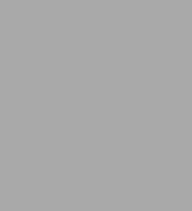
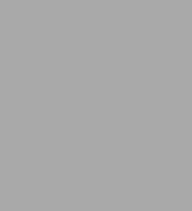
eBook
Available on Compatible NOOK devices, the free NOOK App and in My Digital Library.
Related collections and offers
Overview
This unique book provides a starting point for more in-depth surveys of past and recent work in all aspects of vacuum coating. The author uses his extensive knowledge of the subject to draw comparisons and place the information into the proper context. This is particularly important for the patent literature where the terminology does not always match industry jargon. A section of acronyms for vacuum coating and glossary of terms at the end of the book are critical additions to the information every reader needs.
Product Details
ISBN-13: | 9780815519270 |
---|---|
Publisher: | Elsevier Science |
Publication date: | 04/16/2003 |
Sold by: | Barnes & Noble |
Format: | eBook |
Pages: | 150 |
File size: | 3 MB |
About the Author
Read an Excerpt
The Foundations of Vacuum Coating Technology
By Donald M. Mattox
Elsevier
Copyright © 2003 Noyes Publications / William Andrew PublishingAll rights reserved.
ISBN: 978-0-8155-1927-0
CHAPTER 1
Early Vacuum Science and Technology
(General References [5-9])
In about 1640, Otto von Guericke made the first piston-type vacuum pump (which he called air pumps) patterned after the water pumps that had been used for many years to remove water from mines. Figure 1 shows a woodcut picture of a mine being pumped out using several stages of water pumps. In 1654 von Guericke performed the famous Magdeberg hemispheres demonstration that really introduced the vacuum pump to the scientific world. In 1643 Torricelli demonstrated the mercury barometer based on the water manometer experiments of Berti (~1640). In 1662 Boyle formulated Boyles Law, and in 1801 Dalton expressed the Law of Partial Pressures. Piston-type vacuum pumps came into widespread use, but vacuum experiments had to be continually pumped because of the poor vacuum seals available at that time.
In the early to mid-1800s, heat-moldable, electrically insulating materials included gutta-percha, a material made from the sap of a tree native to Southeast Asia (F. Montgomery brought this to Europe, 1843); the molded plastic made from shellac and sawdust (and later coal dust) (H. Peck & C. Halvorson, Norway, 1850); and India rubber, which was made from rubber tree sap, sulfur, and gum shellac (G. Goodyear, 1851). L. Baekeland invented Bakelite, the first totally synthetic thermosetting plastic, in 1907. Glass forming (ancient) and porcelain fabrication (W. Bottger, Germany, 1710) were well understood by the mid-1800s.
In 1857 H. Geissler invented the platinum-to-glass seal that allowed sealed-off vacuum tubes to be produced. This was a major advance in vacuum technology. Neoprene (artificial) rubber was invented by DuPont in 1933, and molded seals of this material began to be used by the vacuum community in the late 1930s and replaced wax sealing. As late as the 1960s, finding and fixing vacuum leaks was a major part of vacuum technology and Glyptol (a paint—GE), black wax (Apiezon—W) and elephant s—" (a putty) (Apiezon—Q) were common fixtures in the vacuum facility. Many of the early experiments used hydrogen flushing to augment vacuum pumping to reduce oxygen in the chamber. During WWII the Germans used phosphorus pentoxide, a desiccant, in the vacuum chamber to remove water vapor when depositing optical coatings.
In 1855 H. Geissler invented the mercury piston pump, which was widely used but left mercury vapor contamination in the vacuum (mercury has a vapor pressure of 1.2 mTorr at room temperature). Töpler improved the Geissler pump, and in 1865 Sprengel invented the mercury siphon pump, which greatly reduced the labor and attention required for vacuum pumping. In 1874 McLeod invented the McLeod vacuum gauge, which was capable of measuring very low pressures. By using a combination of Geissler and Sprengel vacuum pumps, cold trapping and flaming, good vacuums (about 10-6 atmospheres) could be achieved. Thomas Edison used this combination of techniques in the production of the first carbon-filament electric light bulbs in 1879. Figure 2 shows vacuum pumping, 1880s style. It was not until about 1895 that liquefied air was used to trap mercury vapor pumps. This was after T. Linde and J. Hampson had introduced regenerative cooling as a means of liquefying gases and J. Dewar invented a means for storing liquefied gases (Dewar flask). In 1901 H.C. Booth invented the first electrically-driven vacuum cleaner. The term vacuum cleaner was first used in Booths advertisements.
