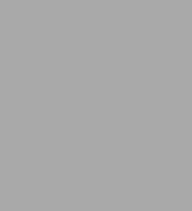
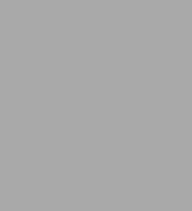
eBook
Available on Compatible NOOK devices, the free NOOK App and in My Digital Library.
Related collections and offers
Overview
Power transfer for large systems depends on high system voltages. The basics of high voltage laboratory techniques and phenomena, together with the principles governing the design of high voltage insulation, are covered in this book for students, utility engineers, designers and operators of high voltage equipment.
In this new edition the text has been entirely revised to reflect current practice. Major changes include coverage of the latest instrumentation, the use of electronegative gases such as sulfur hexafluoride, modern diagnostic techniques, and high voltage testing procedures with statistical approaches.
- A classic text on high voltage engineering
- Entirely revised to bring you up-to-date with current practice
- Benefit from expanded sections on testing and diagnostic techniques
Product Details
ISBN-13: | 9780080508092 |
---|---|
Publisher: | Elsevier Science |
Publication date: | 07/17/2000 |
Sold by: | Barnes & Noble |
Format: | eBook |
Pages: | 534 |
File size: | 17 MB |
Note: | This product may take a few minutes to download. |
Read an Excerpt
High Voltage Engineering Fundamentals
By E. Kuffel W.S. Zaengl J. Kuffel
Newnes
Copyright © 2000 E. Kuffel, W.S. Zaengl and J. KuffelAll right reserved.
ISBN: 978-0-08-050809-2
Chapter One
Introduction
1.1 Generation and transmission of electric energy
The potential benefits of electrical energy supplied to a number of consumers from a common generating system were recognized shortly after the development of the 'dynamo', commonly known as the generator.
The first public power station was put into service in 1882 in London (Holborn). Soon a number of other public supplies for electricity followed in other developed countries. The early systems produced direct ccurrent at low-voltage, but their service was limited to highly localized areas and were used mainly for electric lighting. The limitations of d.c. transmission at low-voltage became readily apparent. By 1890 the art in the development of an a.c. generator and transformer had been perfected to the point when a.c. supply was becoming common, displacing the earlier d.c. system. The first major a.c. power station was commissioned in 1890 at Deptford, supplying power to central London over a distance of 28 miles at 10 000 V. From the earliest 'electricity' days it was realized that to make full use of economic generation the transmission network must be tailored to production with increased interconnection for pooling of generation in an integrated system. In addition, the potential development of hydroelectric power and the need to carry that power over long distances to the centres of consumption were recognized.
Power transfer for large systems, whether in the context of interconnection of large systems or bulk transfers, led engineers invariably to think in terms of high system voltages. Figure 1.1 lists some of the major a.c. transmission systems in chronological order of their installations, with tentative projections to the end of this century.
The electric power (P) transmitted on an overhead a.c. line increases approximately with the surge impedance loading or the square of the system's operating voltage. Thus for a transmission line of surge impedance ZL ([congruent to]250Ω) at an operating voltage V, the power transfer capability is approximately P = V2/ZL, which for an overhead a.c. system leads to the following results:
V(kV) 400 700 1000 1200 1500 P(MW) 640 2000 4000 5800 9000
The rapidly increasing transmission voltage level in recent decades is a result of the growing demand for electrical energy, coupled with the development of large hydroelectric power stations at sites far remote from centres of industrial activity and the need to transmit the energy over long distances to the centres. However, environmental concerns have imposed limitations on system expansion resulting in the need to better utilize existing transmission systems. This has led to the development of Flexible A.C. Transmission Systems (FACTS) which are based on newly developing high-power electronic devices such as GTOs and IGBTs. Examples of FACTS systems include Thyristor Controlled Series Capacitors and STATCOMS. The FACTS devices improve the utilization of a transmission system by increasing power transfer capability.
