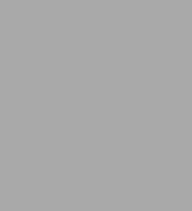
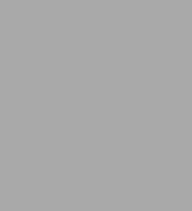
eBook
Available on Compatible NOOK devices, the free NOOK App and in My Digital Library.
Related collections and offers
Overview
Polymers are converted into finished products through a series of steps which include mixing in additives and various types of forming. Following an introduction to polymer science and its importance to various fields, the author describes these processes from a practical, application-oriented perspective. Global suppliers of raw materials, machinery and equipment are also given, making this book an invaluable resource for industry practitioners.
Product Details
ISBN-13: | 9783110656428 |
---|---|
Publisher: | De Gruyter |
Publication date: | 09/21/2020 |
Series: | De Gruyter STEM |
Sold by: | Barnes & Noble |
Format: | eBook |
Pages: | 172 |
File size: | 3 MB |
Age Range: | 18 Years |
About the Author
Table of Contents
Preface V
Chapter 1 Introduction to Polymers 1
1.1 The World of Polymers 1
Bibliography 4
Chapter 2 Basic Chemistry of Polymers 5
2.1 What Are Polymers? 5
2.2 Polymer Categories 6
2.2.1 Polymer Microstructures 7
2.2.2 Lengths of Polymer Chains 8
2.2.3 Polymer Morphology 8
2.2.4 Polymer Behavior - Melting Point 8
2.2.5 Polymer Behavior - Mixing 9
2.3 Polymer Blends 9
2.4 Polymer Composites 10
2.5 Cellular Polymers 10
2.6 Engineered Plastics 11
2.7 Bioplastics 11
2.8 Important Common Polymers 12
2.9 Polymer Degradation 12
2.10 Polymer Waste Disposal 13
Bibliography 13
Chapter 3 Types of Polymers 15
3.1 Common Polymers 15
3.1.1 Polyethytenes 15
3.1.2 Polystyrenes 16
3.1.3 Polypropylenes 17
3.1.4 Polycarbonates 17
3.1.5 Polyvinyl Chloride 19
3.1.6 Polyurethanes 19
3.1.7 Melamine Formaldehyde 20
3.1.8 Acrylonitrile Butadiene Styrene 21
Bibliography 22
Chapter 4 Properties of Polymers 23
4.1 Importance of Properties 23
4.2 Thermal Properties 23
4.2.1 Thermal Diffusivity 23
4.2.2 Linear Coefficient of Thermal Expansion 23
4.2.3 Thermal Degradation 24
4.3 Mechanicaf Properties 24
4.3.1 Tensile Strength 24
4.3.2 Melting Point 24
4.3.3 Young's Modulus of Elasticity 25
4.3.4 Glass Transition Temperature 25
4.3.5 Mixing Behavior 25
4.3.6 Polymer Degradation 26
4.3.7 Density 26
4.3.8 Fatigue Tests 26
4.4 Environmental Effects 26
4.4.1 Water Absorption 27
4.4.2 Chemical Degradation 27
4.5 Viscoelastic Materials 27
4.5.1 Density 27
4.5.2 Firmness 28
4.5.3 Time 28
4.5.4 Temperature 28
4.5.5 Humidity 28
4.6 Electrical Properties 29
4.7 Optical Properties 29
Bibliography 29
Chapter 5 Additives for Polymers 31
5.1 What Are Polymer Additives? 31
5.2 Effects of Additives on Polymers 32
5.2.1 Plasticizing Agents 33
5.2.2 Pigments, Dyes and Masterbatches 33
5.2.3 Stabilizers 34
5.2.4 Lubricants 35
5.2.5 Blowing Agents 35
5.2.6 Catalysts 35
5.3 Influence of Additives During Processing 35
5.3.1 Discoloration and Degradation 36
5.3.2 Improving Molding Processability 36
5.3.3 Improving Durability 37
5.3.4 Use of Lubricants 37
5.4 Functions of Some Additives 38
