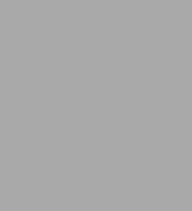
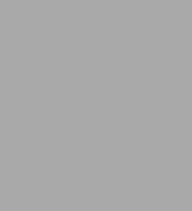
eBook
Related collections and offers
Overview
"Lucidly written and illustrated." — The Glass Engraver
If you've ever admired the exquisite beauty and craftsmanship of Steuben, Tiffany, Orrefors, or other fine engraved glass and wished you could engrave glass yourself, this book is for you. It provides step-by-step instructions for diamond-bur engraving, from making the first cut to displaying the finished work.
The author, a prize-winning engraver, provides a detailed summary of tools and equipment you will need and suggestions for setting up your workshop, along with easy-to-follow practice exercises to give you a feel for working with glass and glass-engraving equipment. Mr. Graham then guides students through four complete projects, ranging from a simple tree design to a more complex flower engraving.
Here are other practical features that make this book ideal for the novice: a useful discussion of design considerations and applications, review of supplemental tools and advanced techniques, expert advice on choosing glass, suggestions for the arrangement and lighting of finished pieces, and more. Over 100 helpful illustrations enhance the text.
With this inexpensive book as your guide, you'll find learning the fundamentals of glass engraving far easier than you might have imagined. Simply written and easy to understand, Engraving Glass: A Beginner's Guide is your personal invitation to enjoy the challenges and satisfactions of this rewarding craft.
Product Details
ISBN-13: | 9780486144153 |
---|---|
Publisher: | Dover Publications |
Publication date: | 04/07/2014 |
Series: | Dover Crafts: Glass Work |
Sold by: | Barnes & Noble |
Format: | eBook |
Pages: | 128 |
Sales rank: | 752,637 |
File size: | 13 MB |
Note: | This product may take a few minutes to download. |
Read an Excerpt
Engraving Glass
A Beginner's Guide
By Boyd Graham
Dover Publications, Inc.
Copyright © 1982 Van Nostrand Reinhold Company Inc.All rights reserved.
ISBN: 978-0-486-14415-3
CHAPTER 1
Glass Engraving Techniques and Equipment
In recent years, there has been a revival of interest in engraved glass on the part of collectors and practitioners alike. Unfortunately, there has been little information available on how it is accomplished for those who would like to try engraving. It is the purpose of this book to pass along to other artists the techniques that I use in the hope that they in turn can enjoy and help to perpetuate glass engraving. Too, it is the intention of this book to encourage an understanding and an appreciation for an ancient and beautiful art form.
TECHNIQUES
There are three methods used to engrave glass by cutting into the surface: copperwheel, stonewheel, and diamond bur. Although the first two are impractical for the amateur, an understanding of the principles involved is beneficial. These methods are described briefly to acquaint you with the tools and technique. However, diamond bur is the technique that will be used throughout this book.
Copperwheel Engraving
Copperwheel engraving is a highly skilled art and years of apprenticeship and experience are required to master the technique. The precision equipment, usually manufactured in Europe, is quite expensive. In this method, a copper wheel, chucked onto a steel shaft, is turned by a table-mounted lathe equipped with a variable speed control for the different cuts. The copper wheels are interchangeable and can vary in size from 1/16 inch (1.6 mm) to four or five inches (10.16 or 12.7 cm) in diameter. They are of various thicknesses and the cutting edges are square, rounded, or V shaped. A cutting abrasive, either silicon carbide or aluminum oxide in powdered form, is applied with a wedge-shaped felt strip that has been soaked in oil and attached so that it rides on the edge of the copper wheel. The revolving action of the wheel, along with the abrasive and oil mixture, makes the desired cut. The size of the wheel and the cut being made determine the revolving speed needed. The glass, or "metal," as it is called in the glass trade, is cradled in the hands and manipulated against the revolving copper wheel. The cuts made by copperwheel are smoother in texture than those made by diamond bur; otherwise, they are similar in appearance.
