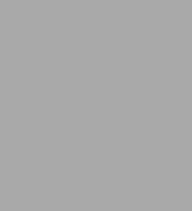
The Natural Colors Cookbook: Custom Hues For Your Fabrics Made Simple Using Food
160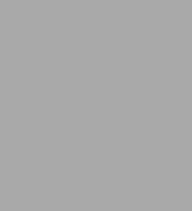
The Natural Colors Cookbook: Custom Hues For Your Fabrics Made Simple Using Food
160Paperback
-
PICK UP IN STORECheck Availability at Nearby Stores
Available within 2 business hours
Related collections and offers
Overview
Discover the wonder of nature’s living colors and transform everyday items with The Natural Colors Cookbook, your guide to creating a spectrum of organic dyes using seasonal produce and leftover food. Now you can bring the timeless form of plant-based dyes to the comfort and familiarity of your own kitchen with the expertise of Maggie Pate, owner and designer of the naturally-dyed clothing label Nåde. Watch in awe as a few hours on the stove extracts a delicate blush tone from a handful of avocado pits, water-soaked black beans release an ashy blue hue and fennel feathers morph into an icy mint. Instead of tossing vegetable trimmings, transform red onion skins into an unexpected olive green, minimizing waste and avoiding harsh chemical dyes.
From selecting among types of natural fibers to mordant and scouring baths, this introduction to hand dyeing covers everything beginners need to know to create a colorful custom palette of textiles. The Natural Colors Cookbook includes simple DIY projects for using your unique dyes, safety tips and precautions, advice for altering hues and instructions for collecting and cataloging colors. It’s an accessible and comprehensive resource every aspiring fiber artist needs.
Product Details
ISBN-13: | 9781624145872 |
---|---|
Publisher: | Page Street Publishing |
Publication date: | 06/19/2018 |
Pages: | 160 |
Product dimensions: | 7.90(w) x 8.90(h) x 0.50(d) |
About the Author
Read an Excerpt
CHAPTER 1
THE BASICS
NATURAL DYEING
For more than 5,000 years, color has been created using plants. From China to Peru and from Morocco to the Americas, the native plants and herbs from each region determine the natural colors that can be produced. Color palettes are unique to each area, similar to food production and growing seasons. Natural dyeing is a way to reconnect with local community, culture, craft and environment.
The first chemical color was created by accident in 1856. From that date forward, it only took 100 years for the craft of natural dyeing to all but vanish. The invention of synthetic dyes transformed our entire perception of color. From color names to the surge of the fashion industry and mass textile production, an entire marketplace was constructed. It is rather astonishing to think that only 150 to 160 years ago all color was created using natural dyes. Now it is a lost art form; like an endangered language, natural dyeing has only been preserved and maintained by remote villagers and small crafters.
The true loss isn't just in the craft and culture of natural colors, but in the magical chemistry as well. A synthetic color only contains one molecule, which means it can only produce one hue. Natural dyes, on the other hand, are made up of multiple molecules, meaning that one natural dye bath can produce a wide range of hues. For example, onion skins can create tones ranging from yellows to pinks to ochres to olives. It is because of this process that natural dyeing isn't just about an end product, it is also an adventure to discover living color.
This book aims to show you how to transform everyday items using universal kitchen staples through the enchanting process of natural dyeing. My hope is that it revitalizes your connection to natural color in an intimate way. It is our history, our culture and our kinship to the earth.
SLOW FOOD
This book explores the natural hues that come from produce, with a focus on compostable remnants and the less-than-perfect items that are deemed unsellable by stores or that simply aren't ideal for consumption. Through this lens, it's only natural that the topic of Slow Food comes up as well.
On a micro level, the Slow Food movement promotes eating locally and cooking traditionally. But it reaches far beyond that. It is a lifestyle that connects our food consumption to greater issues like our social consciousness, ethical beliefs and sustainable practices. It compels us to stop buying premade and processed foods and to instead create our own recipes or find family favorites passed down through the generations. It inspires us to shop locally, to buy from our local farmers and small businesses rather than big chains or superstores.
There is a stigma that the alternative to processed foods and superstores is inconvenient or not accessible, but the opposite is true. Living local, living in season and living slower is all about accessibility and preserving ecology and culture. Decades past have led us, as a society, to become very disconnected from our food sources. Reconnecting with produce revives our connection to our community and environment, and our kinship to culture and craft as well. It is my belief that the maxim and mission of the Slow Food movement can and should reach into all areas of consumerism.
