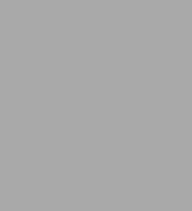
Maintaining Small-Farm Equipment: How to Keep Tractors and Implements Running Well. A Storey BASICS® Title
96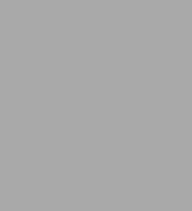
Maintaining Small-Farm Equipment: How to Keep Tractors and Implements Running Well. A Storey BASICS® Title
96eBook
Available on Compatible NOOK devices, the free NOOK App and in My Digital Library.
Related collections and offers
Overview
Product Details
ISBN-13: | 9781612125282 |
---|---|
Publisher: | Storey Publishing, LLC |
Publication date: | 09/08/2015 |
Series: | Storey Basics |
Sold by: | Hachette Digital, Inc. |
Format: | eBook |
Pages: | 96 |
File size: | 6 MB |
About the Author
Ann Larkin Hansen is the author of The Backyard Homestead Seasonal Planner, The Organic Farming Manual, The Electric Fencing Handbook, Finding Good Farmland, and Making Hay; coauthor of A Landowner’s Guide to Managing Your Woods with consulting forester Dennis Waterman and master logger Mike Severson; and coauthor with her husband, Steve, of Maintaining Small-Farm Equipment. She has been a journalist for more than 30 years, specializing in organic agriculture and sustainable forestry. A homesteader and a small-scale organic farmer, she lives with her family on a farm in northern Wisconsin.
Read an Excerpt
CHAPTER 1
Parts
The various equipment available to the small farmer is built from a fairly standard palette of part types. Understand the function of each type of part and see how the parts are assembled; you can then reason through how power is moved from engine to application. Learning how to keep equipment working follows logically from this starting point, so we'll begin by discussing the types of parts common on farm equipment — fasteners; wheels and shafts; bearings and bushings; and hoses and lines — and their functions.
Each type of part comes in a variety of permutations; for example, not all springs look like a coiled wire. If possible, read this chapter with a piece of equipment in front of you so you can get a real-life look at types of parts; illustrations and text are great starting points, but getting your hands on metal is necessary to really grasp how things fit together.
Fasteners
Parts that hold things together are employed whenever you need to attach an implement, disassemble something to do general maintenance, or make a repair. The most common types of fasteners are bolts, rivets, clips, spring clips, keys, cotter pins, hose clamps, springs, shafts, U-joints, and hitch pins.
Bolts, Nuts, and Washers
Bolts are threaded metal shafts that are blunt on one end and have a head on the other. To hold them in place requires screwing a nut onto the shaft, or screwing the bolt into a threaded recess. Nuts are either standard or locknuts, which are designed to provide extra holding friction where there's constant vibration. Washers are used when a hole is bigger than the bolt head or nut, or to hold the bolt head or nut farther from the hole to shorten how much shaft sticks out the other side. Split or star-type washers have the same function as a locknut.
Four Important Things to Know about Bolts
1. Bolts are sized by the length and thickness of the shaft and defined by thread count (coarse or fine) and head type: for example, a quarter-inch by two-and-a-half-inch (¼ " x ½") fine-thread hex-head bolt.
2. Bolt heads (and threads, nuts, and shaft sizes) are made to either metric or US measure, so you'll need either US or metric socket wrenches (see chapter 4 on tools) or, more likely, both.
3. Bolts come in varying degrees of hardness. Numbers 2, 5, and 8 bolts (from softest to hardest) are the grades most commonly used in machinery. Hardness is indicated by the number of lines on the head: no lines for grade 2, three lines for grade 5, and six lines for grade 8. Metric bolts are marked with the numbers 8.8, 10.9, and 12.9 for equivalent grades. When you need to replace a bolt, the new bolt ideally should be of the same hardness.
4. The compressive friction of the bolt head and the nut against the pieces they are fastening together is what gives the connection strength; in other words, loose bolts wear and break more easily than tight bolts.
