The presentation begins with a review of chemical and physical fundamentals and conversion fundamentals, and proceeds to coal gasification and gas upgrading. Subsequent chapters examine liquids and clean solids produced from coal, liquids obtained from oil shale and tar sands, biomass conversion, and environmental, economic, and related aspects of synthetic fuel use.
The text is directed toward beginning graduate students and advanced undergraduates in chemical and mechanical engineering, but should also appeal to students from other disciplines, including environmental, mining, petroleum, and industrial engineering, as well as chemistry. It also serves as a reference and guide for professionals.
The presentation begins with a review of chemical and physical fundamentals and conversion fundamentals, and proceeds to coal gasification and gas upgrading. Subsequent chapters examine liquids and clean solids produced from coal, liquids obtained from oil shale and tar sands, biomass conversion, and environmental, economic, and related aspects of synthetic fuel use.
The text is directed toward beginning graduate students and advanced undergraduates in chemical and mechanical engineering, but should also appeal to students from other disciplines, including environmental, mining, petroleum, and industrial engineering, as well as chemistry. It also serves as a reference and guide for professionals.
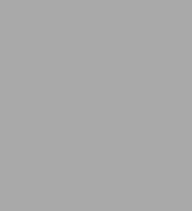
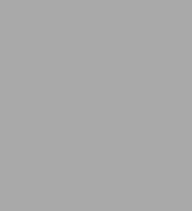
eBook
Available on Compatible NOOK devices, the free NOOK App and in My Digital Library.
Related collections and offers
Overview
The presentation begins with a review of chemical and physical fundamentals and conversion fundamentals, and proceeds to coal gasification and gas upgrading. Subsequent chapters examine liquids and clean solids produced from coal, liquids obtained from oil shale and tar sands, biomass conversion, and environmental, economic, and related aspects of synthetic fuel use.
The text is directed toward beginning graduate students and advanced undergraduates in chemical and mechanical engineering, but should also appeal to students from other disciplines, including environmental, mining, petroleum, and industrial engineering, as well as chemistry. It also serves as a reference and guide for professionals.
Product Details
ISBN-13: | 9780486319339 |
---|---|
Publisher: | Dover Publications |
Publication date: | 04/15/2013 |
Series: | Dover Books on Aeronautical Engineering |
Sold by: | Barnes & Noble |
Format: | eBook |
Pages: | 512 |
File size: | 15 MB |
Note: | This product may take a few minutes to download. |
About the Author
Son of a Gambling Man
Ronald F. Probstein, Ford Professor of Engineering, Emeritus, at the Massachusetts Institute of Technology has had a long career in engineering research and has made significant contributions in many areas from ballistic missile design, to hypersonic flight theory, to the field of synthetic fuels, a subject of obvious importance to everyone. His 1959 book, Hypersonic Flow Theory, co-authored with Wallace D. Hayes, and reprinted by Dover in 2004 as Hypersonic Inviscid Flow, is still the basic book on this subject. Synthetic Fuels, written with R. Edwin Hicks, is certainly one of the most important and timely engineering texts ever reprinted by Dover.
In addition to their own writings, Probstein and Hayes edited the English translation of a major text by two distinguished Russian physicists, Ya. B. Zel'dovich and Yu. P. Raizer, Physics of Shock Waves and High-Temperature Hydrodynamic Phenomena.
However, Dr. Probstein's literary legacy isn't all about hard science. In 2009 he published an evocatively entertaining memoir of his father and their life in Depression-era New York, Honest Sid: Memoir of a Gambling Man. Even though not a Dover book, it is certainly highly recommended.
Critical Acclaim for Physics of Shock Waves and High-Temperature Hydrodynamic Phenomena:
The republication by Dover Publications of this masterwork by Ya. B. Zel'dovich and Yu. P. Raizer will be welcomed by all workers dealing with high-temperature (radiating) flows. This book is a virtual 'bible' for studies of shocks and radiation fronts in high speed aeronautics, astronautics (re-entry), astrophysics, fireballs, shock tubes, and very intense explosions.
