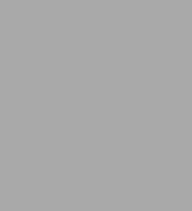
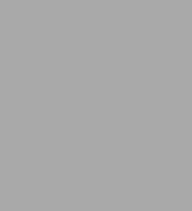
Paperback
-
PICK UP IN STORECheck Availability at Nearby Stores
Available within 2 business hours
Related collections and offers
Overview
Product Details
ISBN-13: | 9781600851285 |
---|---|
Publisher: | Taunton Press, Incorporated |
Publication date: | 02/02/2010 |
Pages: | 228 |
Sales rank: | 129,706 |
Product dimensions: | 9.40(w) x 9.90(h) x 0.70(d) |
About the Author
An award-winning artist, Lisa Pavelka is recognized internationally as an authority on polymer clay. She has written three other books on the topic and regularly contributes columns and articles to "Family Circle, Belle Armoire, "and "Polymer Cafe." She has appeared on "The Carol Duvall Show, DIY's Jewelry Making," and "Beads, Baubles and Jewels" on PBS. She teaches workshops, leads crafting cruises, conducts trade-show demonstrations, and holds seminars on crafting with polymer clay. She lives in Las Vegas, Nevada.
Read an Excerpt
The Complete Book of Polymer Clay
Step-by-Step Instructions Original Projects Inspirational GalleryBy LISA PAVELKA
The Taunton Press
Copyright © 2010 Lisa PavelkaAll right reserved.
ISBN: 978-1-60085-128-5
Chapter One
Polymer Clay Essentials
YOU MAY BE WONDERING, "What, exactly, is polymer clay?" As opposed to earthenware clay, polymer clay is a manufactured modeling compound that remains soft until heated in an oven. Without getting too technical, polymer clay is a combination of polyvinyl chloride (PVC), plasticizer, and pigments. It bakes at low temperatures, typically between 230?F and 275?F. This allows you to bake it with a large number of materials that don't burn or melt at these low temperatures, like paper.
I have always maintained that polymer clay is the most versatile and forgiving medium on the planet. It is probably the most diverse; its fans and enthusiasts include children, hobbyists, model makers, jewelry makers, doll artists, professional crafters, and fine artists. It can be used for household repairs, like filling cracks in tile. It can even be drilled, carved, painted, sanded, polished, riveted, hinged, coiled ... the list goes on and on.
A Brief History of the Medium
German doll artist "Fifi" Kruse Rehbinder developed a moldable material to use in the making of her doll heads in the 1930s. The compound was initially called "Fifi Mosaik." After the sale of the formula to German company Eberhard Faber in the 1960s, the company condensed the beginning of both names to rebrand the product FIMO[R].
The next major product introduction to the clay world occurred in the 1960s, when Zenith Products Company, in Illinois, began selling a coating made for industrial use and as a modeling compound for hobby and crafting purposes. This was the very first Sculpey[R] product.
Polymer clay continues to undergo frequent changes and improvements. This is a tremendous plus for clay users everywhere. Improvements and additions to formula, strength, colors, durability, and safety are always under way.
Even though polymer clay has always been certified as nontoxic and, by all reports, safely used since its introduction, the manufacturers listed on pages 216-217 have removed phthalates, plasticizers common in use since the 1930s, from their clays as a safety precaution after the European Parliament banned these chemical compounds from toy manufacture in 2005. In 2009, the United States also banned phthalates from certain products. Fortunately, all of the major clay brands have complied with the European ban already in effect.
Types of Polymer Clay
There are several clay options available through craft stores and Internet resources, each with different benefits and limitations in regard to workability, strength, flexibility, firmness, working time, and a variety of other elements. Clay properties are discussed below under the individual clay brands.
The best determining factor for deciding which clay to work with is personal experience. The following is offered as a brief explanation of the most commonly available clays at the time of publication.
