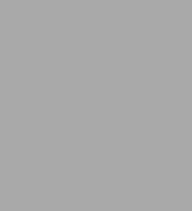
Saving the Pyramids: Twenty First Century Engineering and Egypt's Ancient Monuments
176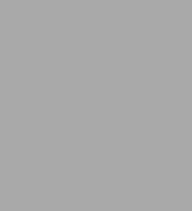
Saving the Pyramids: Twenty First Century Engineering and Egypt's Ancient Monuments
176eBook
Available on Compatible NOOK devices, the free NOOK App and in My Digital Library.
Related collections and offers
Overview
Having worked on projects around the world, strengthening and restoring historically significant structures from Windsor Castle to the parliament buildings in Canada, Peter James brings insight to the structural engineering of ancient Egypt. After fourteen years working on the historic buildings and temples of Egypt, and most recently the world’s oldest pyramid, he now presents some of the more common theories surrounding the ‘collapsing’ pyramid – along with new and innovative projections on the construction of the pyramids and the restoration of some of Cairo’s most monumental structures from the brink of ruin. The decoding of historic construction from a builder’s perspective is examined and explained – at times against many existing theories – and the book provides a new outlook on long-held assumptions, to embrace modern theories in a bid to preserve the past.
Product Details
ISBN-13: | 9781786832528 |
---|---|
Publisher: | University of Wales Press |
Publication date: | 04/12/2018 |
Sold by: | Barnes & Noble |
Format: | eBook |
Pages: | 176 |
File size: | 40 MB |
Note: | This product may take a few minutes to download. |
About the Author
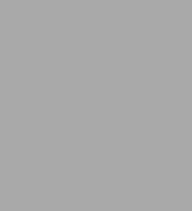
Read an Excerpt
CHAPTER 1
TOOLS OF THE TRADE
When my company was formed in 1985, it was to take exploit patents acquired from a West German engineer. Originally called Cavity Lock Systems Ltd, it had been manufacturing and producing stainless steel cavity wall ties used to overcome the endemic problem in the United Kingdom of corrosion in the mild steel ones.
Wall ties were used from the early nineteenth century to connect single-brick walls together to form a double external wall to prevent moisture passing into the interior of the structure. However, because of inadequate knowledge at that time of corrosion of metals, and particularly of the effect of the black ash mortar used throughout the United Kingdom on bare or galvanized metals, the ties started to corrode, eventually causing the outer skin of the cavity wall to become structurally unstable. The ties could expand to up to seven times their size, forcing the exterior wall to crack and lift, in some cases up to 100 mm, on a traditional semi-detached house. The tell-tale horizontal cracking at every fifth course in the exterior brickwork walls was a sure sign of this failure. Finding a remedy was always going to be difficult. Should the whole tie be removed, or merely bent back into the cavity to protect the external wall from further damage, or would it have to be replaced with a new stainless steel tie?
It was because of the many practical problems of retrofitting replacement wall ties into old structures that I set about looking for a better, more professional solution than the current mechanical expanding stainless steel sleeves or resin injection methods, which caused numerous problems with weak or friable substrates. In my view, the whole tie should be removed and replaced with a new one fitted into both internal and external wall skins.
During my explorations of the industry I came across a Belgian sales engineer looking for a United Kingdom partner for a German inventor, one with experience in using a fabric-socked anchor to solve problems of fixings in the hollow-pot clay blocks used extensively on the Continent. Many of the external walls of West German buildings were constructed in this way, and he had developed some promising ideas using a system that was ideally suited to the problems encountered in repairing or upgrading by adding a new outer wall cladding. Working together, we were able to provide a fabric-socked solution to many of the problems in restoration associated with structural defects, both in hollow-pot and in solid structures.
It was this simple concept that set us off, and we proceeded to develop and fine-tune the idea into a new and more complete way of strengthening structures. After several years of working with these ideas, I decided to acquire the original basic patents and develop the system to encompass a greater range of products and the structures that could be reinforced. It was soon after buying the patents that I decided to create a strong brand name using the current name of the product called Cintec, an acronym for consolidated injection technology.
The company has grown since then with offices in Canada, America, Australia, India and Egypt. It has won many awards and citations for its achievements over the years, in particular the Queen's Award for Innovation in 2002 for strengthening masonry and stone arch bridges. In 2014, I received the Chartered Institute of Builders Award for the outstanding international project for the year for the work on restoring the ceiling of the burial chamber in the Step Pyramid. This monument is an iconic structure dating from 2700 BC, and it is the earliest high-rise stone building in the world.
Whilst the device we developed looks very simple, it is ingenious in concept: not merely a product but the culmination of engineering know-how and the skills with which we can design a complete system to match the requirements of strengthening individual structures.
DESIGN CONSIDERATIONS
The best way to describe the use of the Cintec anchor is to consider how you would place a reinforcement member into an existing building. Imagine you wanted to provide a reinforced concrete lintel into an existing building. Forget the problem of opening up an area to accommodate the lintel and all the associated support work needed, but merely consider making a wooden box the overall size of the lintel, having calculated the amount of steel reinforcing you require, and place this into the box in the correct position. You then somehow pour concrete into the box until it is full to the top.
