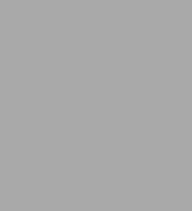
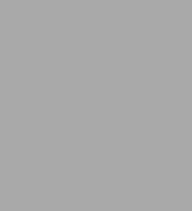
eBook
Available on Compatible NOOK devices, the free NOOK App and in My Digital Library.
Related collections and offers
Overview
Hand tool woodworking can be a source of great pride, satisfaction and amazing results--not to mention less noise and sawdust. But there's a lot to learn, what with a seemingly endless array of chisels and mallets to workbenches and handplanes. You'll learn proven methods for sharpening your tools, prepping your stock and timeless joinery techniques including mortise-and-tenon joins, dovetails, rabbets and others. Within these pages you'll find:
• Advice for selecting the tools you need and setting up shop
• Complete instructions for using the tools you'll reach for time and again
• Tuning processes for keeping your tools sharp and precise
• Technique variations and alternate methods so you can decide what works best for you
Take the mystery out of hand tools and experience the satisfaction of crafting something truly handmade.
Product Details
ISBN-13: | 9781440348921 |
---|---|
Publisher: | Penguin Publishing Group |
Publication date: | 01/12/2018 |
Sold by: | Penguin Group |
Format: | eBook |
Pages: | 274 |
Sales rank: | 741,461 |
File size: | 140 MB |
Note: | This product may take a few minutes to download. |
About the Author
Read an Excerpt
CHAPTER 1
THE TOOLS
WORKBENCHES
The workbench holds your work in place so that you can work faces, edges and ends. Workbenches are equipped with a variety of workholding mechanisms, the vise being the most familiar. However, there are also a number of alternatives to vises.
There are many different designs to choose from, each with its own relative strengths and weaknesses. Costs vary significantly depending on whether you buy one or build it yourself, and what it uses for workholding.
The advantage of a large, heavy workbench is that it will stay in place in use, especially when planing. The biggest problem with lighter workbenches is that they slide around too easily. Lightly built workbenches can also be rickety.
The advantage of a folding workbench is that you can use it in a very small space such as an apartment. Once you're done, fold it up and stand it in a corner. You can also take it with you for off-site work.
A workbench is a compromise of a number of requirements in terms of height, weight, structure, accessories and cost.
TOOLS
The basic tools are handsaws, handplanes and chisels, as well as measuring and marking tools. There are many additional tools for more specialized operations.
You don't need an entire wall full of tools or a large collection to get started. You can start out with a few basics, then add to that as your skills grow.
When buying tools, you really have two choices: good quality antique tools that were made at a time when everyone made their living using them, and modern, high-quality premium tools. Avoid cheap modern tools.
Good quality tools, whether old or new, exhibit good design, good materials and good workmanship. While they may be more expensive, they are lifetime investments. Inexpensive modern high-volume mass-produced tools are generally a poor investment – they are often cheaply made using poor- quality materials.
SAFETY
Hand Tool Safety
Before we use any hand tools, let's take a moment to talk about shop safety. Hand tools are similar in risk to working with kitchen implements. In general they're reasonably safe, but you're working around a lot of sharp edges and teeth. It's not unusual to have little nicks on your fingers, and you're probably going to end up needing a Band-Aid or two.
The one truly dangerous tool is the chisel, because like a large kitchen knife, it's a long, very sharp implement. Safety for the rest of the tools is fairly simple.
Most accidents are due to inattentiveness, improper handling or forcing tools.
Chisels
The safest way to handle a chisel is to always have two hands on it. Have one hand on the handle, the other hand somewhere along the blade. Never point it directly at your body, and never have any part of your body in front of the cutting path, especially your off hand.
You can also choke up on the end of the chisel with your fingers so that they act as a stop, leaving only the tip exposed. That limits how far the chisel can go, useful for working in joints.
A chisel can easily cause very severe cuts, and open up an arm or a hand if you run across its corner.
Be aware of the path the tool may take if something slips or a piece of wood breaks off. Make sure that the exit path is clear no matter what can happen.
Handsaws
Make sure that you're aware of the exit path of the saw. Avoid running the saw across your fingers, especially on the underside of the work.
Handplanes
Handplanes are large enough that you're typically going to have both hands on them. When you're handling them from the underside, always be aware of which way the blade cuts. It's safe to run your fingers from the back toward the front, but not the other direction.
Marking
When you're using a marking knife with a square, make sure that your fingers are not overlapping the straightedge. Make sure they're clear and that you're not going to run your knife over your fingertips.
Marking gauges have sharp points – don't grab the gauge by the points.
