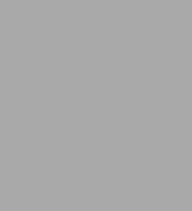
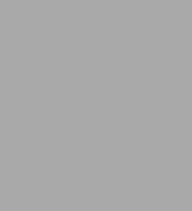
eBook
Related collections and offers
Overview
Product Details
ISBN-13: | 9780486157740 |
---|---|
Publisher: | Dover Publications |
Publication date: | 05/25/2012 |
Sold by: | Barnes & Noble |
Format: | eBook |
Pages: | 183 |
File size: | 27 MB |
Note: | This product may take a few minutes to download. |
About the Author
Furniture maker and architect Gustav Stickley (1858-1942) was a leading spokesman for the American Craftsman movement, a design trend descended directly from the British Arts and Crafts movement.
Read an Excerpt
STICKLEY CRAFTSMAN FURNITURE CATALOGS
By Gustav Stickley
Dover Publications, Inc.
Copyright © 1979 Dover Publications, Inc.All rights reserved.
ISBN: 978-0-486-15774-0
CHAPTER 1
CRAFTSMAN FURNITURE
ANYBODY who knows Craftsman furniture has no difficulty in perceiving that the principles upon which it is based are honesty and simplicity. This is quite true, for when I first began to make it I did so because I felt that the badly-constructed, over-ornate, meaningless furniture that was turned out in such quantities by the factories was not only bad in itself, but that its presence in the homes of the people was an influence that led directly away from the sound qualities which make an honest man and a good citizen. It seemed to me that we were getting to be a thoughtless, extravagant people, fond of show and careless of real value, and that one way to counteract this national tendency was to bring about, if possible, a different standard of what was desirable in our homes.
I suppose it was because I began as a farmer boy and got my training for the work I was ultimately to do by doing as a matter of course the thing which had to be done, that I grew up with the habit of going at things in a natural way. The farmer boy is not given to theorizing about his work, but he soon learns to accept without question the fact that certain things have to be done and that the best way is for him to get right at it and get them done as soon as possible.
Therefore, when the idea came to me that the thing for me to do was to make better and simpler furniture, I naturally went at it in the most direct way. Having been for many years a furniture manufacturer, I was, of course, familiar with all the traditional styles, and in trying to make the kind of furniture which I thought was needed in our homes, I had no idea of attempting to create a new style, but merely tried to make furniture which would be simple, durable, comfortable and fitted for the place it was to occupy and the work it had to do. It seemed to me that the only way to do this was to cut loose from all tradition and to do away with all needless ornamentation, returning to plain principles of construction and applying them to the making of simple, strong, comfortable furniture, and I firmly believe that Craftsman furniture is the concrete expression of this idea.
Because of the sturdiness and beauty of our American white oak, I chose it as the best wood for the kind of furniture I had in mind, and the "style," such as it was, developed naturally from the character of the wood and the application to it of the most direct principles of construction. The result was that I soon found that there was a quality in my plain furniture which took hold of nearly all thinking people as it had taken hold of me, and that in giving expression to what might have been considered an impractical ideal under present-day conditions, I had hit upon an idea which was destined to have a far greater success than even I had hoped for it.
The first pieces of Craftsman furniture were completed in 1898 and then for two years more I worked steadily over the development of forms, the adjustment of proportions and the search for a finish which would protect the wood and mellow it in color without sacrificing its natural woody quality. Then in 1900 I introduced Craftsman furniture to the public at large by exhibiting it at the Furniture Exposition in Grand Rapids, Michigan. The result showed that I had not been mistaken in supposing that this,—the first original expression of American thought in furniture,—would appeal strongly to the directness and common sense. of the American people. From the time of that first exhibition Craftsman furniture grew rapidly in favor, and after the Pan-American Exposition in 1901 its success was assured.
BEGINNING OF METAL AND LEATHER WORK
BUT this success carried with it the obligation to go on and develop still further the basic principles which had found expression in the furniture. The first need was for metal trim which would harmonize in character with the furniture, as none of the glittering, fragile metal then in vogue was possible in connection with its straight severe lines and plain surfaces. So I opened a metal work department in The Craftsman Workshops, and there we made plain, strong handles, pulls, hinges and escutcheons of iron, copper and brass, so designed and made that each article fulfilled as simply and directly as possible the purpose for which it was intended, and so finished that the natural quality of each metal was shown frankly as was the quality of the wood against which it was placed. Also,—for Craftsman furniture is very exacting in its requirements,—leather was needed for cushions, table tops and seats for chairs and settles, and sturdy fabrics interesting in color, weave and texture, had to be found for the same purpose. This necessitated a further expansion to take in the special treatment of leathers so that they harmonize with the Craftsman idea in maintaining all their leathery quality unimpaired, while giving long service under hard wear; and also to include a fabric department, that the textiles used in connection with the furniture would be sure to have the qualities that would harmonize with it.