Rivets
Machine rivets have smooth shafts, half-round heads, and a very low profile; they're used to hold parts moving through tight spaces. Removing and installing rivets is done with a riveting tool. You will run across rivets mostly on older equipment. Since rivets can be fussy to replace when worn or broken, if there is room to substitute bolts it makes future repairs simpler.
Clips, Cotter Pins, and Keys
Clips of various sizes and shapes are used to hold and align parts where there won't be too much force and are designed for quick insertion and removal. The most common is the hitch pin clip, which is pushed through a hole in the bottom of a hitch pin (which connects an implement to the tractor) and keeps the pin from bouncing out.
Cotter pins are a specialized type of clip, made of soft metal so they will break under unusual force and spare the more expensive parts they hold together. They're also used to lock nuts in place. They are intended to stay in place until they fail.
Keys are used to lock together a shaft and pulley or shaft and sprocket. Short canals or grooves are machined on the exterior of the shaft and the interior opening in the pulley or sprocket, and the key (either rectangular or half round — called a half-moon or Woodruff key) slips into the grooves and locks the two parts together. A set screw — a short, stubby screw that screws through a threaded hole in the exterior part to bear on the key or directly on the shaft — may be used as insurance to prevent the key or shaft from slipping out.
Zerks
Also called a grease fitting, a zerk consists of a round head with a spring-loaded ball valve which looks like the tip on a ballpoint pen. It is attached to a hollow, threaded shank that screws into a port in the equipment wherever grease needs to be delivered to moving parts.
Spring Clips
A spring clip is a slim metal bracelet with a cut in it that is slipped into a groove around a shaft to hold a rotating wheel in place on the shaft. On either cut end is a loop for the points of a spring clip tool (a specialized type of pliers), used to install and remove spring clips.
Springs
Springs hold parts together in a number of ways, depending on what's needed: flexible contact, reducing shock or impact, allowing connected parts to move somewhat independently of each other, or as part of a mechanism to engage and disengage two other parts. When a spring breaks or is distorted, it should be replaced with a close if not exact replica, so that its function is maintained.
Spare Parts to Have on Hand
Available at farm equipment stores, and many hardware and auto supply stores:
* Selection of bolts, nuts, and washers (purchased or scavenged)
* Selection of rivets if any of your equipment has rivets
* Selection of cotter pins
* Selection of zerks
* Selection of chain links
* Extra hitch pins with clips
* Selection of hose clamps
* Selection of bushings and spacers (purchased or scavenged)
Available from equipment dealers or from the manufacturer:
* Spare belts (specific to each machine)
* Air and oil filters (specific to each particular engine)
* Spark plugs (specific to each particular engine)
* Parts that frequently need replacing on your equipment, such as rake teeth, cutter bar sections, cultivator sweeps, etc.
Wheels and Shafts
Wheels come in all shapes and sizes on farm equipment, from tires and sprockets to pulleys and gears. Wheels fit on shafts, which are long metal rods. The shaft between tires is called an axle; a short, tapered shaft is called a spindle. A spindle is a type of half axle which can be articulated to allow the tire to steer independently of the axle. A shaft that has a pulley or sprocket on it may also be called a spindle.
Tires
Farm equipment tires are built and treaded for traction, not speed. The rear tires on tractors are usually filled with a mix of calcium chloride and water to give them added weight for better traction.
Universal Joints
A universal joint (more commonly referred to as a U-joint) creates a flexible joint between two shafts. The ends of the shafts are U-shaped and connected by a metal cross with bearings at each corner where it attaches to each of the legs of the U-shaped ends. The bearings allow one shaft to turn freely side to side and the other to move freely up and down, allowing changes in the angle, all while the shafts are spinning in unison. U-joints should be greased diligently.
Pulleys and Sprockets
A pulley is a grooved wheel made to hold a belt, while a sprocket is a wheel with cogs made to hold a chain. The relative sizes of pulleys and sprockets determine the gear ratio, serving to increase or decrease power versus speed as required for function.