Zel'dovich was a physicist of extraordinary breadth of interests. The style of this book is to give heuristic explanations followed by rigorous analysis. It is insightful for both beginning students and researchers in the field. This book is an ABSOLUTE MUST for anyone working on the subjects listed above.
I URGE anyone working in astrophysics and high-temperature flow physics to buy, read, enjoy, and be enlightened by this masterpiece. -- Dimitri Mihalas, co-author of Foundations of Radiation Hydrodynamics
Read an Excerpt
Synthetic Fuels
By Ronald F. Probstein, R. Edwin Hicks
Dover Publications, Inc.
Copyright © 2006 Ronald F. Probstein and R. Edwin HicksAll rights reserved.
ISBN: 978-0-486-31933-9
CHAPTER 1
INTRODUCTION
1.1 SYNTHETIC FUELS AND THEIR MANUFACTURE
Gaseous or liquid synthetic fuels are obtained by converting a carbonaceous material to another form. In the United States the most abundant naturally occurring materials suitable for this purpose are coal and oil shale. Tar sands are also suitable, and large deposits are located in Canada. The conversion of these raw materials is carried out to produce synthetic fuels to replace depleted, unavailable, or costly supplies of natural fuels. However, the conversion may also be undertaken to remove sulfur or nitrogen that would otherwise be burned, giving rise to undesirable air pollutants. Another reason for conversion is to increase the calorific value of the original raw fuel by removing unwanted constituents such as ash, and thereby to produce a fuel which is cheaper to transport and handle.
Biomass can also be converted to synthetic fuels and the fermentation of grain to produce alcohol is a well known example. In the United States, grain is an expensive product which is generally thought to be more useful for its food value. Wood is an abundant and accessible source of bio-energy but it is not known whether its use to produce synthetic fuels is economical. The procedures for the gasification of cellulosic materials have much in common with the conversion of coal to gas. We consider the conversion of biomass in the book, but primary emphasis is placed on the manufacture of synthetic fuels from coal, oil shale, and tar sands. Most of the conversion principles to be discussed are, however, applicable to the spectrum of carbonaceous or cellulosic materials which occur naturally, are grown, or are waste.
For our purposes we regard the manufacture of synthetic fuels as a process of hydrogenation, since common fuels such as gasoline and natural gas have a higher hydrogen content than the raw materials considered. The source of the hydrogen which is added is water. The mass ratio of carbon to hydrogen for a variety of fuels is shown in Table 1.1. Generally, the more hydrogen that is added to the raw material, the lower is the boiling point of the synthesized product. Also, the more hydrogen that must be added, or alternatively the more carbon which must be removed, the lower is the overall conversion efficiency in the manufacture of the synthetic fuel.
The organic material in both tar sands and in high-grade oil shale has a carbon-tohydrogen mass ratio of about 8, which is close to that of crude oil and about half that of coal. For this reason, processing oil shale and tar sands to produce liquid fuels is considerably simpler than making liquid fuels from coal. However, the mineral content of rich tar sands in the form of sand or sandstone is about 85 mass percent, and the mineral content of high-grade oil shale, which is a fine-grained sedimentary rock, is about the same. Therefore, very large volumes of solids must be handled to recover relatively small quantities of organic matter from oil shale and tar sands. On the other hand, the mineral content of coal in the United States averages about 10 percent.
In any conversion to produce a fuel of lower carbon-to-hydrogen ratio, the hydrogenation of the raw fossil fuel may be direct, indirect, or by pyrolysis, either alone or in combination. Direct hydrogenation involves exposing the raw material to hydrogen at high pressure. Indirect hydrogenation involves reacting the raw material with steam, with the hydrogen generated within the system. In pyrolysis the carbon content is reduced by heating the raw hydrocarbon until it thermally decomposes to yield solid carbon, together with gases and liquids having higher fractions of hydrogen than the original material.