GROWTH OF OUR DECORATIVE SCHEME
THE fact that the furniture so imperatively demanded the right kind of metal work and fabrics naturally opened the way to a more extended use of these departments in the making of things intended for general furnishings. While Craftsman furniture is very friendly in its nature and fits in comfortably with any good simple scheme of interior decoration and furnishing, it yet holds out a strong temptation to develop an entire scheme of furnishing along the same lines. So we began in the metal shop to make electric lighting fixtures, fireplace fittings, trays, candlesticks and all manner of useful household articles, designed on the same general principles as the furniture and therefore just as essentially a part of one general scheme of furnishing. The fabrics in their turn were made into curtains, portières, pillows, scarfs, centerpieces and the like, and decorated with needlework and applique in strong simple designs and colorings which belonged to the oaken furniture as naturally as the leaves on a tree belong to the trunk. So, step by step, we grew naturally into the designing and arranging, first of rooms, then of entire schemes of interior decoration, and lastly the planning and building of the whole house.
THE INDIVIDUALITY OF CRAFTSMAN FURNITURE
AS I have already said, Craftsman furniture is built for all manner of uses and its construction is so thorough that it will last for the lifetime of the oak of which it is made, which means the lifetime of several generations of men. Being designed upon the most natural lines and made in the most natural way, there is little room for change in the style, and that the style itself has made good its appeal to the American people is best proven by the fact that, during the twelve years it has been upon the market, it has remained unchanged, except for such modifications and improvements as evidence a healthy growth along normal lines of development. It is impossible to get far away from the structural lines which declare the purpose and use of the piece, and the proportions that best serve that purpose and use are the proportions which it should have. As to the matter of decoration, it will grow of itself in time, for true decoration is always the natural expression of the thought and desire of the people who own and use the things made, combined with the desire of the craftsman to express his own idea of beauty. I am so sure of this that I have been content to leave the furniture absolutely plain until the form of decoration which inevitably belongs to it shall come.
HOW WE FINISH CRAFTSMAN FURNITURE
OF COURSE, a great deal depends upon the finish which is given the oak of which it is made. This is a case where art must come to the aid of nature, because to leave the wood in the purely natural state would be to leave it exposed to all manner of soil and stain from wear. Also, the natural color of new oak is rather uninteresting; it needs age and exposure to give it the depth and mellowness which we associate with this wood. So, while our whole object is to keep the wood looking entirely natural in its possession of all the qualities which belong to oak, this can be done only by the most careful treatment. Some time ago it was discovered that the fumes of ammonia would, within a very short time, darken white oak naturally, giving it the appearance which ordinarily would result from age and use. Therefore, as soon as a piece of Craftsman furniture is made, it is first moistened all over to open the pores, and then put into an air-tight compartment, on the floor of which are placed basins of very strong (26%) ammonia. The time usually demanded for this fuming is forty-eight hours, but that is varied according to the wood and the depth of color required. After the fuming the wood is carefully sand papered by hand until all the loose fiber is rubbed away and every trace of roughness removed. Then comes the final finish. For years I worked and experimented to find something that would leave the furniture entirely free from the hard glaze given by the use of shellac or varnish and yet would completely protect it, not only from soil or stain but also from the atmospheric changes which cause it to shrink or swell. It was a difficult problem,—that of finding a method of finishing which would preserve all the woody quality of the oak without sacrificing the protection needed to make it "stand" under widely varying climatic conditions,—and it is only recently that I hit upon a solution which satisfies me. I found that all that is required to develop the best qualities of oak is to so ripen and mellow the wood that the full value of its natural color is brought out, as well as the individual beauty of texture and grain. The final finish we give it adds very little color, as our aim is rather to develop than to alter the natural tone of the wood, which always appears as an undertone below the surface tint. By the use of this finish we give the oak three different tones, all of which belong essentially to the wood. One is a light soft brown that is not unlike the hue of the frost-bitten oak leaf; another is the rich nut-brown tone which time gives to very old oak; and the third is a delicate gray that gives to the brown of the wood a silvery sheen such as might be produced by the action of the sun and wind. For the last rubbing we use the "Craftsman Wood Luster," which is not a varnish or a polish, but which gives a soft satiny luster to the surface of the wood. When that surface is worn or soiled with use it may be fully restored—if the soil does not penetrate beyond the surface—by wiping it off with a piece of cheesecloth dampened with the Wood Luster and then rubbing it dry with a fresh cloth.
THE CRAFTSMAN LEATHERS
IN THE selection of materials for covering our chairs and settles, we give the preference to the Craftsman leathers, which are especially prepared to harmonize with the design and finish of our furniture. These leathers are of three kinds—Hard and Soft Leather and Sheepskin, all finished by a process of our own, and each satisfactory in its place. The Hard and Soft Leathers are produced by the use of different methods in tanning cattle hides, by which one is made much like sole leather in stiffness and durability, and is given a smooth, hard surface, while the other is rendered soft and pliable, with a surface possessing texture enough to give an excellent effect when dull-finished. Hard Leather is used for table tops and for chair and settle seats where the leather is stretched over the seat rails and nailed on. Soft Leather is used for slip seats in chairs and for loose seat cushions in settles, where the size of the cushion requires a large hide. Sheepskin is the softest and most flexible of all our leathers, and seems to me to be best adapted to covering pillows and loose seat and back cushions for chairs, where the skins can be used without piecing.
