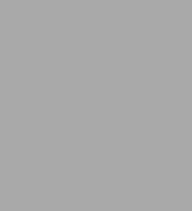
Selecting the Right Manufacturing Improvement Tools: What Tool? When?
416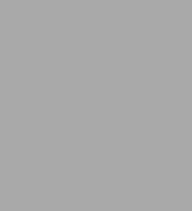
Selecting the Right Manufacturing Improvement Tools: What Tool? When?
416eBook
Available on Compatible NOOK devices, the free NOOK App and in My Digital Library.
Related collections and offers
Overview
But his book goes beyond a simple comparison of improvement tools to show how these tools can be implemented and supported. Instead, it offers a broader strategic explanation of how they relate to one another, and their relative strengths and weaknesses in the larger context of the entire enterprise. It demonstrates how to use these tools in an integrated way such that they are not just be viewed as another “program of the month? or management fad. Selecting the Right Manufacturing Improvement Tools guides the use of these individual management tools within the need for aligning the organization, developing leadership, and managing change, all for creating an environment where these tools will be more successfully applied.
· Provides an excellent review of the most popular improvement tools and strategies - Lean Manufacturing, Kaizen, including 5S, Kanban, Quick Changeover, and Standardization, Total Productive Maintenance, Six Sigma, Supply Chain Management, Reliability Centered Maintenance, Predictive Maintenance (or Condition Monitoring), and Root Cause Analysis.
· Illustrates the use of each tool with case studies, using a fictitious company called "Beta International," which continues its journey to business excellence from author's previous book, Making Common Sense Common Practice
· Describes the foundational elements necessary for any tool to work - leadership, organizational alignment and discipline, teamwork, performance measurement, change management, and the role of innovation.
· Concludes with a recommended hierarchy for the use of the various tools, and provides enough information so that individual circumstances and issues can be related to these improvement tools, making better decisions and having greater business success.
Product Details
ISBN-13: | 9780080468198 |
---|---|
Publisher: | Elsevier Science |
Publication date: | 04/01/2011 |
Sold by: | Barnes & Noble |
Format: | eBook |
Pages: | 416 |
File size: | 2 MB |
About the Author
Read an Excerpt
SELECTING THE RIGHT MANUFACTURING IMPROVEMENT TOOLS
What Tool? When?By RON MOORE
Butterworth-Heinemann
Copyright © 2007 Elsevier Ltd.All right reserved.
ISBN: 978-0-08-046819-8
Chapter One
IntroductionProductivity isn't everything, but in the long run it is almost everything. Paul Krugman, Economist
The Scene
Beta International, a large manufacturing conglomerate, has made substantial progress in its operations and business performance. A few years ago, Bob Neurath, CEO, set forth a 10-point strategic plan for process improvement that focused on getting back to basics. After all, he reasoned, if we aren't tenacious about getting the basics right, how can we expect to get anything else right? Driven from the top, this focus has yielded substantial gains for the company. Asset performance has improved, unit costs are decreasing, safety performance continues to improve, and market share is increasing in many markets, holding steady in others, and only declining in a few markets that are on strategic watch. Profits have moderately increased in most business units and holding steady in almost all others.
But, performance is simply not good enough. Return on capital is only about average in most business units. Intense pricing pressures from foreign competition, particularly Asian manufacturers, are continuing to drive down prices and hold down margins. If downward pricing pressures are stemming from Asia, Bob muses, then there is no doubt that companies like Wal-Mart, with their guaranteed lowest-price strategy, will only further intensify those pressures. The low margins resulting from these pressures limit Beta's ability to invest in research and development (R&D) for new product and process development, new capital projects that flow from this R&D, as well as strategic acquisitions better aligned to the company's long-term strategy and business objectives. As a result, future market development and the growth that goes with it are likely to be hampered. In summary, the good news is that Beta has returned from the brink of disaster to become at least a mediocre company, maybe even above average in some business units. The bad news is that Beta is still not much better than a mediocre company. Perhaps more importantly, many seem to be satisfied, even pleased, with this. Bob Neurath is not. Having taken a step back from the abyss it faced a few years ago, Bob is now ready to move Beta forward more aggressively, creating a much more profitable future for the business. Trying to be all things in all markets only dilutes management focus, thus leading to mediocrity. Bob's expectation, like many corporate leaders today, is that Beta should be first or second in all of its markets or have a clear, measurable path for achieving that position. The company must now move from survival mode to growth mode.
Beyond the "back to basics" focus in all practices for all operations, several of Beta's divisions have tried various improvement tools with varying degrees of success. One division was convinced that Six Sigma would provide substantial gains and achieved substantial improvement in some of its operations, but not others. Another division considered total productive maintenance (TPM) more appropriate and likewise achieved substantial gains in some operations, but not others. Another adopted the Toyota Production System—what has come to be known as Lean Manufacturing—or so they thought. In that division, Bob's characterization is not that they are lean and mean, but rather anorexic and angry. Although improvements were achieved, overall results were less than desired, and on further review, it appears many of the initial results have been lost and they may have left out key strategic and philosophical elements of the system.
Beta's experience has been similar to that of other companies. Various tools or methods are touted as a means for a major step forward but never seem to quite deliver the expected results. For example, Bob Williamson, an industry expert in TPM, estimates that some 60% of TPM programs fail after three years of effort; Jeffrey Liker, an industry expert in Lean Manufacturing, estimates that less than 1% of U.S. companies are truly effectively applying lean principles. Neil Bloom, an industry expert in reliability-centered maintenance (RCM) estimates that over 60% of all RCM programs initiated are never successfully implemented, with many of the rest only done in a superficial way. RCM is an excellent tool for identifying and minimizing functional failures, is also on occasion called the "resource consuming monster." Given the limited resources in most companies through downsizing, RCM does not typically get the support it needs to do the analysis or the results end up being stored in binders on a shelf. Root cause analysis has various approaches, including the "5 Whys" supported by Toyota and progressively more comprehensive approaches, but it can also be very resource-intensive, limiting management's ability to successfully apply it.
