5
1
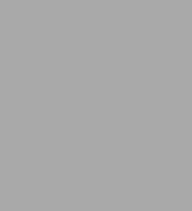
NOW WE KNOW HOW TO REINVENT INDUSTRY To Get Maximum Competitiveness
by Lawrence Rosier
Lawrence Rosier
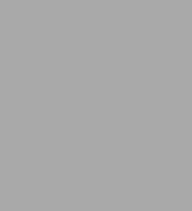
NOW WE KNOW HOW TO REINVENT INDUSTRY To Get Maximum Competitiveness
by Lawrence Rosier
Lawrence Rosier
eBook
$9.99
Available on Compatible NOOK devices, the free NOOK App and in My Digital Library.
WANT A NOOK?
Explore Now
Related collections and offers
LEND ME®
See Details
9.99
In Stock
Overview
Every Industry’s main goal should be to achieve maximum competitiveness. Having the know how and capacity to surpass all competitors is not just an illusion any more. Now we know how to Reinvent Industry to get maximum competitive advantage.
The approach presented in this book seeks to achieve maximum competitiveness through top quality products and by getting the maximum efficiency possible in manufacturing systems while creating a culture of innovation. The approach reinvents the company’s manufacturing and office systems using Enterprise Lean, while creating a Team Managed culture of innovation. This done by following the Reform Models developed by the author and presented in this book.
But the really good news is that the reforms can be largely implemented using your own company’s resources. With the help of a TQM /Lean temporary Training Consultant and a single Management Consultant to guide the implementation for the first six months, when the company can be begin saving $millions. The outcome is vibrant company who’s productivity cannot be matched by competitors.
The biggest competitive news in recent years is Toyota’s winning the competitive struggle against the big three Ford, GM and Chrysler. Toyota used “Total Quality Management (TQM)” to improve its automobiles and “Enterprise Lean” to improve its systems throughout its company to gain competitive advantage. In spite of evidence to the contrary most American CEO’s still believe that Lean is used only to improve the efficiency of hourly workers. The result for most American companies has been competitive stagnation and slow growth compounded by the recession. But now we have a breakthrough we now know how to manage the use of the Japanese tools to achieve maximum competitiveness.
The author recommends that the company’s products be designed for the customer’s needs and meets the highest quality. Then use TQM and Enterprise Lean to fix the company’s systems to get maximum efficiency while developing a culture of innovation. The final step is to replace the bureaucratic organization currently used in most companies with a Team Management organization. The breakthrough is in the step by step approach used in the author’s Reform Models.
Here is how the General Reform Model works.
Phase 1. Following the Toyota method “TQM” and “Enterprise Lean” are implemented throughout the company by training all employees in the use of the tools. There are two levels of training the high level training using Lean is for Management teams to study and improve systems which cross departmental lines as well as inter company operations such as material delivery systems and document flow systems. Other Lean Teams target the functions of the company where office workers and hourly shop floor employees work. The Teams meet once a week using TQM to get the highest quality product and the Lean tool Value Stream Mapping to fix their systems. The outcome is a high quality product and maximum improvement in efficiency for all of the company’s manufacturing systems while empowering employees to innovate in their jobs.
Phase 2. When the first phase is nearly completed the second phase can begin by bringing in Budget Analysts and Industrial Engineers to analyze the Lean study data and determine the cost savings for the current method and the improved method. The result is to right-size the staffing required to do a function and to develop a bottoms-up budget for the function. The outcome is to get the highest efficiency possible while maintaining the effectiveness of the function. Staffing reductions should be close to 20%.
Phase 3. After the Lean Teams have worked together as a team for a period of six months we can begin the last phase of converting the entire organization from a bureaucratic organization to Team Managed organization. The high level Lean Teams form Group Steering Teams to manage several related grouped functions. At the same time the self-managed Functional Team leaders assume the responsibility for their functions. The reform process is a smooth operation with the outcome being the reinvention of the company leading to the highest possible competitiveness.
Other Reform Models target specific industry problem areas. The Consolidation Reform Model focuses on consolidating duplicated service functions and disparate organizations. And the Central IT Cloud Systems Reform Model implements a new IT facility based on a modern database architecture creating an open flexible Relational Database Management system.
The approach presented in this book seeks to achieve maximum competitiveness through top quality products and by getting the maximum efficiency possible in manufacturing systems while creating a culture of innovation. The approach reinvents the company’s manufacturing and office systems using Enterprise Lean, while creating a Team Managed culture of innovation. This done by following the Reform Models developed by the author and presented in this book.
But the really good news is that the reforms can be largely implemented using your own company’s resources. With the help of a TQM /Lean temporary Training Consultant and a single Management Consultant to guide the implementation for the first six months, when the company can be begin saving $millions. The outcome is vibrant company who’s productivity cannot be matched by competitors.
