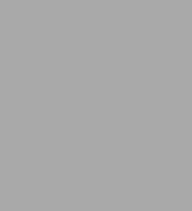
Systematische Beurteilung technischer Schadensfälle
564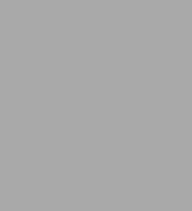
Systematische Beurteilung technischer Schadensfälle
564eBook6. Auflage (6. Auflage)
Available on Compatible NOOK devices, the free NOOK App and in My Digital Library.
Related collections and offers
Overview
Das vorliegende Buch ist aus einem gleichnamigen Seminar hervorgegangen. Dieses Seminar hat in mehr als 30 Jahren gezeigt, dass Schadensfälle in überwiegender Zahl auf Zuwiderhandeln gegen bekannte Regeln der Technik beruhen. Daher liegt der Fokus dieses Nachschlagewerks auf der systematischen Gliederung des Fachgebietes und der anschaulichen Erklärung der Schadensmechanismen in der Theorie sowie durch die praktische Darstellung realer Schadensfälle. Diese Kenntnisse sind für Konstrukteure und Produktionstechniker ebenso von Interesse wie für Qualitäts- und Schadensanalytiker.
Product Details
ISBN-13: | 9783527683215 |
---|---|
Publisher: | Wiley |
Publication date: | 02/12/2014 |
Sold by: | JOHN WILEY & SONS |
Format: | eBook |
Pages: | 564 |
File size: | 51 MB |
Note: | This product may take a few minutes to download. |
Language: | German |
About the Author
Günter Lange war Professor für Angewandte Werkstoffkunde an der Technischen Universität Braunschweig. Der Schwerpunkt seiner Forschungs- und Lehrtätigkeit lag auf der Untersuchung von Verformung und Bruch metallischer Werkstoffe und der Anwendung dieser Erkenntnisse in der Schadensanalyse. Er bekleidete zahlreiche Ämter in Fachgesellschaften, unter anderem als Vorstandsmitglied
DGM und als Ehrenvorsitzender des VDI-Fachausschusses Schadensanalyse. Für sein gesellschaftliches und wissenschaftliches
Engagement erhielt Günter Lange 1991 das Bundesverdienstkreuz und 2000 die Karl-Wellinger-Ehrenmedaille des VDI.
Michael Pohl ist Inhaber des Lehrstuhls Werkstoffprüfung der Ruhr-Universität Bochum. Seit mehr als dreißig Jahren erforscht er die Mechanismen des Materialversagens in Stählen und trug so maßgeblich zu einer Systematisierung auf dem Gebiet der Schadensanalyse bei. Als lang jähriger Leiter des Metallographieausschusses der Deutschen Gesellschaft für Materialkunde (DGM) und Tagungsorganisator erhielt er im Jahre 2000 den Roland-Mitsche-Preis und für seine Arbeit als Vorsitzender des Fachauschusses Schadensanalyse im Jahre 2006 die Karl-Wellinger-Ehrenmedaille und 2011 die Ehrenmitgliedschaft des VDI.
Table of Contents
Vorwort zur 6. Auflage xiiiVorwort zur 1. Auflage xv
1 Vorgehensweise bei der Bearbeitung eines Schadensfalles 1
1.1 Aufgaben und Ziele der Schadensanalyse 1
1.2 Vorgehensweise 2
1.3 Schadensaufnahme und Beweissicherung 2
1.4 Informationen über den Schadensfall 3
1.5 Durchführung 4
2 Einteilung, Ursachen und Kennzeichen der Brüche 13
2.1 Brucharten 13
2.2 Definitionen der Brucharten 14
2.3 Bruchursachen 18
2.4 Allgemeine Kennzeichen für Bruch- und Beanspruchungsart 20
3 Werkstoffuntersuchungen 25
3.1 Mechanische Werkstoffprüfung 26
3.2 Metallografische Werkstoffuntersuchungen 35
3.3 Chemische Werkstoffuntersuchungen 39
3.4 Zerstörungsfreie Werkstoffuntersuchungen 39
3.5 Bewertung und Messungen von Eigenspannungen 44
4 Elektronenmikroskopie bei der Schadensanalyse 49