Brace & Bit, Drills
Be aware of where the point is going to come out on the opposite side.
Mallet
When using a chisel and mallet, make sure that your thumb and the web of your hand are clear of the top of the chisel. Make sure there's a clear striking area for the mallet.
Dull Tools
Don't use dull tools. If a tool is dull, sharpen it. Dull tools skip across the work, sliding around unpredictably instead of cutting – and they require more force to make them work.
SAW TYPES
Anatomy of a Handsaw
A handsaw consists of the handle and the saw plate. The far end of the toothed edge is called the toe – the near end is the heel.
The shape of a saw handle isn't just decoration, it's ergonomics. This is a highly evolved shape that makes it comfortable to use for long periods, using either a one- or two-handed grip. This gives you control and makes the saw comfortable to use.
Saw handles aren't meant for a full hand, they're meant for three fingers, with the index finger extended along the handle.
This extended finger is very important. I call it the "trigger finger grip." Use this on all your handplanes and saws. It gives you extra control to prevent wobble and maintain a specific angle, especially when using small joinery saws for precision cutting, and using handplanes to plane edges.
Get into the habit of using that trigger finger, even when you're doing rough work that doesn't call for precision – you want it to become second nature. That's one of the main things I have to remind people to do when they're first sawing and planing.
Saw Varieties
There are three general types of saws: regular handsaws, smaller joinery saws with backs, known as backsaws, and various framesaws (sometimes also known as bowsaws). Shorter versions of regular handsaws are known as panel saws.
Regular handsaws rely on a thicker plate for stiffness. Backsaws have thinner plates. The back, or spine, provides stiffness. Frame saws have narrow, thin blades that are much more flexible. They provide stiffness by placing the blade under tension, effectively stretching it in the frame.
For all these general types of saws there are two tooth types, determined by function: ripsaws and crosscut saws. Ripsaws are for cutting with the grain (think of ripping a piece of paper lengthwise into strips). Crosscut saws are for cutting across the grain.
The difference is in the way the teeth are filed. Other than that and cosmetic differences, rip and crosscut saws are identical.
For angled cuts, look at how the cut is oriented relative to the grain direction. If the cut is mostly across the grain, use a crosscut saw. Otherwise, use a ripsaw.
There are also various hybrid saws, which have some combination of rip and crosscut teeth.
Rip teeth are the simplest, because they're just filed straight across. Crosscut teeth are more complicated, because instead of being filed straight across, each tooth is filed at an alternating angle.
Both types of teeth are filed with the same triangular file, but it's oriented differently.
The angle at which the leading edge of a tooth is pitched back is called the "rake angle." The alternating angle for filing across crosscut teeth is called the "fleam angle." The bottom space between teeth is called the "gullet." The size of the teeth is called the "pitch" (not to be confused with how the teeth are pitched back).
Rip teeth have very little rake angle, and no fleam angle. Crosscut teeth have up to 30° of rake angle, and up to 20° of fleam angle. Both have gullets that are 60°, the gullet is just oriented differently due to the rake angle.
Sharpening
To sharpen a saw, set the triangular file into a gullet, oriented at the appropriate rake and fleam angles, and file both the leading edge of one tooth and the trailing edge of the tooth in front of it at the same time. Detailed instructions for saw sharpening can be found in Chapter 2.
Because rip teeth are all filed exactly the same, you can hold the file exactly the same way in each gullet. For crosscut teeth, you have to alternate the angle at each gullet.
The easiest way to do this consistently is to first file the odd gullets at one fleam orientation, then file the even gullets at the opposite fleam orientation. This produces the alternating facets on the leading and trailing edges of each tooth.
These filing patterns are what produce the functional differences in the teeth. When ripping, the rip teeth act like little chisels as you push them between the fibers of the wood. When crosscutting, the crosscut teeth act like little knives as you push them across the fibers, severing them. The rip teeth chisel out between the fibers, the crosscut teeth cut across the fibers.
Saw Pitch
Saw pitch, or tooth pitch, is measured in points per inch (ppi), and it's normally stamped at the heel of the saw. Sometimes a saw may have been re-toothed to a different pitch, so it no longer matches the stamping. Or it may have been resharpened past the stamping, resharpened so many times that the stamped number is gone.
To count the teeth, set a ruler at the point of one tooth, and then count the number of points up to one inch, including that first tooth.
Fine joinery saws are measured exactly the same as larger saws. The only difference is that the teeth are much smaller.
PLANE TYPES
Sizes & Numbers
The common metal planes are called "bench planes," because they stay on the bench due to frequent use. The cutters on planes are called "irons."