To obtain fuels that will bum cleanly, sulfur and nitrogen compounds must be removed from the gaseous, liquid, and solid products. As a result of the hydrogenation process, the sulfur and nitrogen originally present in the raw fuel are reduced to hydrogen sulfide and ammonia, respectively. Hydrogen sulfide and ammonia are present in the gas made from coal or released during the pyrolysis of oil shale and tar sands, and are also present in the gas generated in the hydrotreating of pyrolysis oils and synthetic crudes.
Synthetic fuels include low-, medium-, and high-calorific value gas; liquid fuels such as fuel oil, diesel oil, gasoline; and clean solid fuels. Consistent with SI units, we use the shorthand terms low-, medium-, and high-CV gas, where CV denotes calorific value, in place of the terms low-, medium-, and high-Btu gas which are appropriate to British units. Low-CV gas, often called producer or power gas, has a calorific value of about 3.5 to 10 million joules per cubic meter (MJ/[m.sup.3]). This gas is an ideal turbine fuel whose greatest utility will probably be in a gas-steam combined power cycle for the generation of electricity at the location where it is produced. Medium-CV gas is loosely defined as having a calorific value of about 10-20 MJ/[m.sup.3], although the upper limit is somewhat arbitrary, with existing gasifiers yielding some-what lower values. This gas is also termed power gas or sometimes industrial gas, as well as synthesis gas. It may be used as a fuel gas, as a source of hydrogen for the direct liquefaction of coal to liquid fuels, or for the synthesis of methanol and other liquid fuels. Medium-CV gas may also be used for the production of high-CV gas, which has a calorific value in the range of about 35 to 38 MJ/[m.sup.3], and is normally composed of more than 90 percent methane. Because of its high calorific value, this gas is a substitute for natural gas and is suitable for economic pipeline transport. For these reasons it is referred to as substitute natural gas (SNG) or pipeline gas. Lom and Williams1 have pointed out that originally SNG stood for synthetic natural gas, but it was observed that what was natural could not very well be synthetic.
In Figure 1.1 are shown the principal methods by which the synthetic gases can be produced from coal. Gas can be manufactured by indirect hydrogenation by reacting steam with coal either in the presence of air or oxygen. When air is used, the product gas will be diluted with nitrogen and its calorific value will be low in comparison with the gas manufactured using oxygen. The dilution of the product gas with nitrogen can be avoided by supplying the heat needed for the gasification from a hot material that has been heated with air, in a separate furnace, or in the gasifier itself before gasification. In all of the cases, the gas must be cleaned prior to using it as a fuel. This purification step involves the removal of the hydrogen sulfide, ammonia, and carbon dioxide, which are products of the gasification. Medium-CV gas, consisting mainly of carbon monoxide and hydrogen, can be further upgraded by altering the carbon monoxide-to-hydrogen ratio catalytically and then, in another catalytic step, converting the resulting synthesis gas mixture to methane. A high-CV gas can be produced by direct hydrogenation, termed hydrogasification, in which hydrogen is contacted with the coal. A procedure still under development, which allows the direct production of methane, is catalytic gasification. In this method the catalyst accelerates the steam gasification of coal at relatively low temperatures and also catalyzes the upgrading and methanation reactions at the same low temperature in the same unit.
Gas can also be produced by pyrolysis, that is, by the distillation of the volatile components. Oil shale or tar sands are generally not thought of as primary raw materials for gas production, although the use of oil shale has been discussed.