4.1 Systematik elektronenmikroskopischer Schadensanalyse 49
4.2 Grundlagen der Elektronenmikroskopie 50
4.3 Geräte 52
4.3.1 Transmissionselektronenmikroskop (TEM) 52
4.3.2 Rasterelektronenmikroskop (REM) und Mikrosonde (MS) 54
4.3.3 Elektronenstrahlmikroanalyse (ESMA) 56
4.3.3.1 Wellenlängendispersive Spektrometer 56
4.3.3.2 Energiedispersive Spektrometer (EDS) 58
4.3.3.3 Anwendung der ESMA 58
4.3.4 Rückstreu-Elektronenbeugung (Electron Backscattered Diffraction, EBSD) 59
4.3.5 Weitere Analyseverfahren 62
4.3.6 Abbildungsverfahren 65
4.3.6.1 Sekundärelektronenabbildung 65
4.3.6.2 Rückstreuelektronenabbildung 66
4.4 Präparations- und Untersuchungsverfahren 68
4.4.1 Oberflächenuntersuchungen 69
4.4.2 Untersuchungen des Werkstoffinneren 69
4.4.3 Fraktografische Untersuchungen 72
4.4.4 Focussed Ion Beam (FIB) 73
4.4.5 Untersuchung von Pulvern 73
4.4.6 TEM-Untersuchungen 75
4.4.7 Quantitative Bildanalyse 76
4.4.8 Quantitative Elektronenstrahlmikroanalyse 76
4.5 Zusammenfassung 77
5 Mikroskopische und makroskopische Erscheinungsformen des duktilen Gewaltbruches (Gleitbruch) 79
5.1 Definition und Erscheinungsformen 79
5.2 Trichter-Kegel-Bruch 81
5.3 Fräserförmiger Bruch 90
5.4 Scherbruch 91
5.5 Ausziehen zur Spitze 96
5.6 Einfluss von Werkstoff und Beanspruchung auf die Wabenform 97
6 Makroskopische und mikroskopische Erscheinungsformen des Spaltbruches 103
6.1 Einleitung 103
6.2 Phasen des Bruchvorganges 103
6.3 Kennzeichnung von Spaltbrüchen 104
6.4 Makroskopische Bruchmerkmale 104
6.5 Mikroskopische Bruchmerkmale 106
6.5.1 Transkristalliner Spaltbruch 107
6.5.2 Interkristalliner Spaltbruch 113
6.5.3 Mischbrüche 115
6.5.4 Spaltbrüche in martensitischen Werkstoffzuständen 115
6.5.5 Verwechselungsmöglichkeiten 116
6.5.6 „Quasi-Spaltbruch“ 118
6.6 Bauteilversagen durch Spaltbruch 120
7 Makroskopisches und mikroskopisches Erscheinungsbild des Schwingbruches 127
7.1 Definition und generelle Bemerkungen 127
7.2 Makroskopisches Erscheinungsbild 128
7.2.1 Anriss 128
7.2.2 Schwingungsriss 136
7.2.3 Restbruch 137
7.2.4 Charakteristische Bruchflächen 138
7.3 Abhilfemaßnahmen 139
7.4 Mikroskopische Mechanismen und Topografien 140
7.5 Beispiele 159
7.5.1 Steifigkeitssprünge 159
7.5.2 Oberflächenfehler 176
7.5.3 Schwingbrüche an ausgewählten Bauteilen 191
7.5 Anhang 219
7.5.3 Analyse von 250 Schadensfällen an Luftfahrzeugen 219
8 Thermisch induzierte Brüche 221
8.1 Anforderungen an Werkstoffe für den Einsatz bei erhöhter Betriebstemperatur 221
8.2 Warmfestigkeit 221
8.2.1 Brandschäden 223
8.3 Kaltrisse 225
8.3.1 Aufhärtungsrisse 225
8.3.2 Unterplattierungsrisse 226
8.4 Heißrisse 228
8.4.1 Erstarrungsrisse 228
8.4.2 Aufschmelzungsrisse 228
8.4.3 Heißrissverursachende Phasen 231
8.5 Zeitstandfestigkeit 231
8.5.1 Gefügeveränderungen 233
8.5.2 Zeitstandporen 237
8.5.3 Zeitstandbrüche 241
8.5.4 Restlebensdauer 243
8.6 Härterisse 245
8.7 Thermische Ermüdung 245
8.8 Zusammenfassung 248
9 Korrosionsschäden an metallischen Werkstoffen ohne mechanische Belastung 251
9.1 Einleitung 251
9.2 Korrosion 252
9.3 Korrosionserscheinungsformen ohne mechanische Belastung 261
9.3.1 Gleichmäßige Flächenkorrosion 261
9.3.2 Muldenkorrosion 262
9.3.3 Lochkorrosion 262
9.3.4 Spaltkorrosion 265
9.3.5 Kontaktkorrosion (galvanische Korrosion) 266
9.3.6 Taupunktkorrosion 267