Think of our system as a lintel, but instead of the wooden box we have a much smaller fabric tubular sock to replace the wooden box, and accordingly a hole to accommodate the sock is drilled, usually with diamond drilling techniques, into the substrate. Although a large opening is needed when we use a wooden box, we do not have to create a large opening needing struts and props.
Having calculated the main reinforcing bar for the application we are able to provide a complete product that, once we have created the hole, can be made to fit exactly.
The entire assembly is placed in the drilled hole and then a suitable non-shrink grout is pumped from a pressure pot, through injection tubes to the rear of the assembly, filling it from back to front. The grout is placed under pressure and fills the entire assembly. A new development has taken place recently using not only a pressure pot to pump grout into the anchor but also to develop a vacuum at the internal end of the reinforcement. This gives greater control in anchoring the reinforcement, and also a positive feedback to the installer, indicating how the anchor is inflating, which is essential when filling an anchor above the horizontal plane. Once the reinforcement is installed, it remains dormant in the wall until it is required to work structurally.
Whilst the analogy of the lintel mirrors the way the anchor actually works, there are numerous other structural solutions to other, more complex structural problems.
Very often conservationists refer to the problem that the reinforcement is too rigid and demand that the grout must be lime-based in keeping with the original structure. Would one take the risk of having a lime-based lintel over one's head? The material and design must be fit for purpose. The original construction was probably built of local materials and needed to be flexible. Structural anchoring and repairs need to be able to mobilize the forces required to lock the structure together. If the designer needs steel reinforcement, this must be connected to the fabric of the structure with a grout that is strong enough to transmit the load to the base material but is contained within the fabric of the sock and does not migrate to other parts of the structure; otherwise the repair will not be effective.
Consider a motor car that needs a steel engine, although you would not want to sit on steel but would prefer leather or fabric. Bearing in mind the problem of compatibility, the designer can find other ways to reduce the extent of the intervention to a minimum by careful use of the smallest possible size of anchor and choice of the most suitable type.
The engineer/designer first calculates the size and profile of the reinforcing member needed, bearing in mind the type and size of load required. All commercially available sizes and profiles are available, such as solid threading bars and grip bars; also from circular, square and rectangular hollow sections and even rolled steel joists.
Normally, because of its high resistance to corrosion and long life expectancy, we use stainless steel graded from 303 or 304 to marine-quality 316 made to the relevant standard. However, we can use mild steel or special memory steel, and even structural grade plastics. We never use galvanized mild steel, as the coating deteriorates within months of being in contact with cementitious grouts.
In order to secure the reinforcement bar in its final position, metal plates made of the same base material as the anchor are fixed to the ends of the anchor to provide a cone of compression locking the anchor body into its final position.
The length of the anchor can be varied by the use of connectors to join the anchor sections together in the manner of drain rod connections. The longest anchor we have installed so far is in a cathedral in Newcastle, Australia. This technique was used to make and install a solid 32 mm stainless steel bar 32 m in length. Obviously, in extending the length of the anchor the designer must take into consideration the hole diameter to allow for the size of the anchor body connectors and the extra grout feed tubes, which need a greater internal diameter to allow the grout to flow through the entire length of the assembly. It is also necessary to allow for a larger diameter so that the sock can be placed evenly throughout the length of the drilled hole with an even build-up of grout within the assembly.
THE NIKER PROJECT
One of the most exciting new programmes in anchor development has recently completed its design phase after two-year knowledge transfer partnership with Bath University followed by a commission from Niker 7, a new integrated European Union initiative for cooperation between partners from universities and research centres to develop protection with minimum intervention for heritage sites against earthquake damage.
Mechanisms to prevent structural failure, construction types and materials, intervention and assessment techniques will be cross-correlated to develop new methodologies. Traditional materials will be complemented and enhanced by innovative industrial processes, and new high-performance elements will be developed. Advanced numerical studies will allow the parametrization of the results to optimize simple design procedures. In addition, advance monitoring and early-warning techniques for intelligent interventions will be developed.
Earthquake destruction accounts for a substantial part of the global heritage losses caused by natural hazards, as well as very high loss of human life. The post-earthquake survey of damage makes possible scientific understanding of the drawbacks and limitations of new technologies and approaches applied in earlier repair works.
Working in real-application conditions, the project aims to develop and validate complete and diversified innovative technologies and tools for the systematic improvement of their ability to withstand the stress of seismic shifts.
A three-year programme began in January 2010, with the active participation of eighteen universities, research centres, public organizations and companies from twelve countries in Europe and the Mediterranean basin. The coordinator is the Department of Structural and Transportation Engineering of the University of Padua, Italy, and the participants were:
The University of Padua.
The Federal Institute of Materials Research and Testing (Germany).
The Institute of Theoretical and Applied Mechanics (Czech Republic).
The National Technical University of Athens (Greece).
The Politecnico of Milan (Italy).
The University of Minho (Portugal).
The Universitat Politècnica de Catalunya (Spain).