Clean synthetic liquid fuels can be produced by several routes, as shown in Figures 1.2 to 1.4. For example, in indirect liquefaction (Figure 1.2), coal is first gasified and then the liquid fuel is synthesized from the gas. This procedure is not thermally efficient, relating to the fact that the carbon bonds in the coal must first be broken, as in gasification, and then in a further step some of them must be put back together again. Another procedure, illustrated in Figure 1.3, is pyrolysis, the distillation of the natural oil out of the coal, shale, or tar sands. The oil vapors are condensed, the resulting pyrolysis oil is treated with hydrogen, and the sulfur and nitrogen in it is reduced. This is similar to the procedure used in upgrading crude oil in a refinery to produce a variety of liquid fuels. Pyrolysis may also be carried out in a hydrogen atmosphere, a process termed hydropyrolysis, in order to increase the liquid and gas yield. In direct liquefaction (Figure 1.4) there are two basic procedures, hydroliquefaction and solvent extraction. In hydroliquefaction the coal is mixed with recycled coal oil and, together with hydrogen, fed to a high pressure catalytic reactor where the hydrogenation of the coal takes place. In solvent extraction, also termed "solvent refining," the coal and the hydrogen are dissolved at high pressure in a recycled coal-derived solvent which transfers the hydrogen to the coal. After phase separation, the coal liquid is cleaned and upgraded by refinery procedures to produce liquid fuels. In solvent refining, with a low level of hydrogen transfer, a solid, relatively clean fuel termed "solvent refined coal" is obtained.
In order to compare the size and output of synthetic fuel plants producing different products, a nominal reference standard is desirable and should incorporate both the calorific value of the product and the rate of production. In the United States the nominal accepted calorific values of various synthetic fuel products are shown in Table 1.2. These values are all defined in British units and we have shown their SI equivalents. It should be emphasized that the calorific value per barrel of liquid fuel is a nominal one that holds approximately for synthetic crudes, fuel oils, and some transportation fuels.
Although there are not now "standard-size" plants, nor are there likely to be in the future, there has nevertheless grown up in the U.S. literature certain nominal plant sizes which have come to be accepted as "standard." These sizes are shown in Table 1.3 together with their SI equivalents. The nominal standard sizes shown were not necessarily accepted because they are economically optimum. Indeed, the accepted nominal liquid fuel plant size has changed from 100 thousand barrels per day, a value which was adopted because it was believed that the synthetic fuel products would be upgraded in existing refineries which no longer would have a source of natural petroleum crude.
For the purposes of this book, where needed we have chosen to adopt nominal standard plant sizes that are convenient in SI units and not at great variance with the commonly accepted sizes in British units. We are justified in this to the extent that the sizes in Table 1.3 are arbitrary and to the extent that they do not necessarily represent the actual sizes of plants to be built. Our nominal standards are shown in Table 1.4, where it can be seen that the calorific value outputs of the plants are more nearly comparable than for the sizes in Table 1.3. Moreover, the "ten million" unit size may ease the transition to SI units for those accustomed to "barrels per day" and "standard cubic feet per day." In any case, we emphasize the nominal character of the selection, the main purpose of which is to provide a basis for comparison amongst the different types of plants.
1.2 HISTORY
Contrary to widespread opinion, the manufacture of synthetic fuels is neither new nor has it been limited in the past to small-scale development. This is perhaps most true of the production of gas from coal. As early as 1792, Murdoch, a Scottish engineer, distilled coal in an iron retort and lighted his home with the coal gas produced. By the early part of the nineteenth century, gas manufactured by the distillation of coal was introduced for street lighting, first in London in 1812, following which its use for this purpose spread rapidly throughout the major cities of the world. The early coal gas contained noxious and poisonous impurities, but techniques were soon developed for cleaning and purification. Gas distribution networks were rapidly built up in most large-and medium-size cities, particularly in the industrialized European countries, along with gasworks for the manufacture of the coal gas. By the last quarter of the nineteenth century, coal gas came into widespread use for home lighting. Toward the end of the nineteenth century its use as a source of heat for domestic and industrial applications took on even greater importance.