In 1907 W. Gaede invented the oil-sealed rotary vane mechanical pump. By 1910, electric-motor-driven, oil-sealed, rotary vane pumps were in common use. In 1913 the mercury diffusion pump was invented by I. Langmuir and was improved by W. Gaede in 1922. In 1926 C.R. Burch replaced the mercury with low-vapor pressure oil, though well-trapped mercury diffusion pumps were considered the cleanest high-vacuum pumps for many years afterward. In 1937 L. Malter built the first metal oil diffusion pump; until that time fractionating and non-fractionating diffusion pumps were made of glass. The oil diffusion pump (diff pump) has remained the principal high-vacuum pump used on many large vacuum coating systems. During WWII, the company Distillation Products, Inc. (later Consolidated Vacuum Corp.—CVC) and National Research Corporation (NRC—later a division of Varian Corp.) were the major suppliers of vacuum equipment to the vacuum coating industry.
Cryopumps and turbomolecular pumps have widespread use in the vacuum coating industry where small chambers are pumped or where oil contamination is a major concern. The cryopump developed from the use of cold traps in vacuum chambers and also cold shrouds in space simulators. Liquid helium cooling developed after the invention of the closed-loop helium cryostat (Gifford-McMahon cycle) in 1960 but did not come into widespread use until 1980, when Varian Corp. began marketing cryopumps. W. Gaede invented a turbopump in 1912, but the modern vertical-axis, high-RPM turbopump was developed independently in 1958 by H.A. Steinhertz and by W. Becker. Pfeiffer Corp. began marketing turbopumps in 1958.
In the mid-1990s molecular drag stages were added to turbomolecular pumps. This technology allowed turbopumps to exhaust to higher pressures so diaphragm pumps could be used as backing pumps. This combination allowed very oil-free pumping systems (dry pumps) to be developed for critical applications. The use of piston pumps also returned due to the need for clean, dry pumps. Ultra-clean vacuum components (and their packaging) and vacuum systems were developed for the semiconductor industry around the late 1960s.
In 1906 W. Voege invented the thermocouple vacuum gauge, and in 1909 M. von Pirani invented the Pirani gauge. That year the hot cathode ionization gauge was invented by Von Baeyer. The modern Bayard-Alpert hot cathode ionization gauge was invented by R.T. Bayard and D. Alpert in 1950. W. Sutherland (1897), I. Langmuir (1913), and J.W. Beams (1960) advanced the concept of various viscosity (molecular drag, spinning rotor) gauges. Beams high-speed rotor work was the basis of the modern spinning rotor (molecular drag) gauge. The modern capacitance manometer gauge was invented by A.R. Olsen and L.L. Hirst in 1929 but did not become commercially available until 1961 when MKS Corporation began marketing it. F.M. Penning invented the magnetron cold cathode ionization gauge in 1937. In 1922 S. Dushman wrote the classic book Production and Measurement of High Vacuum. Helium leak detectors and many other advancements in vacuum technology were developed during WWII in support of the isotope separation project.
In the early years vacuum chambers were predominately single chambers, though Edison patented a dual-chamber vacuum system in the early 1900s to speed up production of light bulbs. With the advent of integrated circuit (IC) technology in the 1960s the need for high volume production of substrates having several layers deposited on them led to the development of several types of chambers including the open-ended and closed-ended in-line systems. Several systems were patented that had a central vacuum transfer chamber. A problem with these central-chamber designs was probably the complicated transfer mechanisms needed. In 1987 Applied Materials Inc. introduced the first commercial multiple-chamber cluster tool for semiconductor processing. This system was used for sequential deposition of doped and undoped PECVD films with an intermediate plasma-etching step. These cluster tool systems later allowed very precise pick-and-place movement of wafers from a central cassette into processing chambers in a random sequence. Also in the 1960s coating on strip metal was being developed. This led to the fabrication of thin metal foils by depositing difficult to fabricate metals, such as beryllium, on a mandrel and then removing it in a continuous manner.
With the advent of reactive deposition and hybrid processing, the control of gas composition and mass flow has become an important aspect of vacuum engineering and technology. This includes partial pressure control and gas manifolding in processing chambers. Many vacuum measurement instruments cannot be used for measurement of total gas pressures in the presence of a plasma in the range of interest to many PVD processes (0.5 to 20 mTorr). Capacitance manometer gauges and spinning rotor gauges are commonly used in these applications. Differentially pumped mass spectrometers can be use to monitor and control partial pressures of gases. In 1984 a mass spectrometric feedback method of controlling the partial pressure of reactive gases in reactive sputter deposition was patented. Optical emission spectroscopy is also used to control the partial pressures of reactive gases in reactive sputter deposition. Optical emission has been used for many years to detect the end-point in plasma etching for semiconductor processing.