Different manufacturers use different numbering systems for identifying their planes. The most common is the Stanley system, numbered 1 through 8 for smallest to largest bench plane. These are bevel-down planes, where the iron is mounted in the plane with the bevel facing down. There are also bevel-up planes, where the iron is mounted in the plane with the bevel facing up.
The main question is, which order do you use them in? Do you go from largest to smallest? Smallest to largest? What's the difference?
The difference is that the length of the plane establishes its function. There are three functions for planes, in order of use: roughing, flattening and smoothing. Roughing means removing material quickly. Flattening means making the rough surface flat. Smoothing means getting the final, smooth surface. Flattening may also produce a smooth enough surface that further smoothing isn't necessary, particularly on edges.
Removing material is a rough operation, where you're not concerned yet about getting a flat, smooth surface. This reduces the thickness or width of a piece, getting it roughly to final dimension. Once that step is complete, flattening and smoothing are fine operations, getting the piece precisely to final dimension.
Long planes tend to ride across any high spots in the surface and flatten them out. Short planes tend to ride along the surface, following the contours more than flattening them out. All planes perform some flattening, but the difference in length means that a short plane is much more of a finishing plane, set for a very fine shaving to smooth the surface without appreciably affecting its flatness.
Because of this, long planes are used for flattening, and short planes are used for smoothing. Flattening is known as "jointing" or "trying," so long planes are known as jointers or trying planes. Jointing refers to flattening an edge, while trying refers to flattening a face, and most people use the same plane for both. Short planes are known as "smoothers."
Short numbers 1-4 are considered smoothers. Long numbers 6-8 are considered jointers. One of the factors to help you choose between planes of the same types is your size and strength. For instance, a #7 is heavier and longer than a #6, and a #3 is lighter than a #4.
What about the middle size #5 plane? This is known as a "jack plane." I like to use a jack strictly as a roughing plane, with the iron cambered – or sharpened to a curve. That curve allows the iron to take a deeper shaving, more of a heavy chip that feathers out on the sides. In contrast, the irons for jointers and smoothers are straight across, with the corners rounded or feathered off to avoid leaving plane tracks in the wood.
Therefore, the order of usage is a middle-size jack plane for roughing, a long jointer for flattening, and a short smoother for final smoothing.
Roughing can be very aggressive, taking anything from paper-thick shavings to nearly 1/8" chips, depending on the wood. Flattening is finer, from tissue paper to cardboard thickness. Smoothing is the very finest, from light feathery shaving to tissue paper thickness.
Some people like to use jack planes for everything, from roughing to jointing and smoothing. They may have different irons prepared for each usage. Bevel-up jacks are particularly useful for this.
Anatomy of a Handplane
Most handplanes are comprised of a few key parts including the main body of the plane, the frog (which supports the iron), a handle and knob for gripping, a sole and the iron. The following photos explain the various parts of typical handplanes and how they work.
Left to right: Stanley 7, 6, 5, 4, 3 and 2 planes. The #8 and #1 planes are less practical for general use.
The 3 general sizes in order of use: jack, jointer and smoother.
(A) A bench plane consists of a body, a frog assembly for supporting the iron, a handle, known as a "tote" and a knob. (B) The bottom side of the body is the bed – or sole – with a mouth for the cutter, known as the iron.
The iron is paired with a chipbreaker, and secured to the frog with a lever cap. The frog has an adjuster knob for adjusting the depth of cut (A), and a lateral adjustment lever for adjusting the angle of the iron across the mouth (B).
To remove the iron and chipbreaker assembly, lift the lever on the lever cap as shown in photo A. Slide the cap off, exposing the iron resting on the frog as shown in photo B. Lift that out of the mouth and over the center tensioning screw. This screw allows you to adjust the tension on the lever cap. You should be able to lift the lever of the cap easily, and it should click down in place when you lock it. Turn the screw to tighten or loosen it. Don't overtighten the screw, because that can distort the plane.
(Continues…)
Excerpted from "Hand Tool Basics"
by .
Copyright © 2017 Steve Branam.
Excerpted by permission of F+W Media, Inc..
All rights reserved. No part of this excerpt may be reproduced or reprinted without permission in writing from the publisher.
Excerpts are provided by Dial-A-Book Inc. solely for the personal use of visitors to this web site.
Table of Contents
Special Offers,
Introduction,
CHAPTER 1 THE TOOLS,
CHAPTER 2 SHARPENING,
CHAPTER 3 STOCK PREPARATION,
CHAPTER 4 SIMPLE JOINERY,
CHAPTER 5 MORTISE & TENON JOINERY,
CHAPTER 6 DOVETAIL JOINERY,
CHAPTER 7 BORING HOLES & CURVED WORK,