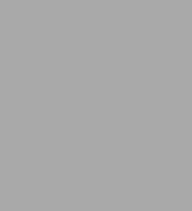
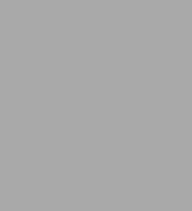
eBook
Available on Compatible NOOK devices, the free NOOK App and in My Digital Library.
Related collections and offers
Overview
The most complete guide of its kind, this is the favored handbook for chemical and process engineers who need a reliable and authoritative solution to their practical on the job problems. Includes all new material on new processing sectors, include biopharmaceuticals. The text is comprehensively revised and updated with new data and formulas. Rules of Thumb for Chemical Engineers solves process design problems quickly, accurately and safely, with hundreds of common sense techniques, shortcuts and calculations.
Key features;
- Rules of Thumb for Chemical Engineers brings together solutions, information and work-arounds that engineers in the process industry need to get their job done.
- New material in the Fifth Edition includes physical properties for proprietary materials, six new chapters, including pharmaceutical, biopharmaceutical sector heuristics, process design with simulation software, and guidelines for hazardous materials and processes.
- Now includes SI units throughout alongside imperial, and now accompanied by online calculation tools New to this edition;
- New chapter on biopharmaceutical systems
- New chapter on closed-loop heat transfer systems
- Extensively rewritten chapters on fluid flow, fractionation, heat exchangers, pumps, compressors, safety, and controls.
- Latest information on packed columns and structured packings
- Excel workbooks, with Visual Basic for Applications function subroutines, that solve many of the problems in the book.
- Fully updated references
- Rules of Thumb for Chemical Engineers brings together solutions, information and work-arounds that engineers in the process industry need to get their job done.
- New material in the Fifth Edition includes physical properties for proprietary materials, six new chapters, including pharmaceutical, biopharmaceutical sector heuristics, process design with simulation software, and guidelines for hazardous materials and processes
- Now includes SI units throughout alongside imperial, and now accompanied by online calculation tools and a searchable Rules of Thumb library
Product Details
ISBN-13: | 9780123877895 |
---|---|
Publisher: | Elsevier Science |
Publication date: | 07/27/2012 |
Sold by: | Barnes & Noble |
Format: | eBook |
Pages: | 456 |
File size: | 18 MB |
Note: | This product may take a few minutes to download. |
About the Author
Read an Excerpt
RULES OF THUMB FOR CHEMICAL ENGINEERS
By Stephen Hall
Butterworth-Heinemann
Copyright © 2012 Elsevier Inc.All right reserved.
ISBN: 978-0-12-387789-5
Chapter One
Fluid Flow
Introduction 2 Data Required 2 General Procedure 3 Recommended Velocity 3 Equivalent Length 6 Shortcut Equation for Pressure Drop Due to Friction 9 Reynolds Number 9 Friction Factor 10 Incompressible Flow 10 Compressible Flow – Isothermal 11 Compressible Flow – Transmission Equations 11 Nomenclature 12 Compressible Flow – Adiabatic 12 Visual Basic Subroutines for Pressure Drop Due to Friction 12 Orifices 19 Control Valves 20 Partially Full Horizontal Pipes 21 Two-Phase Flow 22
Introduction
Chemical engineers who are designing plants and specifying equipment probably face more fluid flow problems than any other. Pressure drop calculations help the engineer size pipes and ducts, determine performance requirements for pumps and fans, and specify control valves and meters. And although the underlying theory is rather simple, its practical application can be confusing due to the empirical nature of important correlations, multiple methods for expressing parameters, many variable inputs, and alternative units of measurement.
This chapter presents formulae and data for sizing piping systems for incompressible and compressible flow:
Friction factor, which is an empirical measure of the resistance to flow by a pipe or duct.
Equivalent Length of a pipe segment, which characterizes bends and fittings as an equivalent length of straight pipe.
Pressure drop due to friction for liquids and gases, both isothermal and adiabatic.
Restriction orifices.
Control valves.
Two-phase flow.
A successful design requires much more analysis than a set of mathematical results. Consider these questions:
What is the required flow range, now and in the future? Plant systems often operate at a range of flows, due to production rate variances, start-up differences, multiple uses of the same system (such as production followed by flushing and cleaning), and future debottlenecking. Ensure that all of the components, such as control valves, account for these variations.
How might the chemical composition and temperature change? Again, different production scenarios may result in wide variances in chemicals in use, and in temperatures. It may be prudent to create material and energy balances for different scenarios, and perform fluid flow calculations on several of these. Gaseous systems are especially sensitive to composition and temperature changes.