The biggest competitive news in recent years is Toyota’s winning the competitive struggle against the big three Ford, GM and Chrysler. Toyota used “Total Quality Management (TQM)” to improve its automobiles and “Enterprise Lean” to improve its systems throughout its company to gain competitive advantage. In spite of evidence to the contrary most American CEO’s still believe that Lean is used only to improve the efficiency of hourly workers. The result for most American companies has been competitive stagnation and slow growth compounded by the recession. But now we have a breakthrough we now know how to manage the use of the Japanese tools to achieve maximum competitiveness.
The author recommends that the company’s products be designed for the customer’s needs and meets the highest quality. Then use TQM and Enterprise Lean to fix the company’s systems to get maximum efficiency while developing a culture of innovation. The final step is to replace the bureaucratic organization currently used in most companies with a Team Management organization. The breakthrough is in the step by step approach used in the author’s Reform Models.
Here is how the General Reform Model works.
Phase 1. Following the Toyota method “TQM” and “Enterprise Lean” are implemented throughout the company by training all employees in the use of the tools. There are two levels of training the high level training using Lean is for Management teams to study and improve systems which cross departmental lines as well as inter company operations such as material delivery systems and document flow systems. Other Lean Teams target the functions of the company where office workers and hourly shop floor employees work. The Teams meet once a week using TQM to get the highest quality product and the Lean tool Value Stream Mapping to fix their systems. The outcome is a high quality product and maximum improvement in efficiency for all of the company’s manufacturing systems while empowering employees to innovate in their jobs.
Phase 2. When the first phase is nearly completed the second phase can begin by bringing in Budget Analysts and Industrial Engineers to analyze the Lean study data and determine the cost savings for the current method and the improved method. The result is to right-size the staffing required to do a function and to develop a bottoms-up budget for the function. The outcome is to get the highest efficiency possible while maintaining the effectiveness of the function. Staffing reductions should be close to 20%.
Phase 3. After the Lean Teams have worked together as a team for a period of six months we can begin the last phase of converting the entire organization from a bureaucratic organization to Team Managed organization. The high level Lean Teams form Group Steering Teams to manage several related grouped functions. At the same time the self-managed Functional Team leaders assume the responsibility for their functions. The reform process is a smooth operation with the outcome being the reinvention of the company leading to the highest possible competitiveness.
Other Reform Models target specific industry problem areas. The Consolidation Reform Model focuses on consolidating duplicated service functions and disparate organizations. And the Central IT Cloud Systems Reform Model implements a new IT facility based on a modern database architecture creating an open flexible Relational Database Management system.
Product Details
BN ID: | 2940013793507 |
---|---|
Publisher: | EPUB BUD |
Publication date: | 12/27/2011 |
Series: | Reinventing Government and Industry , #4 |
Sold by: | Barnes & Noble |
Format: | eBook |
File size: | 219 KB |
About the Author
Lawrence Rosier is a Management Consultant specializing in Government and Industry Reform. He was formerly a Management Consultant with Alexander Proudfoot and Scheduling Corp. both firms located in Chicago. He has served on the staffs of: the Manager of Special Projects, Boeing Co., President of McDonnell Douglas Missile Systems Co. and Vice President of Manufacturing of McDonnell Douglas Missile Systems Co. Education includes degrees in Industrial Engineering and Secondary Education. He was a graduate instructor at the University of Washington Experimental Education Unit. He was also the Manager of Manufacturing Engineering for Multiplex Company in St. Louis.
His most significant achievement in the 1980s was the proposal and acceptance by Sanford McDonnell CEO of McDonnell Douglas Corp. of a modification to the company’s Quality of Work Life (QWL) implementation (the forerunner of Lean Manufacturing). The modification replaced the existing Bureaucratic organization with a Team Management organization consisting of Steering Management Teams and Functional Management Teams for the McDonnell Douglas Missile Systems Co. This Team Management style was enthusiastically received by employees and inspired employee innovation. It was used successfully for over ten years until the sale of the company to Boeing in the 1990’s.
His most significant achievement in the 1980s was the proposal and acceptance by Sanford McDonnell CEO of McDonnell Douglas Corp. of a modification to the company’s Quality of Work Life (QWL) implementation (the forerunner of Lean Manufacturing). The modification replaced the existing Bureaucratic organization with a Team Management organization consisting of Steering Management Teams and Functional Management Teams for the McDonnell Douglas Missile Systems Co. This Team Management style was enthusiastically received by employees and inspired employee innovation. It was used successfully for over ten years until the sale of the company to Boeing in the 1990’s.
From the B&N Reads Blog
Page 1 of