9.3.7 Stillstandskorrosion 267
9.3.8 Sauerstoffkorrosion 268
9.3.9 Selektive Korrosion 268
9.3.9.1 Interkristalline Korrosion 268
9.3.9.2 Spongiose 271
9.3.9.3 Entzinkung 272
9.3.10 Mikrobiologische Korrosion 272
9.4 Untersuchungen zum Korrosionsverhalten 272
10 Korrosionsschäden an metallischen Werkstoffen bei überlagerter mechanischer Beanspruchung 277
10.1 Einleitung 277
10.2 Rissbildende Korrosionsarten 277
10.2.1 Anodische Spannungsrisskorrosion 278
10.2.1.1 Schadensbeispiele 281
10.2.2 Schwingungsrisskorrosion 287
10.2.2.1 Schadensbeispiel 288
10.2.3 Dehnungsinduzierte Spannungsrisskorrosion 289
10.2.3.1 Schadensbeispiel 290
10.2.4 Lotrissigkeit 291
10.2.4.1 Schadensbeispiel 291
10.2.5 Kathodische Spannungsrisskorrosion 292
10.2.5.1 Schadensbeispiele 294
10.3 Erosionskorrosion 296
10.3.1 Strömungsbeeinflusste Korrosion 296
10.3.2 Flüssigkeitsaufprallerosion, Tropfenschlag 298
10.4 Kavitationskorrosion 299
10.4.1 Schadensbeispiele 300
10.5 Reibkorrosion 302
10.6 Schlussbemerkung 304
11 Schäden durch Wasserstoff 307
11.1 Vorbemerkung 307
11.2 Atomarer und molekularer Wasserstoff 307
11.2.1 Thermodynamische Gleichgewichte 307
11.2.2 Kinetik 310
11.2.3 Effusion 311
11.3 Schadensarten 313
11.3.1 Verzögerter Bruch und Wasserstoffinduzierte Spannungsrisskorrosion (H-ind. SCC) 314
11.3.2 Fischaugen und Flocken 318
11.3.3 Beizblasen und HICs 323
11.3.4 Methanbildung 323
11.4 Beispiele 323
11.5 Verwechslungsmöglichkeiten 337
11.6 Wasserstoffempfindlichkeit verschiedener metallischer Werkstoffe 339
11.6 Anhang (Verwendete Größen und Gleichungen) 343
12 Schäden durch Hochtemperaturkorrosion 345
12.1 Allgemeine Bemerkungen 345
12.2 Thermodynamik und Kinetik 346
12.2.1 Gleichgewichte 346
12.2.2 Wachstum und Struktur 349
12.3 HTK in heißen Gasen 350
12.3.1 Oxidation 350
12.3.1.1 Zunderbeständigkeit durch Legieren 354
12.3.1.2 Innere Oxidation 356
12.3.2 Aufkohlung (Innere Karbidbildung) 357
12.3.2.1 Aufkohlende Gase 358
12.3.2.2 Selbstaufkohlung 360
12.3.3 Wasserstoffangriff 362
12.3.3.1 Druckwasserstoffangriff oberhalb 200 °C auf Stahl 362
12.3.3.2 Wasserstoffkrankheit bei Kupfer 363
12.3.4 Schwefelung 363
12.3.4.1 Schwefelaktivität von Gasen 363
12.3.4.2 Stabilisierung der oxidischen Schutzschicht 364
12.4 HTK unter Ablagerungen 365
12.4.1 HTK an Überhitzerberohrungen steinkohlengefeuerter Dampferzeuger 366
12.4.2 HTK an Gasturbinenschaufeln 369
12.5 HTK in Metallschmelzen 371
13 Werkstoffschäden durch Verschleiß 375
13.1 Grundlagen zum Verschleißverhalten von Werkstoffen 375
13.2 Tribosystem 376
13.3 Verschleißarten und Verschleißmechanismen 380
13.3.1 Verschleiß durch Abrasion 381
13.3.2 Verschleiß durch Adhäsion 384
13.3.3 Verschleiß durch tribochemische Reaktion 385
13.3.4 Verschleiß durch Oberflächenermüdung 394
13.4 Verschleißschutzschichten 395
13.4.1 Verfahren zur Untersuchung von Verschleißschutzschichten 398
13.4.2 Galvanisch abgeschiedene Chromschichten 399
13.4.3 Außenstromlos abgeschiedene Nickelschichten 399
13.5 Zusammenfassung 401
14 Schäden an Schweißnähten 405
14.1 Einleitung 405
14.2 Werkstoffbeeinflussung durch den Schweißprozess 406
14.3 Rissbereiche in Schweißkonstruktionen 406
14.3.1 Schwachstellen 407
14.3.2 Risslagen 409
14.4 Rissarten in Schweißverbindungen 410
14.4.1 Fertigungsrisse 410