Most clay is sold in small bricks, typically weighing 2 oz. or more. The new Pardo clay by Viva Décor is sold in balls from packages of six balls (1.2 oz.) to larger jars of 2.65 oz. Some of these clays are also available in bulk-size bricks that range in size from 12 oz. to 16 oz. The best sources for the larger bricks of clay are catalogs and Internet sites. Many brands also offer color samplers in 1-oz. bars.
Generally speaking, all clays have an indefinite shelf life if properly stored. However, the amount of time clay remains in the conditioned state depends on the firmness of the clay.
There are more than a few brands of polymer clay that are designed for bulk or sculpting use (and come in only one color). For example, one bulk package that is a skin-tone base for doll sculpting is Polyform Super Sculpey[R]. (These will not be reviewed in the interest of simplicity.)
One great thing about working with clay is that, for the most part, it is not an expensive medium. While price fluctuations continue to occur within the retail market, the current cost of a small block or container ranges from two to three dollars. It follows that buying larger bulk bricks is usually less expensive.
The following is a breakdown of the most common polymer clay types.
CERNIT[R]
This clay is a favorite of doll makers because of the range of flesh-tone colors available and lifelike skin-tone translucency after baking. It can be somewhat difficult to condition, but it bakes very firm and strong with a good degree of flexibility. It's available in more than 60 colors.
FIMO CLASSIC
Originally only referred to as FIMO, FIMO Classic is the oldest and most widely recognized of the polymer clays due to its history. This clay is a favorite among fine artists and caners. It is one of the strongest and most resilient clays after baking, offering an excellent degree of flexibility. FIMO Classic bakes with a matte finish and is available in 24 colors.
FIMO SOFT
This is one of the easier clays to condition. A few seconds of kneading right out of the package is usually sufficient. FIMO Soft also offers the least amount of resistance or "blade drag" when slicing, even when very soft and warm. It has good strength and flexibility after baking. It also offers one of the longest "open times" for working the clay as well as superior shelf life for millefiori canes | see MILLEFIORI CANING, chapter 4, page 44 |. It bakes with a matte finish and is available in more than 50 colors.
KATO POLYCLAY[TM]
This clay is one of the newest brands, introduced earlier in this century. It can be stiff out of the package and take longer to condition, but it offers excellent strength and flexibility after baking. It bakes with a slight sheen and is available in 17 colors.
PARDO
This is the newest clay. It offers easy conditioning, superior strength, and re-usable packaging. It comes in over 70 colors.
PREMO! SCULPEY[R]
This clay offers a medium-soft consistency and bakes with excellent strength and flexibility while still being easy to condition. It is known for being stickier than other brands, which can be an advantage when, for example, you are doing the Sutton Slice and a limitation when you are rolling out long strips of clay such as with Skinner Blended bulls' eyes. It bakes with a slight sheen finish and is available in more than 30 colors.
SCULPEY III[R]
One of the first clays to be introduced in individual colors, this clay is very soft and easy to condition and offers good open time. It bakes firm with a matte finish, but it is not flexible and tends to be brittle after baking. This clay is best suited for projects with density and bulk, and it is available in more than 40 colors.
STUDIO[TM] BY SCULPEY
Softer than its sister clay, Premo! Sculpey, this clay offers easy conditioning. The feel is lighter and less dense than other clays, and it bakes with a matte finish. Its strength and flexibility are good, and it's available in more than 30 colors.
Liquid Clay
Liquid clay was first introduced in the 1990s. It remains an innovative addition to the polymer clay world and offers infinite possibilities. It can be used as a primary medium, especially when colored with oil-based paint, alcohol inks, or powdered pigments.
When adding color, mix only a drop or two at a time until the desired color is achieved. Try mixing some batches of colored liquid clay and store in small plastic bottles. Another handy way to prepare colored liquid clay is to fill empty paint pot strips, which are available at most craft stores.
Here are a few of the other applications for liquid clay:
It can be used as an adhesive to bond clay layers together.
You can use it to make image transfers, | see IMAGE TRANSFERS, chapter 5, page 62 |.
You can add inclusions such as mica powder, glitter, and fibers to create specialty and stonelike effects.