The use of vacuum equipment for deposition (and etching) processes also introduces problems associated with pumping and disposing of possibly toxic, flammable, and corrosive processing gases, as well as reactive gases used for in situ cleaning of the vacuum systems. Specialized vacuum equipment and in situ chamber plasma-etch-cleaning techniques have been developed to address these concerns.
An important aspect of vacuum coating processing is often how to create a vacuum rapidly and reduce the water vapor contamination quickly. In creating a clean vacuum the problem of water vapor moving from its point of origin to the vacuum pump by way of numerous adsorption-desorption events on surfaces is often the controlling factor in removing water vapor from the chamber.
The term vacuum should be used with caution because it means different things to different people. To some people the term vacuum means that the gas density is so low that the gaseous species do not affect the process or phenomena being studied. To others it means a sub-atmospheric gas density that should, or must, be controlled during the process or study in order to have reproducible results. For example, in Jim Laffertys 1980 book Vacuum Arcs he makes a point of saying, If there is an arc there is no vacuum and where there is a vacuum there is no arc.
CHAPTER 2
Early Electricity and Magnetism
(General References [16-18])
In 1600 W. Gilbert wrote the book De Magnete (On The Magnet). This book is considered to be the first scientific publication. In 1672 Otto von Guericke (of vacuum pump fame) built the first electrostatic (frictional) electricity-generating machine, which used a rotating ball of sulfur. Friction electricity was used for entertainment in the early years (E-2). In 1732 Gray described the conduction of electricity, and about 1745 the air capacitor (Leyden jar) was invented by von Kleist, which allowed electricity to be stored. The invention of the Leyden jar is sometimes erroneously credited to Prof. van Musschenbroek at the University of Leyden in The Netherlands. In 1749 Benjamin Franklin introduced the concept of positive and negative electricity and the conservation of charge. Franklin also introduced the word battery for a bank of Leyden jars (E-3). In 1800 Alessandro Volta invented the electrolytic voltaic pile (later called a battery) based on the observations of animal electricity by Luigi Galvani (1791) and others (see Figure 3). The science of electrochemistry had its beginning at that time—for example, the electrodeposition of copper (Cruikshank in 1800) and electrolysis, which allowed the separation of oxygen and hydrogen from water (an accidental discovery by Nicolson and Carlyle in 1800). Napoleon Bonaparte was immediately interested and supported the construction of very large arrays of batteries, as did others. For example, the Russians built an array of 4,200 Cu-Zn cells in 1803 at St. Petersburgs Medical and Surgical Academy. In 1810 Sir Humphry Davy produced a manmade arc between two electrodes. (Arc is from the word arch, which is the shape of a long arc between two electrodes in air due to heating and convection.) Davy is generally credited with producing the first manmade arc, although a Russian, Vasilli V. Petrov, reported the same effect in 1803.
In 1820 H.C. Oersted detected the magnetic field around a current-carrying wire, and in 1821 Ampére invented the galvanometer. In 1831 Michael Faraday discovered electromagnetic induction. The first continuous generation of electricity, both AC and DC, using induction was developed by Hypolite Pixii in 1832. M. Nollet improved Pixiis design in 1849 or 1850. This led to the first commercial use of mechanically generated electricity. In 1836 N.J. Callan made the first induction coil to produce pulses of high voltages by periodically making and breaking a DC circuit. In 1851 H.D. Rühmkorff built a high-quality induction coil (Rühmkorff coil) that allowed the generation of high voltages, and this device was widely used with gas-discharge tubes for many years.
(Continues...)
Excerpted from The Foundations of Vacuum Coating Technology by Donald M. Mattox. Copyright © 2003 Noyes Publications / William Andrew Publishing. Excerpted by permission of Elsevier.
All rights reserved. No part of this excerpt may be reproduced or reprinted without permission in writing from the publisher.
Excerpts are provided by Dial-A-Book Inc. solely for the personal use of visitors to this web site.
Table of Contents
Early Vacuum Science and TechnologyEarly Electricity and Magnetism
Early Plasma Physics and Chemistry
Some Scientific and Engineering Societies and Publications
Patents and the U.S. Patent Office
Deposition Processes
Summary
Endnotes
References
Acronyms Used in Vacuum Coating
Glossary of Terms for Vacuum Coating
What People are Saying About This
A review of the development of the varied applications of vacuum coating technologies in use today