Gears
Gears are cogged wheels fitted tightly together in precise combinations to change the ratio of force to speed between engine and implement, and to change the direction of power, such as when it needs to go around a corner. For the most part, gears on farm equipment, though essential, are unseen inside sealed gearboxes and rarely need attention.
PTO Shaft
Where the power source is separate from the implement, a short, splined power takeoff (PTO) shaft — on a tractor, for example — inserts into a splined receiving shaft extending from the implement to deliver power to the working parts. PTOs have either six splines and turn at 540 rpm (revolutions per minute) or 21 splines and turn at 1000 rpm. The PTO shafts of implements have to match those on the tractor.
The short, protruding PTO shaft is probably the most dangerous part of any piece of equipment you'll own; brushing it with a loose shoelace when it's running can get your foot ripped off. Make sure there's a guard over it, and never get close to a running PTO (or a rotating U-joint).
Clutches
A clutch interrupts a driveshaft so a power source can be engaged and disengaged, which allows the engine to keep running while wheels and the PTO are not. Tractors with "live" PTOs (that is, all but the oldest tractors) have separate clutches for wheels and PTO. Clutch repair is generally a job for professionals.
A second type of clutch found on some bigger implements is the slip clutch (also called an overriding clutch), which is engineered to disengage under exceptional force, to prevent other parts from breaking. Slip clutch work is generally within reach of the average farm shop.
Belts and Chains
Belts and chains are common on all types of equipment, and they loosen, wear, and break fairly often. Both function by being wrapped around two wheels (pulleys or sprockets), one of which is turned by the engine or motion of the wheels, moving the belt or chain, which then turns the pulley or sprocket at the other end, which is attached to and turns a working part of the implement.
Rubber belts may have a V-shape in cross section and then are called V-belts, but there are other types, and it's important to replace a bad belt with another of precisely the same length and shape. Very old equipment may have leather belts; apply spray-on leather-belt conditioner to make these last. Chains must be sized to fit the sprockets; they're used where no slippage is wanted (belts allow for a little slippage).
Bearings and Bushings
When metal moves against metal, it binds and grinds unless a fluid or mechanism or combination of the two is put in place to minimize the friction. Grease and oil are the fluids (see chapter 3); bearings and bushings are the mechanisms used to minimize friction.
Bushings are thick, relatively short metal cylinders made of softer, more slippery metal, used to provide space between moving parts. Bearings are more complex, precisely machined, and expensive.
Bearings allow wheels to turn independently of an axle, spindle, or shaft. On farm equipment, most bearings are made of little steel balls or cylinders that are packed in a bed of grease in a groove inside a metal doughnut-shaped "raceway" and capped with another raceway. The raceways move separately, the bearings rolling in between to prevent friction between top and bottom. Bearings are either sealed and need no regular attention, or unsealed and greased by disassembling and hand-packing, or through an external zerk.
Hoses, Lines, and Parts Specific to Farm Implements
Hoses and lines (small versions of hoses) are used to circulate fluids, including fuel, coolant, and hydraulic fluid. Coolant hoses and fuel lines are attached with clamps or fittings, while higher pressure hydraulic hoses utilize couplings, either screw-together or quick couplings. Hose clamps are perforated strips of flexible metal that cinch around a hose end where the hose fits over a connection. A small bolt holds the clamp tight, keeping the hose in place.
Parts that contact dirt, seeds, weeds, crops, and manure are specific to the job and, because of constant hard use, need to be replaced fairly often. Implements are designed to make this routine chore simple, and replacements are commonly available at farm stores and equipment dealers. Though the variety of parts in this category is huge, some of the most common are discs, sweeps, coulters, cutter bar sections, spring teeth, and rake teeth.
CHAPTER 2
Systems
Systems are assemblies of parts that create, move, and apply power; move fluids; and cool and lubricate. An engine has five basic systems: fuel, electrical, lubrication, cooling, and air intake/exhaust. The system that moves power from engines to implements is a drivetrain. Small machines may make this connection by belt or chain. On large equipment, such as tractors and skidsteers, there is often a gearbox and/or a hydraulic system for moving power from engine to implement.