Although the majority of the world's electric transmission is carried on a.c. systems, high-voltage direct current (HVDC) transmission by overhead lines, submarine cables, and back-to-back installations provides an attractive alternative for bulk power transfer. HVDC permits a higher power density on a given right-of-way as compared to a.c. transmission and thus helps the electric utilities in meeting the environmental requirements imposed on the transmission of electric power. HVDC also provides an attractive technical and economic solution for interconnecting asynchronous a.c. systems and for bulk power transfer requiring long cables.
Table 1.1 summarizes a number of major HVDC schemes in order of their in-service dates. Figure 1.2 provides a graphic illustration of how HVDC transmission voltages have developed. As seen in Figure 1.2 the prevailing d.c. voltage for overhead line installations is 500 kV. This 'settling' of d.c. voltage has come about based on technical performance, power transfer requirements, environmental and economic considerations. Current trends indicate that d.c. voltage levels will not increase dramatically in the near future.
1.2 Voltage stresses
Normal operating voltage does not severely stress the power system's insulation and only in special circumstances, for example under pollution conditions, may operating voltages cause problems to external insulation. Nevertheless, the operating voltage determines the dimensions of the insulation which forms part of the generation, transmission and distribution equipment. The voltage stresses on power systems arise from various overvoltages. These may be of external or internal origin. External overvoltages are associated with lightning discharges and are not dependent on the voltage of the system. As a result, the importance of stresses produced by lightning decreases as the operating voltage increases. Internal overvoltages are generated by changes in the operating conditions of the system such as switching operations, a fault on the system or fluctuations in the load or generations.
Their magnitude depends on the rated voltage, the instance at which a change in operating conditions occurs, the complexity of the system and so on. Since the change in the system's conditions is usually associated with switching operations, these overvoltages are generally referred to as switching overvoltages.
In designing the system's insulation the two areas of specific importance are:
(i) determination of the voltage stresses which the insulation must withstand, and
(ii) determination of the response of the insulation when subjected to these voltage stresses.
The balance between the electric stresses on the insulation and the dielectric strength of this insulation falls within the framework of insulation coordination and will be discussed in Chapter 8.
1.3 Testing voltages
Power systems equipment must withstand not only the rated voltage (Vm), which corresponds to the highest voltage of a particular system, but also overvoltages. Accordingly, it is necessary to test h.v. equipment during its development stage and prior to commissioning. The magnitude and type of test voltage varies with the rated voltage of a particular apparatus. The standard methods of measurement of high-voltage and the basic techniques for application to all types of apparatus for alternating voltages, direct voltages, switching impulse voltages and lightning impulse voltages are laid down in the relevant national and international standards.
1.3.1 Testing with power frequency voltages
To assess the ability of the apparatus's insulation withstand under the system's power frequency voltage the apparatus is subjected to the 1-minute test under 50 Hz or 60 Hz depending upon the country. The test voltage is set at a level higher than the expected working voltage in order to be able to simulate the stresses likely to be encountered over the years of service. For indoor installations the equipment tests are carried out under dry conditions only. For outdoor equipment tests may be required under conditions of standard rain as prescribed in the appropriate standards.
1.3.2 Testing with lightning impulse voltages
Lightning strokes terminating on transmission lines will induce steep rising voltages in the line and set up travelling waves along the line and may damage the system's insulation. The magnitude of these overvoltages may reach several thousand kilovolts, depending upon the insulation. Exhaustive measurements and long experience have shown that lightning overvoltages are characterized by short front duration, ranging from a fraction of a microsecond to several tens of microseconds and then slowly decreasing to zero. The standard impulse voltage has been accepted as an aperiodic impulse that reaches its peak value in 1.2 µsec and then decreases slowly (in about 50 µsec) to half its peak value. Full details of the waveshape of the standard impulse voltage together with the permitted tolerances are presented in Chapter 2, and the prescribed test procedures are discussed in Chapter 8.