My constant experimenting with finishes has included the treatment of leather as well as wood, and my recent success with wood finishes suggested a way to improve the leather as well. The result is that I have not only found a method by which all these leathers are made waterproof, but also I have been able to do away with what so far has been the weak point of Sheepskin, for I am now dressing the skins in such a way that they are entirely free from any tendency to check or craze. Naturally, their wearing quality is greatly improved, and in addition to this I have been able to obtain a beauty of color and a softness of surface that, so far as I know, has never been equaled. No artificial graining is used, but the natural grain of each kind of leather is left to show its full value.
CUSHIONS AND PILLOWS
ALL our loose spring-seat cushions for chairs and settles are made so that the shape will be retained even under the hardest wear. These cushions are made over stout wood frames which are carefully fitted to each piece, and have exactly the same appearance as the ordinary loose cushions, except that the frame upon which the cushion is built slips just inside the frame of the chair, so that the seat, although removable, is always in place. Its construction not only makes it more comfortable than the ordinary cushion, but keeps it from ever getting out of shape or wearing into hollows like the ordinary stuffed cushions. Where the backs of chairs require loose cushions, they are made with equal care and filled with Java floss.
LEATHER-COVERED TABLES
WITH some of our more massive tables, we have been able to obtain an added interest by covering the top with hard leather, finished in a color that blends with and emphasizes the tone of the wood. Naturally, we use only a single large hide in covering a table top, so that the surface is perfect, and the great spread of leather, showing the most charming play of varied tones over the glossy surface,—which yet retains all the leathery quality as an undertone,—gives an effect of rich and sober excellence to the piece that makes it easily the center of attraction among the furnishings of a living room or a large and well-appointed library. We quote in the catalogue the prices of both wood-top and leather-top; but for those that are best left all in wood, we quote no price in leather.
OUR HARD LEATHER CHAIR SEAT
ALL our leather-seated chairs, which have not either slip seats or spring-seat cushions, are made with firm, flat seats of hard leather, stretched tightly over the rails. This seat has unlimited durability. The foundation is made of very thick, firm canvas, stretched tightly over the seat-rails and nailed underneath. Over this heavy webbing is woven as closely as the width of the strands will permit, and just enough padding is laid over the top to give a smooth surface above the webbing—but not enough to interfere with the perfect flatness of the seat. Then the hard leather, stiff and firm as sole leather, is stretched over the rails, wrapped around and nailed on the inside. The square-headed nails are used only at the corners, where they fasten down the leather that is cut around the posts.
BENT ROCKERS
ALL the rockers now used on Craftsman rocking chairs are cut straight with the grain of the wood and then bent with steam pressure by bending machines. This precaution makes the rocker as strong as any other part of the chair and entirely does away with the danger of breaking that exists when the rocker is cut on a curve that partly crosses the grain.
HOW TO IDENTIFY CRAFTSMAN FURNITURE
FROM its first success in 1900, the popularity achieved by Craftsman furniture was the signal to an army of imitators who saw in it what they considered a novelty that would prove to be a notable moneymaker. These manufacturers at once began to turn out large quantities of furniture which was designed in what seemed to them the same style. But failing to comprehend my reasons for giving to Craftsman furniture forms that were plain and almost primitive, they naturally seized upon this primitiveness as a fad which might be profitable and exaggerated it into intentional crudeness. This imitation has grown instead of decreased with the passing of time, and while in one sense it is the best evidence of the popularity and stability of the Craftsman style, in another it creates confusion which at times is annoying. Restrained by law from the use of my registered name, "Craftsman," these manufacturers get as near to it as they can and variously style their products "Mission," "Hand-Craft," "Arts and Crafts," "Crafts-Style," "Roycroft," and "Quaint." To add to the confusion, some of the most persistent of these imitators bear the same name as myself and what is called "Stickley furniture" is frequently, through misrepresentation on the part of salesmen and others, sold as "Craftsman furniture or just the same thing."
(Continues...)
Excerpted from STICKLEY CRAFTSMAN FURNITURE CATALOGS by Gustav Stickley. Copyright © 1979 Dover Publications, Inc.. Excerpted by permission of Dover Publications, Inc..
All rights reserved. No part of this excerpt may be reproduced or reprinted without permission in writing from the publisher.
Excerpts are provided by Dial-A-Book Inc. solely for the personal use of visitors to this web site.
Table of Contents
Contents
Title Page,Copyright Page,
INTRODUCTION TO THE DOVER EDITION,
Catalogue of CRAFTSMAN FURNITURE,
CRAFTSMAN FURNITURE,
CRAFTSMAN METAL WORK,
CRAFTSMAN FABRICS & NEEDLEWORK,
CRAFTSMAN WILLOW FURNITURE,
CRAFTSMAN RUGS,