Stonewheel Engraving
The stonewheel engraver uses manufactured abrasive stone wheels of a fine grit quality that range from the size of a shirt button to two feet (60.96 cm) or larger in diameter. These stones are attached to a table-mounted arbor (a spindle or axel for holding the cutting tools). The engraver can vary the speed, depending upon the size of the stone. The engraver shapes the stone edge for the required cut by wearing away part of the stone with a shaping tool. A wet sponge is held in place at the edge of the stone as a coolant; it also absorbs the glass and abrasive residue. The cuts are then polished, using a wood, lead, or cork wheel (usually mounted on a separate machine) and cerium oxide polishing powder. The beautiful "cut crystal" vases and bowls that you can purchase in many glass shops are made by stonewheel engraving methods.
Diamond Bur Engraving
Diamond bur engraving differs from the other two methods in that the cutting tool is held like a pencil in one hand with the glass being held in the other hand. This allows more flexibility than either the copperwheel or stonewheel process, since both the tool and glass can be maneuvered. A flexible shaft tool attached to a motor is used. At the opposite end of the shaft is a handpiece, which holds the diamond bur. The bur is the cutting instrument and the revolving speed is controlled by a foot-operated rheostat. Water is dripped from a container onto the glass at the spot being cut; this acts as a cutting lubricant and coolant, and also carries off the glass particles that otherwise would fly up around the cut.
Diamond bur engraving is the least expensive of the three methods of engraving glass because of equipment costs and availability. It is also the easiest to learn. All that is required are the tools, the desire to do it, and the determination to learn how.
Copperwheel, stonewheel, and diamond bur engravings are done on the outer surfaces of the vessel, not on the interior surface. The intaglio decoration (a design depressed below the surface of the material) of stonewheel engraving is usually meant to be viewed from directly in front of the surfaces on which it is executed. Copperwheel and diamond bur engravings, on the other hand, because they are to be viewed from the other side, are usually cut intaglio to give a bas-relief (raised) effect. (On occasion, the copperwheel or diamond bur engraver may wish to extend his design completely around the outside of a vase or bowl, and naturally, when this occurs, it would be quite impossible to view the entire design as a bas-relief.) The cuts made by copperwheel and diamond bur are usually not polished, but retain a "frosty" look caused by the cutting tool. However, the engraver does have the option to polish a portion of the engraving to emphasize or enhance a point.
EQUIPMENT
The following is the basic equipment required for diamond bur engraving:
One-tenth horsepower electric motor with flexible shaft
Detachable handpiece and three sizes of collets
Foot rheostat for motor speed control
About twelve different shapes and sizes of diamond-impregnated burs
Diamond pencil or carbide-tipped scriber
China marking pencil
Tracing paper
Carbon paper
Binocular-type magnifier that fits on the head
Mask or respirator
Good lighting
Water source
Convenient working area
The above is the minimum equipment needed to get started. You may wish to add more tools as you progress, and I will describe these in later chapters.
Because your source of supplies will vary, no exact cost figure can be given here; however, the beginner could expect to spend about $300 for the initial equipment. You will find a list of suppliers, who can furnish you with their equipment costs, and their addresses at the end of this book.
Motor
There are several brands and types of motors with attached flexible shafts available on the market; these are used in industry and in the jewelry trade. One type rests horizontally on a stand and sits on the working surface. The model I prefer hangs vertically from a stand. This offers more freedom of movement, takes less space, and allows plenty of elbow room in the working area. Such motors are available with one-tenth horsepower and can achieve up to 25,000 rpm when governed by a foot-operated speed control rheostat, which must be purchased separately. The flexible steel shaft is covered by a durable plastic composition sheath that allows great maneuverability.
The motor with attached flexible shaft has a price range of $50 to $90. If your budget allows, it is wise to purchase a good motor that will give long service and good performance. In using the motor, never apply so much pressure with the bur that the machine stalls; a sudden stoppage or overload could cause severe damage to the flexible shaft. The shaft should be lubricated after about fifty hours of use, and the motor about once every two hundred hours of use. Follow the manufacturer's instructions in caring for your motor to assure the best use of it.