The University of Bath (UK).
The Gazi University (Turkey).
L'Ecole Nationale d'Architecture (Morocco).
Cairo University (Egypt).
The Israel Antiques Authority (Israel).
Bozza Legnami (Italy).
Cintec International (UK).
Interprojekt (Bosnia and Herzegovina).
S & B Industrial Minerals (Greece).
ZRS Ziegert Seiler Ingenieure (Germany).
Monumenta (Portugal).
The first concept of a dissipative method developed for Niker 7 was very expensive and its use could only be considered on a structure that was especially noteworthy and of great historical value. Consequently, the project is still ongoing for Cintec with the aim of using a similar principle but with lower production costs and greater ease of installation in smaller-diameter drilled holes. This would bring it within the range of the vast number of endangered domestic dwellings in seismic regions. The product has been called a dissipative fuse.
THE PARENT MATERIAL
The strength of the parent material (the base material to be strengthened) and the mortar can govern the anchor capacity. Design checks on its capacity can be based on the resistant strength, according to national standards of the construction, to the anchor force. When the parent material or mortar strength is not determinable, the capacity of the material can be worked out by means of local site tests.
In general, this means that the greater the strength of the parent material, the smaller the drilled hole needed. When dealing with weak and friable parent material, it is necessary to increase the size of the drilled hole to spread the load over a greater area – exactly as a large tractor tyre enables movement over soft and marshy terrain. This allows the anchor to be used in a large variety of substrates.
THE DRILL HOLE
Placing the reinforcement correctly is probably the hardest part of the intervention and can cause most problems for the installer. Positioning the anchor assembly is vital for the designer. As the hole is drilled, any variation in the quality and type of the parent material causes a major problem for the drilling technician. If the substrate is too hard it will require a different compound for the cutting head. If it is soft and friable, and collapses when the core section is removed, or if there is a combination of all these factors, that is the worst-case scenario.
The designer calculates the correct diameter to be drilled, which will depend on the bond strength between the grout and the anchor body, and the grout between the sock and the substrate. Where there is a problem in defining the strengths, the recommendation is to undertake pull-out trials to assess the bond strength of the anchor.
When dealing with historic structures, the impact of drilling must be reduced to the minimum. Mostly the techniques we use are based on diamond drilling technology, particularly, dry-diamond drilling cooled by moist air – what we call keyhole surgery. However, we have used every type of drilling technique, from rotary percussion drills to large hydraulically powered equipment and power mining barrels in a great variety of projects.
Another technique that we have recently patented is the ability to create grooves in the drilled hole to increase the grout-sock bond capacity, particularly when using short anchors in high-strength material that requires large pull-out capacity.
THE GROUT
Presstec is the product name for the cementitious grout. It is a factory-produced mix with graded aggregates and other constituents which, when combined with water, produce a pumpable grout that exhibits good strength with no shrinkage and no added undesirable elements or resins. It is made in accordance with German Din standards and is checked in the factory laboratory both during manufacture and at final dispatch, and also periodically by a recognized external testing house.
Presstec can also be varied in its manufacture to match the substrates and other conditions such as fast-setting grouts, a rapid-hardening grout, several sulphate-resisting and lime-enhanced grouts.
THE SOCK
The fabric sleeve is a specially woven polyester-based tubular sock with expansion properties to match the diameter of the drilled hole and substrate. The mesh is designed to contain the aggregates of the mixed grout while still allowing the cement-enriched water (milk) to pass through the sock, both sizing and bonding the grout to the substrate. The sock is manufactured in sizes from 20 mm to 300 mm in diameter and is adjusted to suit each individual application. It can also be made of different materials to produce a more resistant interface needed in special circumstances.
The sock is made to our exact specification. The quality of the thread and hole mesh sizes are made to correspond to the anchor type, diameter and overall length. Every anchor sock is measured and cut on a machine designed to control the amount of sock taken from the roll without subjecting it to longitudinal tension. The result is that the manifested product has the correct length and diameter of sock needed for each anchor size without compromising a parallel expansion of the sock when inflated.
The construction of the anchor assembly can vary considerably to provide the designer with an all-encompassing solution to the design problems. Some parts can be socked and others left uncovered. This is done by locating grout feed tubes in the sections to be grouted whilst areas that are not to be inflated can be left without a socked attachment. Some anchors can have detachable grout tubes that can be removed during installation if required, whilst multi-bar anchors can have the feeding tubes in their core, and these tubes can be removed and withdrawn as the anchor is inflated.
After careful unwrapping of the anchor from the factory delivery tube, the entire assembly is accurately positioned inside the drilled hole, which must be inspected, and any dust or debris removed, prior to the installation of the anchor to ensure that the sock is not snagged on any obstructions.
(Continues…)
Excerpted from "Saving the Pyramids"
by .
Copyright © 2018 Peter James.
Excerpted by permission of University of Wales Press.
All rights reserved. No part of this excerpt may be reproduced or reprinted without permission in writing from the publisher.
Excerpts are provided by Dial-A-Book Inc. solely for the personal use of visitors to this web site.