Are the piping specifications fixed, or is there flexibility to optimize material selections? Construction materialsmay affect the pressure drop calculations due to differences in their surface roughness and dimensions. Specified wall thicknesses may be adjusted to save money (thinner walls reduce initial capital cost and potentially operating cost since the pressure drop will be lower at otherwise identical flow conditions).
What are the status of flow diagrams, piping and instrumentation diagrams (P&IDs), general arrangement drawings, and elevation drawings? Each of these are needed for a thorough analysis. But preliminary results from fluid flow calculations may be needed to complete the drawing.
An Excel workbook with VBA function routines accompanies this chapter.
Data Required
Design Documents
Block flow diagram (minimum requirement)
Process Flow Diagram (PFD) (highly recommended)
P&ID (desirable)
General Arrangement drawing with major equipment from the P&IDs shown, in scale, in plan and elevation
Piping specifications. Minimum requirements are materials of construction, pressure and temperature limits, and dimensional specifications (e.g., acceptable diameters, wall schedule vs. diameter, long or short elbow radius).
Material and Energy Balance
For each pipe in the analysis, the material composition, flow, and temperature are needed. Various scenarios might be needed.
Physical Properties of the Materials
For liquids, the density, coefficient of thermal expansion, and viscosity at flowing temperature(s) are required.
For gases, provide molecular weight, ratio of specific heats (Cp/Cv), and compressibility factor, Z. Z is needed at high pressures and/or low temperatures. Chapter 27 discusses the determination of Z.
General Procedure
1. List the pipes that are included in the analysis. They are usually the lines shown on the P&IDs.
2. Using the General Arrangement drawings, estimate the length of each line and the number of each type of fitting (elbow, tee, etc.). If the drawings are already completed in CAD, and piping is already drawn, then an actual take-off of the piping should be obtainable from the CAD system. For conceptual or preliminary work, a very quick take-off of each pipe is made by roughly measuring the distance from the origin to the destination of the pipe using x-y-z coordinates, then adding a contingency factor of about 25%. See sidebar "Quickly estimating pipe lengths."
3. If the piping is not yet sized, use velocity to tentatively select pipe diameters.
4. Calculate pressure drop due to friction for selected scenarios. This step is used to determine the optimum size for the pipe during early design work, and to support sizing pumps and control valves during detailed design.
5. Size pumps, fans, and control valves. Iterate through all of the steps as information is developed.
6. Create system curves (see Chapter 5).
7. Update the P&IDs and General Arrangement drawings.
8. Conduct Process Hazards Analyses (PHAs), especially when flammable or toxic chemicals are being processed (see Chapter 20).
Recommended Velocity
Engineers determine pipe sizes by analyzing performance and economic parameters. Over the years, an enormous number of systems have been designed, installed, and operated. Those systems often share similar characteristics since they were built from the same catalog of available equipment, such as pumps and control valves. It's reasonable, then, to begin a new design project using existing system designs as a starting point.
Therefore, a Rule of Thumb is to use tables of suggested velocity for an initial determination of pipe size. The values in the tables have been widely disseminated, and have long since lost their original source. Also, the suggested velocities are often given as ranges. You are cautioned to use the information judiciously and perform your own analysis as your piping system design develops.
Factors to consider regarding velocity:
Low velocity may indicate a larger pipe diameter than is necessary which raises cost.
Low calculated velocity may result in the pipe running partially full in horizontal runs.
Low velocity can lead to laminar flow conditions which may promote fouling and will definitely hinder heat transfer (if applicable).
High velocity may be noisy.
High velocity can cause damage to the pipe due to erosion.
Certain components such as check valves and control valves are designed to operate with a specific flow range; manufacturers of the components recommend minimum lengths of pipe of specified diameter upstream and downstream of their device.
Some more comments by type of service:
Clean single-phase fluids (gas or liquid) tolerate the widest range of velocity. Generally use 1.5 to 4.0 m/s (5 to 12 ft/s) for liquids, or 15 to 40 m/s (50 to 120 ft/s) for gases as a starting point. Use a Net Present Value (NPV) economic analysis to balance the initial capital cost for the piping with energy cost for moving the fluid.
Steam systems are generally designed with higher velocity in the headers than the branch lines. Recommendations are based on comparison with sonic velocity and vary with the system pressure.