SLOW CRAFT
The cliché "quality over quantity" is the first thing that comes to mind when I think about slow craft. Most people would agree that quality is important, but in the boom of capitalism and mass consumerism, it often takes a backseat to quantity and profit.
Slow craft is a philosophy much like that behind the Slow Food movement. It seems to romanticize the past as it focuses on a more measured way of creating — through simplicity, craftsmanship and respect for the environment. The slow crafter cultivates a relationship with their work, so much so that it is almost meditative. Slow crafters value the history and culture of their craft. They know and care about the origin of their materials and desire to use ethically and environmentally procured supplies. They employ others with ethical and fair practices, and pass their skills on to others. Slow craft urges the crafter to find harmony in creating beyond the pace of mass consumerism.
For me, natural dyeing is a meditation. It gives context to color and our place in this world. Though it demands time and tradition, it exists beyond the world of everyday anxieties and stresses. It isn't about completion, about simply finishing a task and moving on. Instead, the process of natural dyeing is about a spiritual fulfillment. A return to nature, a return to culture and a return to oneness. "Nature does not hurry, yet everything is accomplished" is a quote attributed to Lao Tzu that illustrates this perfectly.
To learn more about Fiber Types, skip to the Fiber 101 section here tohere.
GETTING STARTED
PICKING YOUR FIBER
Whether you are transforming fabric, adding hue to craft supplies or repurposing vintage items, fiber type plays a crucial role in your natural dye project. The type of fiber you are working with guides you to your next steps and impacts your dye results as well. Just like you review the nutritional facts of your food, you should grow accustomed to checking your garment and home textile tags as well, to be aware of the types of fiber you wear and that outfit your space.
Whenever possible, I aspire to source fabric as sustainably as I can. This means researching fiber farms, fair trade textile suppliers and, most importantly, using natural fibers. Synthetic fibers like polyester, nylon and acrylic do not take natural dye color very well, so I steer clear of synthetic fibers as well as fabric blends that have both natural and synthetic materials.
Natural dyeing is a bit like a map or flowchart. The first parameter that will determine your path through the natural dyeing process is your fiber type. Depending on the fiber type you choose, your actions and recipe details will shift. There are two categories of natural fibers — cellulose and protein — which are categorized based on their source. Cellulose fibers are plant-based textiles. Protein fibers are those that come from animals. See the Resources section for more information on the different fibers you can choose from.
Since dyeing is a bit like a flow chart, one step will determine the next. After you have chosen your fiber type, the next two parameters that influence your process are your colorant or dye material and your mordant type. The colorant is the plant or produce that will produce the color, and the mordant is the fastener that allows the natural dye to attach to the fiber. To ease yourself into the process, let's go over the universal steps of natural dyeing!
First, select your fiber. What do you want to dye? What type of fiber is it? Measure the Weight of Fiber (WOF). Then gather your dye material, whether from the garden, refrigerator or farm. Remove the oils and chemicals on your fiber with a Scouring Bath. Begin the Mordant Bathfor your fiber. While the mordanted fiber is cooling, begin your dye bath. Add your fiber to the dye bath. Rinse and dry, then enjoy your naturally-dyed textile!
DETERMINING THE WEIGHT OF FIBER
DETERMINING WOF FOR SCOURING BATH
For cellulose fibers, I recommend using half an ounce (15 g) of soda ash for every 3.5 ounces (100 g) of fiber. If my fiber weighs 21 ounces (595 g), I would create a scouring bath with 3 ounces (85 g) of soda ash.
For protein fibers, I recommend half a teaspoon (2.5 ml) of Synthrapol for every 17.6 ounces (500 g) of fiber. If my fiber weighs 54 ounces (1.5 kg), I would create a scouring bath with 1.5 teaspoons (7.5 ml) of Synthrapol.
DETERMINING WOF FOR MORDANT BATH
For cellulose fibers, I recommend 0.4 ounces (12 g) of Alum Acetate for every 3.5 ounces (100 g) of fiber. If my fiber weighs 16 ounces (454 g), I would create a mordant bath with 2 ounces (57 g) of Alum Acetate (I rounded up).