The Response
Bob's response to this lack of consistency and "constancy of purpose" (Deming) in applying these tools, beyond a certain amount of chagrin, was to form a senior-level steering team to review each tool and make a judgment about its efficacy and efficiency. Some questions being asked were: (1) under what circumstances do we apply each strategy or tool? (2) what are each tool's advantages and disadvantages? (3) are they compatible and/or supportive? (4) do some require other related tools to be used in conjunction for maximum results? and (5) when are they incompatible? These fundamental questions need answers in order to develop a strategy for their application that could align the organization toward a common set of goals within all of Beta's various operating units.
Bob also demanded an annual market review to ensure proper alignment of the manufacturing plants' strategy to the marketing and product mix strategy (and vice versa). The review needed to identify the major steps needed for assuring growth in all markets. He agreed with Michael Treacy's view in Double Digit Growth that growing market share required Beta to do most, if not all, of the following seemingly straightforward activities:
1. Keep the customers that you already have by creating incentives for them to stay or obstacles to their departure.
2. Take business from your competition by making your products more attractive.
3. Go to where the growth is by anticipating those growth areas.
4. Enter adjacent markets by adapting your products to those markets.
5. Invest in developing new product lines, markets, and customers.
These principles need to be applied at Beta, along with the models for rationalizing and optimizing products, customers, and markets outlined by Christopher and Moore to better manage those products, customers, and markets and, particularly, to align these to the manufacturing capability. Both recommend a routine analysis of customers and products and their contribution to the business. The model used by Christopher suggests dividing customers and products into A, B, and C categories. For example, the A list is the 20% of customers who provide 80% of profits and/or volume or the 20% of products that provide 80% of profits and/or volume. The A list must be sustained and built over time. The B and C lists require either development or elimination. Both Christopher and Moore offer models for optimizing customers and products.
Bob will continue to use the model shown in Figure 1-1 to help align the marketing and manufacturing strategies.
The marketing department will manage product and customer mix and complexity within the product range. They will work with manufacturing to understand the implications of their decisions on the manufacturing function, particularly as it relates to quality, cost, and delivery. This communication will be a two-way street with business decisions based on what is best for the business overall and not on a single given function. The plants work to improve quality, cost, and delivery through improved reliability and stability as well as reduced variability and waste. This should increase capacity and gross profits and allow the pursuit of additional market share without having to make additional capital investment.
Bob also agrees with Bossidy and Charan's contention that: (1) the world is awash in capital creating overinvestment and excess capacity; (2) China and India are attracting much of that capital with their large markets and cheap labor; and (3) when combined with the Wal-Mart/Home Depot business model for driving down prices, costs must follow downward. Most importantly, Beta must compete in that environment. Beta must become more productive, reduce its waste and system/supply chain cycle times, and use its inherent advantages. It would also require Beta to take stronger positions in the Chinese and Indian markets, both in terms of products and customers, as well as potential manufacturing capability to address those markets and perhaps others worldwide. Clearly, this will all be challenging.
Bossidy and Charan's model for doing this is shown in Figure 1-2. They suggest that we must fully understand our business's external realities: Are we in a growing or declining market? What is happening to prices in those markets? What is happening to our customer base? Are we in the middle of a major structural shift? They also suggest that we understand our internal activities relative to our external realities. Is our strategy aligned with market realities? Are our operations efficient enough to address those? Are we as executives engaging our people in supporting our improvement? Is our organizational structure aligned to meeting our objectives? And, are we meeting our financial targets in light of all this, routinely iterating and improving our performance relative to the external realities and internal activities?
Bossidy and Charan offer a number of suggestions and case studies in addressing these issues, something that Beta must adopt to be more effective in managing its business.
The Tools
An initial review of the tools and strategies being used in various Beta operating units revealed that the following were applied to some significant degree, sometimes in conjunction, but at other times independently from one another. That is, different plants or functions were applying one tool or the other without coordinating their application. In any event, the most common tools and strategies being applied were found to be:
* Lean Manufacturing
* Kaizen
* Total Productive Maintenance
* Six Sigma
* Supply Chain Management
* Reliability-Centered Maintenance
* Predictive Maintenance
* Root Cause Analysis
Some, such as Lean Manufacturing and Kaizen, included the use of tools of Total Quality Management/Assurance (TQM/A), 5S, quick changeover, and other techniques. Others, like Six Sigma, included the use of statistical process control techniques and design of experiment (DOE). A summary of the steering team's initial findings regarding each of these is provided next.
(Continues...)
Excerpted from SELECTING THE RIGHT MANUFACTURING IMPROVEMENT TOOLS by RON MOORE Copyright © 2007 by Elsevier Ltd. . Excerpted by permission of Butterworth-Heinemann. All rights reserved. No part of this excerpt may be reproduced or reprinted without permission in writing from the publisher.
Excerpts are provided by Dial-A-Book Inc. solely for the personal use of visitors to this web site.
Table of Contents
1. Introduction2. Aligning the Organization
3. Innovation
4. Leadership and Teamwork
5. Managing Change
6. Business Level FMEA
7. Lean Manufacturing
8. Kaizen
9. Total Productive Maintenance (TPM)
10. Six Sigma
11. Supply Chain Management
12. Reliability Centered Maintenance (RCM)
13. Predictive Maintenance/Condition Monitoring
14. Root Cause Analysis
15. Closing; Appendices
What People are Saying About This
The only comprehensive book that deals with all important classes of materials and processes