In addition to testing equipment, impulse voltages are extensively used in research laboratories in the fundamental studies of electrical discharge mechanisms, notably when the time to breakdown is of interest.
1.3.3 Testing with switching impulses
Transient overvoltages accompanying sudden changes in the state of power systems, e.g. switching operations or faults, are known as switching impulse voltages. It has become generally recognized that switching impulse voltages are usually the dominant factor affecting the design of insulation in h.v. power systems for rated voltages of about 300 kV and above. Accordingly, the various international standards recommend that equipment designed for voltages above 300 kV be tested for switching impulses. Although the wave-shape of switching overvoltages occurring in the system may vary widely, experience has shown that for flashover distances in atmospheric air of practical interest the lowest withstand values are obtained with surges with front times between 100 and 300 µsec. Hence, the recommended switching surge voltage has been designated to have a front time of about 250 µsec and half-value time of 2500 µsec. For GIS (gas-insulated switchgear) on-site testing, oscillating switching impulse voltages are recommended for obtaining higher efficiency of the impulse voltage generator Full details relating to generation, measurements and test procedures in testing with switching surge voltages will be found in Chapters 2, 3 and 8.
1.3.4 D.C. voltages
In the past d.c. voltages have been chiefly used for purely scientific research work. Industrial applications were mainly limited to testing cables with relatively large capacitance, which take a very large current when tested with a.c. voltages, and in testing insulations in which internal discharges may lead to degradation of the insulation under testing conditions. In recent years, with the rapidly growing interest in HVDC transmission, an increasing number of industrial laboratories are being equipped with sources for producing d.c. high voltages. Because of the diversity in the application of d.c. high voltages, ranging from basic physics experiments to industrial applications, the requirements on the output voltage will vary accordingly. Detailed description of the various main types of HVDC generators is given in Chapter 2.
1.3.5 Testing with very low-frequency voltage
In the earlier years when electric power distribution systems used mainly paper-insulated lead covered cables (PILC) on-site testing specifications called for tests under d.c. voltages. Typically the tests were carried out at 4–4.5V0. The tests helped to isolate defective cables without further damaging good cable insulation. With the widespread use of extruded insulation cables of higher dielectric strength, the test voltage levels were increased to 5–8V0. In the 1970s premature failures of extruded dielectric cables factory tested under d.c. voltage at specified levels were noted. Hence on-site testing of cables under very low frequency (VLF) of ~0.1Hz has been adopted. The subject has been recently reviewed.
Chapter Two
Generation of high voltages
A fundamental knowledge about generators and circuits which are in use for the generation of high voltages belongs to the background of work on h.v. technology.
Generally commercially available h.v. generators are applied in routine testing laboratories; they are used for testing equipment such as transformers, bushings, cables, capacitors, switchgear, etc. The tests should confirm the efficiency and reliability of the products and therefore the h.v. testing equipment is required to study the insulation behaviour under all conditions which the apparatus is likely to encounter. The amplitudes and types of the test voltages, which are always higher than the normal or rated voltages of the apparatus under test, are in general prescribed by national or international standards or recommendations, and therefore there is not much freedom in the selection of the h.v. testing equipment. Quite often, however, routine testing laboratories are also used for the development of new products. Then even higher voltages might be necessary to determine the factor of safety over the prospective working conditions and to ensure that the working margin is neither too high nor too low. Most of the h.v. generator circuits can be changed to increase the output voltage levels, if the original circuit was properly designed. Therefore, even the selection of routine testing equipment should always consider a future extension of the testing capabilities.
(Continues...)
Excerpted from High Voltage Engineering Fundamentals by E. Kuffel W.S. Zaengl J. Kuffel Copyright © 2000 by E. Kuffel, W.S. Zaengl and J. Kuffel . Excerpted by permission of Newnes. All rights reserved. No part of this excerpt may be reproduced or reprinted without permission in writing from the publisher.
Excerpts are provided by Dial-A-Book Inc. solely for the personal use of visitors to this web site.