For protein fibers, I recommend 0.3 ounces (8 g) of Alum Potassium Sulfate for every 3.5 ounces (100 g) of fiber. If my fiber weighs 46 ounces (1.3 kg), I would create a scouring bath with 4 oz (113 g) of Alum Potassium Sulfate.
DETERMINING WOF FOR DYE BATH
In this book, I give dye materials in ratio form. For example, I suggest a 3 to 1 ratio for blueberry dye baths. That means three times the weight of blueberries to the weight of fiber. So if my fiber weighs 7 ounces (200 g), I would use 21 ounces (600 g) of blueberries in the dye bath.
SCOURING BATHS
A scouring bath is a simple deep cleaning that strips the fiber of dirt, waxes, grease and chemical additives that often find their way into textiles during the production and manufacturing stages. Removing these impurities will ensure that the fabric will bind with natural hues more easily. Each type of fabric will have a different type of scouring bath, so pay close attention to whether you are dyeing protein or cellulose fibers (here–here).
WHAT YOU'LL NEED
CELLULOSE FIBER SCOURING BATH
Find your WOF. Calculate how much soda ash you'll need. For every 3.5 ounces (100 g) of fiber add 0.5 ounce (15 g) of soda ash.
In a ceramic bowl, combine the soda ash with 2 cups (480 ml) of warm water. Allow the soda ash to dissolve. Fill an appropriately sized stainless steel pot with water, depending on the amount of fiber you plan to dye. The fiber should be able to float freely in the scouring bath and not be too cramped. Add the soda ash mixture to the stainless steel pot of water.
Place the stainless steel pot on the stove top. Slowly add the fiber to the scouring bath, trying your best to avoid trapping air bubbles. Starting on medium-low heat, bring the temperature of the bath up to 140°F (60°C). Hold the temperature for 30 to 40 minutes. Stir to rotate the fiber every 10 minutes.
Remove the pot from heat. Let the scouring bath and fiber cool to room temperature. Rinse the fiber in cool water and repeat if necessary. If the scouring bath water is a milky amber or brown color, then I suggest repeating the scouring process. If not, move on to your mordant bath.
PROTEIN FIBER SCOURING BATH
Find your WOF. Now calculate how much Synthrapol detergent you'll need. For every 17.6 ounces (500 g) of fiber add 0.5 teaspoon of Synthrapol detergent.
Fill an appropriately sized stainless steel pot with water, depending on the amount of fiber you plan to dye. The fiber should be able to float freely in the scouring bath and not be too cramped. Starting on medium-low heat, bring the temperature of the bath up to 180°F (82°C). Hold the temperature for 30 minutes. Stir to rotate the fiber every 10 minutes.
Remove the pot from heat and let the scouring bath and fiber cool to room temperature. Rinse the fiber in cool water.
MORDANT BATHS
Most natural dyes require a mordant bath to properly bind lasting hues to the fiber. The mordant prepares the natural fibers to successfully attach to natural dyes. There are a variety of mordanting techniques and materials. Some natural dyers add their mordant to the dye bath, while others use separate baths for each. I prefer separating the two, as the mordant material can influence the color results.
Since there are varying mordant materials, natural dyers have a range of preferred mordants for each fiber type depending on the natural dye they will be using. Some crafters use metal mordants like aluminum, iron and copper, and some use natural mordants like cream of tartar, rhubarb, chalk, wheat bran and soy milk. Some might even use a combination of metal and natural mordants. To keep from complicating this book and exhausting those who are new to dyeing, I chose to share the mordant baths that are most successful for me and the two that I use most frequently. But I encourage you to experiment with your mordants and explore how they affect dye results and coloration.
Some natural dyes are substantive dyes, which means their pigments can directly bond to a natural fiber on their own. This is called an anthocyanin pigment, but be careful assuming that these dyes will last. It doesn't mean that they are lightfast pigments — they may still require a mordant to retain hue. Other dyes are called adjective dyes, which means they definitely need a mordant to keep the color bonded to the fiber. I always employ the cliché "better be safe than sorry" when it comes to mordant baths. I would rather mordant a fiber than assume it will be fine without, only to then be disappointed when all that color and effort rinses out.
