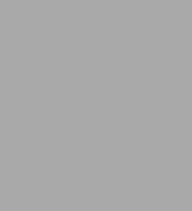
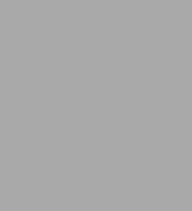
eBook
Related collections and offers
Overview
Product Details
ISBN-13: | 9781615643707 |
---|---|
Publisher: | DK |
Publication date: | 08/06/2013 |
Sold by: | Penguin Group |
Format: | eBook |
Pages: | 240 |
Sales rank: | 891,750 |
File size: | 16 MB |
Note: | This product may take a few minutes to download. |
About the Author
Table of Contents
1 Setting Up Your Workspace 2
Appreciate Metal's Appeal 3
Choose Your Place 3
Plan Your Space 4
An Easy Organization System 5
Find the Right Work Surface 6
Workbench Features 6
The Role of the Bench Pin 7
Good Work Surfaces on a Budget 8
Play It Safe 9
2 Choosing Tools and Equipment 10
My Tool Philosophy 11
Source Tools Creatively 11
Know When to Spend and When to Save on Tools 12
The Tools You Need to Get Started 13
Basic Torch Setups 15
All-in-One Torches 15
Jewelers Torches 17
Plumber's Torch 18
Torch Workstation Checklist 18
Safe Torch Practices 20
Specialty Equipment 21
3 Understanding Metal Materials 24
Knowing Your Materials 25
Defining Metal Types and Properties 26
Preparing Your Metal 27
Annealing Metal 28
Work-Hardening Metal 32
Recycling Metal 34
Saving Your Scrap 34
Reusing Scrap 34
4 Designing Jewelry 36
Dreaming in Metal 37
Recording Design Ideas and Finding Inspiration 37
Using Paper Models to Work Out Your Design 39
Executing Your Designs 41
5 Moving Metal 44
Understanding Metal Hardness 45
Bending Metal Sheets and Wire 46
Discovering a World of Shaping Tools for Metal 46
Dapping Metal 48
Scoring Metal 49
Forging Metal 50
The Importance of Every Hammer Blow 51
Basic Hammer Shapes 51
Fundamental Hammering Techniques 52
Foldforming 54
6 Sawing and Piercing Metal 58
Working with a Jeweler's Saw 59
How to Handle a Jeweler's Saw 60
How to Load a Saw Blade 62
How to Use Bench Pin When Sawing 64
Why Saw Blade Lubricants Are Optional 65
Using Low-Tech Piercing Methods 65
The Simplest Hole Punch 65
Hole-Punching Pliers 66
Drilling 67
Supply List and Basic Drilling Preparation Steps 67
Hand Drills and Spiral Hand Drills 68
Motorized Drills 69
Drill Bits 73
7 Filing and Smoothing Metal 74
Filing 75
Basic File Facts 75
Types and Shapes of Metal Files 76
Filing Techniques 78
Special Care for Your Files 80
Sanding 81
Select the Right Sandpapers and Abrasives 81
Understand the Three Major Types of Sanding 83
Polish with Sandpaper 83
Burnishing 84
What You Can Achieve Through Burnishing 84
What to Use as a Burnisher and How to Use It 84
8 Joining Metal 86
Rivets and Other Cold Connections 87
Making and Using Rivets 88
Making Wire Rivets 89
Making Tube Rivets 91
Customize Your Rivets 93
Making and Using Slots and Tabs 94
Glues 95
Rubber Cement 96
Two-Part Epoxy 96
Hot Connections 97
What Is Solder? 97
What Supplies Do I Need for Soldering? 99
How Do I Solder? 100
What Are the Types of Solder Operations and When Do I Use Them? 102
What Else Should I Know About Soldering? 104
What Are the Basic Steps for Soldering? 105
9 Creating Surface Textures and Impressions 106
Creating Textures with Hammers 107
Making Scratch Textures 109
Hand Tool Textures 109
Power Tool Textures 110
Stamping Metal 111
Gathering Your Tools and Preparing Your Metal 111
Creating the Impression 112
Etching 114
Handling Chemicals Safely 114
Gathering Supplies and Applying a Design 115
Etching Copper and Brass with Ferric Chloride 117
Photo Etching 119
Other Texture Options 120
Chasing and Repoussé 120
A Rolling Mill 120
A Car 121
10 Coloring Your Metal 122
Patina from a Metalsmith's Perspective 123
Low-Tech Patinas from Household Items 124
Preparing Metal for a Patina 124
Creating Home-Brew Patinas 125
Creating a Fumed Ammonia Patina 126
Creating a Direct-Contact Ammonia Patina 128
Creating a Peanut Oil Patina 129
Next-Step-Up Chemical Patinas 130
Preparing Your Jewelry and Gathering Supplies 130
Cooking the Patina 131
Coloring Then Neutralizing 132
Finishing 132
Overview of Other Techniques 134
Colored Pencil 134
Alcohol Inks 134
Heat Patina 135
Enameling 135
11 Adding Gems and Embellishments 136
Buying Gems 137
Gemstone Characteristics 138
Shop for These Stones First 139
Setting Gems 140
Basic Gemstone Settings 140
Basic Soldered Setting 141
Basic No-Solder Setting 146
Using Found Objects 147
12 Making Chains and Other Findings 148
Jump Rings 149
Chains 150
Supplies for a Handmade Chain 150
Steps for Making a Simple Chain 151
Closures and Clasps 153
Bails and End Caps 155
Bail Styles 155
End Cap Styles 155
Pin and Brooch Mechanisms 157
Ear Wires 160
13 Finishing Touches 162
Polishing Your Work 163
Sample Hand-Polishing Progression 163
Polishing Compounds 164
Power Tool Polishing 165
Preserving the Finish 167
Choosing a Wax or a Varnish 168
Applying Waxes and Varnishes 169
Taking Care of Your Jewelry 170
Maintaining Your Jewelry 170
Removing Tarnish 170
Reapplying Wax or Varnish 172
Enjoying the Natural Progression of Metal 173
14 Creating Metal Jewelry: 10 Projects 174
Basic Setups for the Projects 175
Ginger Forged Necklace 178
Glow Forged Copper Cuff Bracelet 179
Leaves Earrings with Blue-Green Patina 182
Tendril Pendant 183
Vine Earrings 185
Paging Ms. Heroine Wide Copper Cuff Bracelet 187
I Love Lacy Pierced and Riveted Pendant 189
Cut Out the Silver and Copper Patterns 189
Rivet the Pieces Together 190
Manhattan Harley Cuff Links 193
Solder the Copper Hubs to the Silver Discs 193
Add Texture and Shape the Cuff Links 194
Honeycomb Geometric Brooch 196
Saw the Shapes 197
Solder the Pin Catch Assembly 198
Captured Canyon Gemstone Prong Setting 201
Design the Setting and Assemble the Pieces 202
Solder the Prongs and Set the Stone 203
Appendixes
Glossary 206
More About Metal 212
Index 216