It makes an excellent sealer for foils, leafing, and transfers.
It can even be used as a paper laminate.
Because the clay is liquid, you don't need to worry about having an uneven surface after you apply it. On the other hand, when using it as a sealer, be careful not to apply it too thickly, or the result will be a milky or cloudy surface. Sanding and buffing can be done after baking to polish and increase the clarity of thicker layers of polymer clay. Adding shine can also be achieved by adding glosses or glazes to cured layers of liquid clay.
APPLYING LIQUID CLAY
Liquid clay can be poured directly from the bottle or can be applied with a toothpick for detailed applications, with a fingertip, or by brush. (A high-quality hair or synthetic brush is recommended. Inferior brushes may lose bristles during application.) Once a brush has been used for liquid clay, it must remain dedicated to that clay use, as you will not be able to clean out all of the material.
Care for these brushes by wiping all the excess clay out of the bristles with a paper towel. Always stroke the towel in the direction of the bristles, away from the handle. Cover brushes with a small plastic bag with the handle facing down when stored. This will prevent dust and debris from contaminating the brush when not in use. Clean up liquid clay with baby wipes or alcohol.
Over time, the liquid clay may begin to thicken and firm up. To recondition a liquid-clay brush, work a few drops of fresh medium into the bristles to soften the old buildup. Drag the tip of a toothpick through the bristles to loosen and remove the excess clay. Wipe with a paper towel and repeat as needed until the brush is clean.
An alternative method for curing liquid clay is to use a heat gun designed for embossing powders. You can visibly see when the clay has set. The sheen will disappear, marking a change in the surface tension, indicating the clay has cured.
Liquid clay is commonly available in 2-oz. bottles, but indicated (*) brands below also come in 8-oz. sizes.
FIMO LIQUID DECORATING GEL
This is the clearest of the liquid clays and also has the lowest viscosity (thickness). It is highly flexible after baking. Extremely thin layers provide a matte finish, and thicker layers create a satiny gloss finish.
* KATO LIQUID POLYCLAY[TM]
This liquid clay offers the second greatest clarity and has a medium thickness. It cures with the most flexibility and results in a satiny gloss finish in thick or thin applications.
* TRANSLUCENT LIQUID SCULPEY
This is the thickest of all liquid clays and has the least amount of clarity when cured. It can be thinned with Sculpey Diluent, which can also help when conditioning stiff clay. It cures hard and firm with a matte finish.
heat gun safety tips
Heat guns emit temperatures in excess of those recommended, making it possible to scorch or burn your clay.
First, make sure the work area is clean of uncured clay and any other flammable materials before working with a heat gun.
Tie your hair back and make sure any loose clothing is secured. Hold the gun about 3 in. to 5 in. away from the clay, moving it continuously in circles until the clay is cured.
The tip of the gun will be very hot after using. Allow it to cool before storing, about 10 to 15 minutes.
Safety First
In classes, I usually offer two rules for working with polymer clay: "Don't eat it and don't burn it," followed by, "Everything else is just a suggestion!" While that is basically true, there are some specific safety issues that must be shared.
1 Never leave uncured clay on a painted, varnished, or lacquered surface. Baked clay is inert and cannot harm furniture.
2 Polymer clay is rated as nontoxic, but it is not recommended for food use. Kitchen tools used for working with clay should remain craft or clay dedicated.
note
Shine occurs when baking on smooth surfaces like tile, but it can be removed with a light sanding with 1,000-grit or higher sandpaper.
note
Paper can curl when baking. For very thin pieces of clay, it can be helpful to bake directly on the tile or weight down the clay with a book after baking, to flatten.
You can't eat or drink from polymer clay, so don't even think about using anything made of clay for utensils or dishware. On the other hand, using it to embellish handles or the bases of stemware that don't come into contact with anything edible is fine.
3 Always clean hands thoroughly before handling food after working with clay. Use a pumice-based, waterless hand cleaner (available in the automotive section of many stores) or hand sanitizer to dissolve the clay residue. Follow with soap and water.