5.4.1 Antioxidants 38
5.4.2 Antistatic Agents 38
5.4.3 Biodegradable Plasticizers 38
5.4.4 Blowing Agents 39
5.4.5 External Lubricants 39
5.4.6 Fillers/Extenders 39
5.4.7 Flame Retardants 39
5.4.8 Heat Stabilizers 39
5.4.9 Impact Modifiers 40
5.4.10 Light Stabilizers 40
5.4.11 Coloring Agents 40
5.4.12 Reinforcements 40
Bibliography 41
Chapter 6 Useful Data for Processing Polymers 43
6.1 Important Parameters 43
6.2 Coloring of Polymers 43
6.2.1 Introduction 43
6.2.2 Theory of Colors 44
6.2.3 The Color Wheel 44
6.2.4 Primary Colors 45
6.2.5 Secondary Colors 45
6.2.6 Tertiary Colors 45
6.2.7 Warm and Cool Colors 45
6.2.8 Tints, Shades and Tones 46
6.3 Purging Colored Material from Production Machinery 46
6.3.1 Masterbatches 47
6.3.2 Universal Masterbatches 47
6.3.3 Liquid Colorants 47
6.3.3.1 Special Effects Liquid Colorants 48
6.3.4 Precolored Resins 48
6.3.5 Cube Blends 48
6.3.6 Colored Specialty Compounds 48
6.4 Electrical Power Calculations 49
6.5 Compressed Air 50
6.6 Water Requirements 51
6.7 Safety Factors 51
6.8 Quality Control 52
6.8.1 X-R Control Chart 53
6.8.2 P-Chart 53
6.8.3 An SPC System in Operation - An Example 54
6.9 Preventive Maintenance for Machinery and Equipment 55
6.10 Key Factors fora Processing Plant 56
6.11 In-House Laboratory 56
6.12 In-House Workshop 57
6.13 Granutators/Shredders for Recycling Plastic Wastes 57
Bibliography 58
Chapter 7 Lean Processing for Efficiency and Profitability 59
7.1 The Concept of Lean 59
7.1.1 Identifying Value 59
7.1.2 Map the Value Stream 59
7.1.3 Creating Flow 60
7.1.4 Establish a Pull System 60
7.1.5 Constant Improvement 60
7.1.6 Lean Versus Six Sigma 61
7.2 Guidelines to Thinking Lean 61
7.2.1 What Are the Benefits? 61
7.2.2 Continuous Improvement Initiatives 62
7.2.3 Push-Pull System 63
7.2.4 Kanban System 63
Bibliography 63
Chapter 8 Processing Systems for Polymers 65
8.1 Some Common Systems 65
8.2 Common Processing Systems for Thermoforming Resins 65
8.2.1 Extrusion 65
8.2.1.1 Some Types of Commercial Extruders 68
8.2.1.2 Co-Rotating Jntermeshing Extruders 68
8.2.1.3 Counter-Rotating Nonintermeshing Extruders 69
8.2.1.4 Maintenance of Extruders 69
8.2.1.5 Some New Technologies in Extrusion 70
8.2.1.6 Recommended Shutdown Procedures 74
8.2.1.7 Recommended Restart Procedures 74
8.2.2 Injection Molding 75
8.2.2.1 Structural Web Injection Molding 76
8.2.2.2 Benefits of Structural Web Processes 77
8.2.2.3 Structural Foam Injection Molding 78
8.2.2.4 Hand-Operated Injection Molding 79
8.2.3 Blow Molding 80
8.2.4 Compression Molding 82
8.2.4.1 Transfer Molding 84
8.2.4.2 Applications 85
8.2.4.3 Molding Composites by Compression Molding 85
8.2.5 Dip Coating 86
8.2.5.1 Dip Coating Versus Dip Molding 86
8.2.5.2 Dip Coating Procedure 86
8.2.5.3 Hot Dip Coating in a Fluidized Bed 87
8.2.5.4 Hot Dip Coating in Vinyl Plastisol 87
8.2.5.5 Polymer Flock Spraying 87
8.2.6 Vacuum Forming 88
8.2.6.1 The Vacuum Forming Process 88
8.2.7 Direct Coating 90
8.2.8 Indirect Coating 91
8.2.9 Rotational Molding or Rotomolding 92