14.4.1.1 Heißrisse 411
14.4.1.2 Kaltrisse 417
14.4.1.3 Lamellenrisse 424
14.4.1.4 Relaxationsrisse 430
14.4.2 Betriebsrisse 436
14.4.2.1 Betriebsrisse infolge Überbeanspruchung 436
14.4.2.2 Betriebsrisse – ausgehend von Schweißfehlern 441
14.5 Schlussbetrachtung 442
15 Bruchmechanik in der Schadensanalyse 447
15.1 Einleitung 447
15.2 Stabile, instabile und unterkritische Rissausbreitung 447
15.3 Spannungsintensitätsfaktor 449
15.3.1 Definition 449
15.3.2 Die wirksamen Spannungen 450
15.3.3 Oberflächenrisse 451
15.3.4 Spannungsintensitätsfaktoren für beliebige Belastungen 452
15.4 Anwendungsbereich der linear-elastischen Bruchmechanik (LEBM) 453
15.5 Zusammenhang zwischen kritischer Risslänge und kritischer Spannung 453
15.6 Unterkritisches Risswachstum bei wechselnder Belastung 454
15.7 Unterkritisches Risswachstum bei konstanter Belastung und aggressiver Umgebung 456
15.8 Lebensdauerberechnung 456
15.9 Korrelation Bruchlinienabstand – mittlere Rissgeschwindigkeit 457
15.10 Korrelation Bruchlinienabstand –∆K 458
15.11 Versagen durch plastische Instabilität 459
15.12 Die Zwei-Kriterien-Methode 461
15.13 Anwendungsbeispiel: Behälter unter Innendruck 462
15.14 Bruchmechanische Schadensbewertung 465
16 Schäden an Druckbehältern 469
16.1 Zusammenfassung 469
16.2 Problemstellung 469
16.3 Risikobewertung mittels Bruchmechanik 473
16.4 Fallstudien 476
16.4.1 Unfall mit Sauerstoffflasche 476
16.4.2 Unfall mit Acetylenflasche 480
16.4.3 Katastrophe mit Flüssiggastankwagen 482
16.5 Folgerungen 485
17 Schadensuntersuchungen und Problemlösungen mit Oberflächenanalytik 487
17.1 Einleitung 487
17.2 Oberflächenempfindliche Untersuchungsmethoden 487
17.3 Auger-Elektronen-Spektroskopie (AES) 489
17.3.1 Physikalische Grundlagen 489
17.3.2 Scanning Auger Microscope (SAM) 491
17.4 Röntgen-Fotoelektronen-Spektroskopie (XPS, ESCA) 492
17.4.1 Physikalische Grundlagen 492
17.4.2 ESCA-Anlage 493
17.5 Anwendungsbeispiele 494
17.5.1 Kadmium-Versprödung der Bolzen aus der Triebwerksaufhängung eines Großraumflugzeugs 494
17.5.2 Beschädigter Drucksensor 496
17.5.3 Oberflächenkontamination bei einer Hochfrequenz-Empfangsspule 500
17.5.4 Haftung von diamantartigen Kohlenstoffschichten auf Implantaten 502
17.5.5 Oberflächenanalyse einer Hüftgelenkprothese 505
17.6 Zusammenfassung 507
18 Schwingungsrisse bei der dynamischen Prüfung von Seilbahnkomponenten 511
18.1 Einleitung 511
18.2 Seilbahnsysteme 511
18.3 Fahrzeugkomponenten bei Umlaufseilbahnen 513
18.4 Betriebsbelastungen 514
18.5 Europäische Normen für Seilbahnfahrzeuge 515
18.6 Beispiele aus der Praxis 517
18.6.1 Beispiele zu Spannungskonzentrationen 518
18.6.1.1 Kuppelbare Seilklemme 518
18.6.1.2 Gehängestange 520
18.6.1.3 6-Personen-Kabinenstruktur 520
18.6.1.4 3-Personen-Sesselfahrzeug 521
18.6.2 Beispiele zu Schweißeigenspannungen und Steifigkeitsänderungen 522
18.6.2.1 6-Personen-Kabinenfahrzeug 522
18.6.2.2 4-Personen-Kabinenfahrzeug 524
18.6.2.3 Gehängerahmen eines Seilbahnfahrzeuges 525
18.6.3 Versagensbeispiele infolge Reibkorrosion 526
18.6.3.1 Allgemeines 526
18.6.3.2 4-Personen-Sesselfahrzeug 527
18.6.3.3 8-Personen-Seilbahnkabine 529
18.6.4 Versagensbeispiel infolge Montagespannungen 531
18.6.5 Versagensbeispiel infolge Spannungsrisskorrosion 534
Stichwortverzeichnis 539