4 Never leave baking clay unattended! If clay appears to be smoking or burning, turn off the oven, remove the clay, and place it outdoors until cool. Ventilate the room.
5 Wear protective eyewear and use a dust mask or dust cabinet when carving, dry sanding, machine buffing, or drilling clay.
Work Surfaces
A smooth ceramic tile is the best work and baking surface. It's inexpensive and almost impervious to scratching, and it can go directly from your worktable into the oven. You may want several for your workstation.
Parchment-type deli paper (also known as patty paper) is ideal when you do not want your clay to stick to the work surface. (You'll soon discover when you want your clay to stick to the tile and when you don't.) Working with paper allows you to remove worked clay from your tile without stretching or distorting it.
You can find this type of paper in bulk at grocery warehouses and restaurant supply stores. You can even bake on it to prevent shiny spots from forming on the underside of your clay.
Clay Conditioning and Handling
All polymer clays must be conditioned, no matter how soft. Conditioning is the redistribution of all the ingredients that may have settled during storage. Failure to condition may lessen the finished strength of your baked clay. Clay is adequately conditioned when you can fold it without cracking.
Softer clays like FIMO Soft, Pardo, and Sculpey III can usually be conditioned straight out of the package by hand kneading for a minute or two. Slicing sheets from the block and repeatedly rolling them through a pasta machine several times is also a great way to condition your clay.
Leaching is a process by which plasticizer is removed from the clay. Although this technique will make the clay firmer to work with, it should be noted that it can also lessen the finished strength of the piece.
To begin the leaching process, sandwich thin slices of clay between several layers of copy paper. Place this on your work tile and set a phone book on top. How firm you want your clay to be is up to you, so this will require some monitoring on your part. A few hours may be enough, or you may need to allow the clay to rest a day or two, replacing the paper each time you see it is saturated through (this will appear as a grease stain). Remember that leaving unbaked clay on painted, varnished, or lacquered surfaces can damage their finish.
Firmer clays are naturally harder to condition and can sometimes be crumbly. Conditioning with a pasta machine should only be done after getting the clay warm and partially conditioned by hand.
Clay is very responsive to the heat of your hands. Some brands of clay will continue to get softer and softer in consistency when being handled.
Always begin working with the lightest colors of clay first whenever possible. Clay is like a magnet. It will pick up anything on your hands or work surface. Baby wipes-regular or alcohol-free-are ideal for cleaning your hands between colors of clay. A word of caution about generic brands of wipes: These can be very fibrous and may contaminate your clay with tiny particles of lint.
Baking
Polymer clay can be cured in ovens, including conventional, toaster, and convection types. Never use a microwave oven! And even though thousands of people have baked their clay in their food ovens for decades without incident, it's best to err on the side of caution and use a dedicated clay oven. If this isn't possible, you can create a "baking chamber" to use in your home oven. This is simply a roasting pan or large lidded pot that you dedicate for clay baking. If the piece is too tall for the lid to fit, tightly wrap a tent of aluminum foil over the baking pan.
Always follow the manufacturer's instructions for baking time and temperature. Preheat the oven and always use an oven thermometer to check for accuracy. I can't stress this enough.
(Continues...)
Excerpted from The Complete Book of Polymer Clay by LISA PAVELKA Copyright © 2010 by Lisa Pavelka. Excerpted by permission.
All rights reserved. No part of this excerpt may be reproduced or reprinted without permission in writing from the publisher.
Excerpts are provided by Dial-A-Book Inc. solely for the personal use of visitors to this web site.
Table of Contents
Introduction
What You Need: An overview with photos of the clay and clay related materials.
What to Know
Millefiori
Skinner Blending
Transfers
Mokumé Gané
Metallic Effects
Faux
Molding/Forming
Stamping
Surface Treatments
Constructions
Gallery: More than 50 finished pieces. One-two additional projects with step-by-step instructions will appear at the end of each chapter, including:
Tips and Troubleshooting
Glossary of Terms
Resources
Index