8.2.9.1 Solar-Powered Rotomolding Units 93
Bibliography 93
Chapter 9 Processing of Liquid Polymer Foaming Systems 95
9.1 Foaming Liquid Polymers 95
9.1.1 Polyvinyl Chloride Plastisol 95
9.1.2 Low-Density Polyethylene Foam 96
9.1.3 Integral Skin Foam 97
9.1.4 Direct Molded Foam 98
Bibliography 98
Chapter 10 Specialty Polymers and Polymeric Composites 99
10.1 What Are Specialty Polymers? 99
10.2 Applications of Specialty Polymers 100
10.3 Graphene - Properties, Processing and Applications in Brief 100
10.4 Graphene-Polymer Composites 100
10.5 Graphene Composites Can Reduce Atmospheric Pollutants 102
10.6 Fluoropolymer Specialty Insulation for Extreme Application Needs 102
10.7 Polyurethane Specialty Polymers 103
10.8 Electrical Conductivity of Conjugated Polymers 104
10.8.1 Flexible Conductive Film 104
10.8.2 Some Latest Automotive Specialty Polymers 105
10.9 Polymer Modified Bitumen 105
10.10 Reinforced Polymers with Coffee Chaff 106
10.11 Specialty Polymer Composites 106
10.12 Specialty Engineered Composites 107
10.13 Specialty Polymer Resins with Rice Hulls 107
10.13.1 Polymeric Composites with Rice Hulls for Injection Molding 108
10.13.2 Recommended Processing Guidelines 109
10.14 Expanded Polystyrene with Graphite 110
10.15 Polymeric Composites with Bamboo Fibers 111
10.16 New Polylactic (PLA) grade for 3D Printing 111
Bibliography 112
Chapter 11 Three Manufacturing Processes for Important Products 113
11.1 Molded Expanded Polystyrene Products 113
11.1.1 Preexpansion and Aging 114
11.1.2 Curing Phase 114
11.1.3 Molding Process 115
11.1.4 Shape Molding 115
11.1.5 Fabrication 116
11.1.6 Some EPS Molded Products 116
11.1.7 Expanded Polystyrene Properties and Key Benefits 116
11.1.7.1 Key Benefits 116
11.1.7.2 Properties 118
11.1.8 EPS in Building Construction 119
11.1.9 Food Packaging 119
11.1.10 Industrial Packaging 119
11.1.11 Safety and Recyclability 120
11.1.12 Extruded Polystyrene Insulation 120
11.1.13 The Extrusion Process for XEPS 120
11.1.14 Insulation Properties of XEPS Boards 121
11.2 Manufacturing Plant for EPS Products for an Entrepreneur 121
11.2.1 The Products 121
11.2.2 Machinery and Equipment 121
11.2.3 Raw Material 123
11.2.4 Production Method 124
11.2.5 Fabrication 125
11.3 Manufacture of Polymeric Composite Resins 125
11.3.1 Technology in Brief 125
11.3.2 Raw Materials 126
11.3.3 Polymers 128
11.3.4 Rice Hulls 128
11.3.5 Additives 129
11.3.6 Processing Machinery and Equipment 129
11.4 Manufacture of PUR Flexible Foam Mattresses 131
11.4.1 The Raw Materials 131
11.4.2 Machinery and Equipment 135
11.4.3 Calculating Density 136
11.4.4 Calculating Indentation Force Deflection 137
11.5 PUR Flexible Foam Manufacturing Methods 137
11.5.1 Manual Operation 137
11.5.2 Molds 138
11.5.3 Cutting and Fabrication 139
11.5.4 Production Method 139
11.6 The Intermittent Process to Make Large Foam Blocks 140
11.6.1 Production Example - Intermittent Process 142
Bibliography 144
Appendix A 145
Appendix B 147
Appendix C 149
Glossary 151
Acknowledgments 155
Index 157