Hot fluids, whose vapor pressure is near the system pressure, require careful analysis to ensure the fluids won't flash inside the pipe. This is particularly important on the suction side of pumps, where a Net Positive Suction Head (NPSH) calculation must be performed. See the Pumps chapter for more information on NPSH.
Two-phase systems include solid-liquid, liquid-gaseous, and liquid-liquid. Generally, higher velocity threatens pipe damage due to erosion, especially at bends and components such as valves. Lower velocities may allow the heavy phase to drop out of the flow and collect at low points or coat the pipe surface. The velocities recommended for clean fluids apply, but try hard to avoid excursions. Erosion is proportional to the impact velocity to the power n, where n is usually 2 or 3 depending on the properties of the sediment.
Corrosive fluids, defined as those that chemically attack the pipe if the naturally protective layer is absent (such as with passivated stainless steel), should be treated as if they are erosive. It's important that the flowing fluid does not scour the passivation layer.
Pipe material must be factored into the analysis. Softer materials, such as thermoplastics and copper, are more susceptible to erosion than hard materials, such as austenitic stainless steels.
Compressible Flow of a Gas
The maximum velocity of a gas is equal to the speed of sound at flowing conditions. This is generally at the discharge end of a pipe, but may be at an intermediate location where there is a flow restriction such as a valve or orifice. It's good practice to design for a velocity that is less than 30% of the speed of sound (0.3 Mach). For adiabatic flow, the equation is:
Umax = = √Z γ gc RT/M (1-1)
Z = Compressibility Factor = 1 for an ideal gas
γ = Ratio of Cp/Cv
Oil/Gas Mixtures
A widely used formula is published in API 14E, but this has been challenged by Salama as being overly conservative. It is intended to give the maximum velocity for crude oil/gas mixtures, flowing in two phases (that may contain sand sediment), to avoid excessive erosion.
U = C1/√ρ (1-2)
U = velocity, m/s or ft/s
ρ = gas/liquid mixture density, kg/m3 or lb/ft3
ITLITL1 = coefficient specific to piping material and quality of the fluid. Coefficient for SI units (multiply by 0.82 for US Customary units):
Steel pipe, clean fluid (no sand), continuous service: 122
Steel, clean fluid (no sand), intermittent service: 152
Steel, clean fluid, non-corrosive, continuous service: 180 to 240
Use lower (unspecified) values for sand-containing fluids
API 14E states that the minimum velocity for two-phase flow should be about 3 m/s (10 ft/s).
Check Valves
Check valves are a special case, as reported in detail by Crane. There is a certain minimum velocity needed to keep check valves fully open. If the velocity drops below this, then the valve will partially close. Crane states that:
most of the difficulties encountered with check valves, both lift and swing types, have been found to be due to oversizing which results in noisy operation and premature wear of the moving parts.
The formula for minimum pipe velocity (determined by the nominal pipe size of the check valve, not the flow opening in the valve) is:
Umin = C β2 √[bar.V] (1-3)
ITLITL = coefficient, see Table 1-2.
β = ratio of flow opening in the valve to pipe size
[bar.V] = specific volume of fluid (inverse of density)
Equivalent Length
There are two prevalent methods to characterize the flow resistance of a pipeline with its fittings.
The much easier and more convenient Equivalent Length method computes a pressure drop that is 10% to 20% higher for a typical pipeline compared to the K coefficient method.
(Continues...)
Excerpted from RULES OF THUMB FOR CHEMICAL ENGINEERS by Stephen Hall Copyright © 2012 by Elsevier Inc. . Excerpted by permission of Butterworth-Heinemann. All rights reserved. No part of this excerpt may be reproduced or reprinted without permission in writing from the publisher.
Excerpts are provided by Dial-A-Book Inc. solely for the personal use of visitors to this web site.
Table of Contents
1 Fluid Flow
2 Heat Exchangers
3 Fractionators
4 Absorbers
5 Pumps
6 Compressors
7 Drivers
8 Vessels
9 Boilers
10 Cooling Towers
11 Refrigeration
12 Closed Loop Heat Transfer Systems
13 Biopharmaceutical Systems
14 Vacuum Systems
15 Pneumatic Conveying
16 Blending and Agitation
17 Process Evaluation
18 Reliability
19 Metallurgy
20 Safety
21 Controls
22 Troubleshooting
23 Startup
24 Energy Conservation
25 Process Modeling
26 Approximate Conversion Factors
27 Properties
Appendix
What People are Saying About This
For over 15 years chemical engineers have reached for Rules of Thumb for Chemical Engineers to answer their process engineering problems and to help them get on with the job.