When dealing with equipment parts and systems, think in terms of "if this, then that." For example, if there's a zerk, then there's a bearing, bushing, or shaft. If there are hydraulic hoses, then there's a cylinder, pump, and couplings. If there's a wheel — whether it's a tire, sprocket, or pulley — then there's a shaft and bearings.
Fuel System
In a gas-powered engine, fuel is moved by gravity or a fuel pump from the tank through a line with either a filter or screen and into the carburetor, where it is mixed with air. Inside the engine block, the air-fuel mix is sucked into the cylinders, where it is compressed by the pistons and ignited by a spark from the spark plugs. The fuel explodes, driving the pistons back. Rods attached to the bottoms of the pistons turn the crankshaft, converting the energy of the chemical explosion into mechanical power. Note that air, fuel, and spark must all be present for combustion to take place in a gas engine.
A diesel engine has no carburetor or spark plugs; the fuel is injected directly into the cylinders, where it is mixed with air. Extreme compression of the mix causes ignition.
This very simplified explanation of the workings of an internal combustion engine completes the description of the fuel system and illustrates where the fuel system intersects with the electrical system, the air intake/exhaust system, and the drivetrain.
Two-Cycle vs. Four-Cycle Engines
Larger engines, whether gas or diesel powered, are four-cycle, so-called after the two-up plus two-down strokes of the pistons which complete the power and recharge cycles. The first down-and-up crankshaft rotation draws in and then compresses the fuel air mix. A spark delivered to the cylinder at peak compression ignites the mix. The resulting explosion powers the second down-and-up rotation, driving the piston down to turn the crankshaft, which creates momentum to move the piston upward to expel the exhaust gases and set up the next cycle. Small engines are gas powered and either four- or two-cycle.
Two-cycle engines tend to be smaller and lighter, but are less efficient. This type of engine utilizes just one up and one down stroke of the piston for intake, ignition, and exhaust.
For everyday purposes, the difference between the types is that four-cycle engines have a separate system for lubrication, while two-cycles add oil to the gas, which lubricates the entire engine. Since two-cycle engines don't require separate engine lubrication systems, you don't ever have to change the oil or an oil filter.
Very few two-cycle engines mix the gas and oil internally; most (chain saws are one example) require premixing the gas and oil before adding it to the fuel tank. Use the correct type of oil, and the correct proportions of gas and oil, as specified in the owner's manual. (Don't forget that a chainsaw has a separate lubrication system for the cutter bar and chain, which uses a different type of oil than the engine.)
SCHEMATIC OF FUEL, AIR, AND ELECTRICAL SYSTEMS
Valves
Valves are metering devices for liquids and gases, which operate inside a line or chamber that contains the fluid, forcing it to pass through the valve. They're found in several places in different systems. Hydraulic controls are valves, as are the choke and carburetor float valve in the fuel system, combustion valves at the cylinders, and the thermostat in a coolant system.
(Continues…)
Excerpted from "Maintaining Small-Farm Equipment"
by .
Copyright © 2015 Ann Larkin Hansen and Steven Frederick Hansen.
Excerpted by permission of Storey Publishing.
All rights reserved. No part of this excerpt may be reproduced or reprinted without permission in writing from the publisher.
Excerpts are provided by Dial-A-Book Inc. solely for the personal use of visitors to this web site.
Table of Contents
Acknowledgments,
Introduction,
Dedication,
Chapter One: Parts,
Chapter Two: Systems,
Chapter Three: Fluids,
Chapter Four: Tools,
Chapter Five: Maintenance,
Chapter Six: Diagnostics,
Chapter Seven: Repairs,
Chapter Eight: Getting Professional Help,
Resources,
Maintenance Log,
Index,
Other Storey Titles,
The Storey BASICS Series,
Copyright,
Share Your Experience!,