically. Ask your local fabric store for recommendations.
* Don't drop your cutting tools. I tie a long ribbon to my sewing scissors and pin one end to the ironing-board cover. I have a second pair tied to my machine, so they're always handy.
* Place a tiny drop of sewing-machine oil on the pivot screw every few months, then open and close the blades. Wipe with a soft cloth to remove excess oil and cut through cotton fabric scraps to absorb any oil you may have missed.
* To avoid damaging the blades, never cut over pins or needles.
Q: Can I use a rotary cutter in place of dressmaker's shears for cutting?
A: Yes, if you feel comfortable using this sharp, pizza-cutter-like tool (see pages 164–165). Rotary cutting results in smooth and straight edges for cutting and sewing accuracy. The 45 mm-diameter cutter is the most popular, but smaller and larger sizes are available. You will need a large rotary cutting mat to protect your cutting surface and a 6" × 24" clear acrylic rotary ruler to guide cutting along straight pattern edges.
For cutting along curved edges, choose a small rotary cutter (18 mm). You'll need a very steady hand to cut without a guide, or try using a French curve ruler as a cutting guide. It may be easier to cut curved areas with shears.
Rotary cutting equipment is great for cutting home-decor project pieces, since they are usually large geometric shapes, but this works only if you have a large cutting mat and table. Moving fabric layers can cause slippage and distortion.
Q: How should I care for my rotary cutter for optimum use and accurate cuts?
A: Using a dull blade can irreparably damage your cutting mat. Also, using too much pressure to force a cut results in inaccuracy. At the first sign of poor cutting action (cuts require more pressure than usual or the blade skips and misses periodically), don't assume the blade is worn. Before you throw it out, try cleaning it:
1. Disassemble the cutting mechanism, placing the pieces on your work surface in the order removed.
2. Use a clean, soft cloth to wipe away any bits of lint on the blade or caught between the nut and blade.
3. Add a tiny drop of sewing-machine oil to the blade in the area that lies under the front sheath.
4. Tighten (but do not overtighten) the nut after reassembly. A too tight blade will hang up on the fabric layers and cause you to think it's dull or incorrectly assembled.
(Continues…)
Excerpted from "The Sewing Answer Book"
by .
Copyright © 2010 Barbara Weiland Talbert.
Excerpted by permission of Storey Publishing.
All rights reserved. No part of this excerpt may be reproduced or reprinted without permission in writing from the publisher.
Excerpts are provided by Dial-A-Book Inc. solely for the personal use of visitors to this web site.
Table of Contents
Acknowledgments,
Introduction,
Chapter 1: Setting Up Your Sewing Room,
Chapter 2: Needles and Thread,
Chapter 3: Stitching Basics,
Chapter 4: Working with Patterns,
Chapter 5: All About Fabrics,
Chapter 6: Interfacings and Linings,
Chapter 7: Seams and Seam Finishes,
Chapter 8: Hems and Hem-Edge Finishes,
Chapter 9: Shaping to Fit,
Chapter 10: Waistlines, Pockets, and Sleeves,
Chapter 11: Fasteners and Closures,
Resources,
Index,
Share Your Experience!,