Coal gas as distributed contained about 50 percent hydrogen, from 20 to 30 percent methane, with carbon monoxide the remaining principal constituent. Its calorific value was about 19 MJ/[m.sup.3] and this value served as the benchmark for the "town gas" industry. A solid coke byproduct of limited utility was produced in coal processing by "carbonization." However, in the latter half of the nineteenth century, complete gasification of coke was achieved commercially by means of a cyclic gas generator in which the coke was alternately blasted with air to provide heat and steam to generate "blue water gas," a name given to the gas because it burned with a blue flame. The discovery of blue gas is attributed to Fontana in 1780, who proposed making it by passing steam over incandescent carbon. The blue gas was composed of about 50 percent hydrogen and 40 percent carbon monoxide, with the remainder about equal parts carbon dioxide and nitrogen. It had a calorific value of about 11 MJ/[m.sup.3], and to increase this value to that of town gas it was enriched with cracked oil gas.
At about the same time as the cyclic gas generator was commercialized, the complete gasification of coal was carried out commercially in continuous fixed bed "gas producers," which manufactured a low-CV gas with a calorific value of 5–6.5 MJ/[m.sup.3] by reaction of air and steam with coal. By the turn of the century, gas producers had come into widespread use for on-site generation of gas for industrial heating.
In the first half of the twentieth century the availability of natural gas with a calorific value of 37 MJ/[m.sup.3] began to displace the use of manufactured gas. In the United States following the end of World War II, with discoveries of large quantities of natural gas in Texas and because of the growth of the natural gas pipeline transportation network, the town gas industry virtually disappeared. The same was also true in Europe where low-cost natural gas became available while the price of coal rose.
Since the Arab oil embargo of 1973, in coal-producing countries such as the United States, attention has once again turned to the alternatives for manufacturing gas from coal. Development work is now directed toward improving gasifier technology and unit output for the large-scale production of industrial gas, gas to be used in the manufacture of SNG, and synthesis gas to be used for the manufacture of liquid fuels and chemicals. Development of processes to produce SNG in single units is also being carried forward. A number of commercial-scale coal conversion projects, each with an output of 3.5 million cubic meters per day or greater, are also underway, including ones for the production of medium-CV industrial fuel gas as well as SNG.
The history of coal liquefaction is considerably more recent than that of coal gasification. Direct coal liquefaction can be traced back to the work of Bergius in Germany, recorded in his publications from 1912 to 1926. In his studies and developments, he produced coal liquids by reacting pulverized coal or coal-oil slurries with hydrogen at high pressures and temperatures. In 1931 he received the Nobel Prize in Chemistry for his work. The development of commercial-size coal hydrogenation units for the production of motor fuels was begun in Germany in 1926. By 1939, production was estimated for the year to be 1.1 million tons, which is roughly equivalent to a production of 4 million liters per day of gasoline. In 1935, a commercial coal hydrogenation plant was started up in England and smaller-scale experimental plants were put in operation elsewhere throughout the world. During World War II, production of liquid fuels, mostly aviation gasoline, from coal and coal tars by direct liquefaction, was greatly expanded in Germany. Over a one year period it is estimated to have peaked at an average production of 4.2 million tons annually, which is equivalent to a rate of about 16 million liters of gasoline per day. This output came from 12 plants, the largest of which produced some 2.7 million liters per day of gasoline equivalent.
(Continues...)
Excerpted from Synthetic Fuels by Ronald F. Probstein, R. Edwin Hicks. Copyright © 2006 Ronald F. Probstein and R. Edwin Hicks. Excerpted by permission of Dover Publications, Inc..
All rights reserved. No part of this excerpt may be reproduced or reprinted without permission in writing from the publisher.
Excerpts are provided by Dial-A-Book Inc. solely for the personal use of visitors to this web site.
Table of Contents
1. Introduction2. Chemical and Physical Fundamentals
3. Conversion Fundamentals
4. Gas from Coal
5. Gas Upgrading
6. Liquids and Clean Solids from Coal
7. Liquids from Oil Shale and Tar Sands
8. Biomass Conversion
9. Environmental Aspects
10. Economics and Perspective
Appendixes
Index