WHAT YOU'LL NEED
CELLULOSE FIBER MORDANT BATH
Wear a mask and gloves to protect yourself from the alum acetate. For every 3.5 ounces (100 g) of fiber add 0.4 ounces (12 g) of alum acetate. In a ceramic or glass bowl, combine 1 cup (240 ml) of warm water with the alum acetate needed based on your WOF. Allow the alum acetate to dissolve in the water, lightly stirring every so often.
Fill an appropriately sized stainless steel pot with water, depending on the amount of fiber you plan to dye. The fiber should be able to float freely in the scouring bath and not be too cramped.
Place the stainless steel pot on the stove top, then slowly add the scoured and rinsed fiber to the mordant bath while it is still wet. Fibers achieve best results when they are wet before entering mordant and dye baths. Try your best to avoid trapping air bubbles in the mordant bath.
Starting on medium-low heat, bring the temperature to 180 to 190°F (82 to 88°C). Hold the temperature for 1 hour, stirring and rotating the fibers every 10 to 15 minutes. Remove the pot from heat and allow the mordant bath to slowly cool. Cellulose mordant baths are most successful if you let the fiber rest in the bath for at least 2 and up to 24 hours.
Rinse the fiber in lukewarm water, then either move on to a dye bath or store your mordanted fibers in a plastic bag in a dark space for up to three days. Just make sure to use them before they mold due to dampness.
PROTEIN FIBER MORDANT BATH
In a ceramic or glass bowl, combine 1 cup (240 ml) of warm water with the alum potassium sulfate needed based on your WOF. For every 3.5 ounces (100 g) of fiber add 0.3 ounces (8 g) of alum potassium sulfate. Allow the alum potassium sulfate to dissolve in the water, lightly stirring every so often.
Fill an appropriately sized stainless steel pot with water, depending on the amount of fiber you plan to dye. The fiber should be able to float freely in the scouring bath and not be too cramped.
Place the stainless steel pot on the stove top, then slowly add the scoured and rinsed fiber to the mordant bath while it is still wet. Fibers achieve best results when they are wet before entering mordant and dye baths. Try your best to avoid trapping air bubbles.
Starting on medium-low heat, bring the temperature to 180 to 190°F (82 to 88°C). Hold the temperature for 1 hour, stirring and rotating the fibers every 10 to 15 minutes. Remove the pot from the heat and allow the mordant bath to slowly cool to room temperature.
Rinse the fibers in lukewarm water, then either move on to a dye bath or store your mordanted fibers in a plastic bag and in a dark space for up to three days. Just make sure to use them before they mold due to dampness.
NO MORDANT NECESSARY
Sometimes the dye material you are using will not require the use of a mordant bath because it will have naturally occurring tannins in the plant. For example, onion skins, sumac, rhubarb and avocado pits do not require a mordant bath. But it also never hurts to do one.
A NOTE ON DYE RECIPES
There is a long and extensive history of natural dyeing, which means that there is a wide range of dye recipes. Recipes tend to be specific to certain regions, and are subject to the time period and the materials available when they were written. Over the years, master dyers have sought to translate old recipes for current use, but that is often an impossible task. Ancient recipes from the medieval period are riddled with puzzling details and subjective nuances — for example, some call for a walk or a prayer to specify time passing in a recipe. Such directions are amusing, but not exactly helpful to us these days.
Since I began my exploration into natural dyeing, I have noticed that books I've sought to learn from only ever list a master dye recipe. This can certainly be helpful for beginners, but different dye materials can require varying techniques. Some perform best with long sustained heat while others burn easily over time. This book treats every dye material differently, which is why every dye bath has its own recipe. This may seem redundant to some, but I know that when I began natural dyeing, this approach would have been a great resource to me.
(Continues…)
Excerpted from "The Natural Colors Cookbook"
by .
Copyright © 2018 Margaret Pate.
Excerpted by permission of Page Street Publishing Co..
All rights reserved. No part of this excerpt may be reproduced or reprinted without permission in writing from the publisher.
Excerpts are provided by Dial-A-Book Inc. solely for the personal use of visitors to this web site.
Table of Contents
Introduction 9
The Basics 13
Blushes & Burgundies 27
Peaches & Oranges 45
Ochres & Yellows 59
Earth Tones & Neutrals 81
Greens 95
Blues & Purples 117
Resources 135
Bibliography 150
Acknowledgments 152
About the Author 155
Index 156