Handpiece
The handpiece is the device that snaps into the flexible shaft of the motor and holds the diamond burs. It is held in the hand, somewhat like a pencil, when making the cut. The handpiece is made in various designs for specific purposes, but only the two that are best suited for glass engraving are described here. The first, shown here at the top of the photograph, has "no-oil" sealed bearings and a flexible spring connector. One collet (the part that fits into the chuck and clamps the diamond bur) is furnished with the handpiece; you can purchase separately the other two sizes needed. The three collets we will use are 1/16 inch (1.6 mm), 3/32 inch (2.3 mm), and 1/8 inch (3.17 mm); these are the sizes of the diamond bur shafts. The proper size collet is placed in the chuck, the diamond bur shaft is slipped into the collet, and, when the chuck is tightened, the tool is ready for use.
The handpiece shown at the bottom of the photograph has no chuck or collet; it does have a locking unit that holds the bur securely. It will only accept 3/32 inch (2.3 mm) shafts. Because of its configuration, this handpiece is especially handy for getting at small, hard-to-reach spots. Otherwise, it is structurally the same as the first.
The handpieces shown are equipped with a spring connection of high-quality steel; this provides unrestricted wrist movement and great flexibility. Do not subject this connection to unnecessarily sharp bends or excessive pressure, as damage could result. The same handpieces are available without the spring connection, but I suggest using the former because of their versatility.
Take good care of your tools and they will serve you for a long time. At the close of each work session, remove the chuck and collet, dry with a rag or tissue, put a drop of oil on a rag, and wipe all parts to prevent rust. The second handpiece mentioned is more difficult to clean, but do it anyway! Shake out all water that has accumulated in the nozzle and dry with the corner of a folded rag inserted into the nozzle. Add a drop of oil and repeat the drying process. Always heed the manufacturer's instructions in caring for your equipment.
The Speed Control
To control the cuts, you must be able to control the speed at which the diamond bur revolves. Larger, rougher cuts require a fast speed, while delicate, smooth cuts require a slower speed. The device used to vary the speed is a foot-operated rheostat, located in the electrical circuit between the electric source and the motor. The greater the pressure of your foot, the faster the motor will revolve. The rheostat provides smooth, precise control of motor speeds, and it automatically shuts off the motor when the foot is removed from the pedal. After some experience, you will be able to achieve the desired speed with ease; you will become unconscious of what your foot is doing —it will simply respond to your needs.
Of the two rheostat models shown on this page, I find the one with the dome-shaped top more versatile. You can press on the edge at any point for a reaction. Practice using the control when you begin your engraving exercises, especially the slow speed used in the finishing cut.
Do not expect the rheostat to last for the life of the motor. I have replaced the rheostat twice in the ten years or so that I have used my motor.
Diamond Bur
There are two types of diamond burs; they perform the same job, but differ in their construction. One is made of metal at the cutting point, with industrial-grade diamond dust, called bort, impregnated and metal-plated onto the surface. The other is a sintered type, formed with a bonding material that has the diamond throughout the cutting head, so that, as the diamond is worn away at the surface, there is more to replace it. Both types of diamond points are mounted on steel shafts in sizes of 1/16 inch (1.6 mm), 3/32 inch (2.3 mm), and 1/8 inch (3.17 mm), depending on the size of the cutting point.
Although the sintered type of bur costs a little more, it will last longer than the plated type. Once the diamond is gone on the plated type, there is nothing left but the steel core. I have a collection of both types in my workbox and use both to advantage. I usually use the plated burs for the rough cutting and the sintered burs for the more delicate work because the sintered burs seem to leave a smoother surface. It is not necessary, however, to use both types, since they are available in the same shapes and sizes. Diamond burs cost from about $5 to $18 each, depending on the size and type.
You will need the following diamond burs to begin your glass engraving ventures:
Three rounds in sizes 1 mm, 2 mm, and 4 mm
Two cone shapes in sizes 2 mm and 4 mm at the base
One inverted cone in size 3 or 4 mm
Round-edge wheels in sizes 6 and 10 mm
One tapered cylinder 3 mm at the base
One inverted tapered cylinder of the same size (3 mm)
One 3/4 inch (19 mm) flat saw
One 6 mm flat saw
The saw has diamond on the cutting edge only and is used to make thin line cuts and to help shape glass.
Of course, you will add other burs to your toolbox as you progress because there always seems to be a spot where the burs you have do not quite work. But finding the right bur is the challenge and fun of engraving. Dentist friends have given me slightly worn burs that they no longer can use on teeth. These often work beautifully on glass. It pays to visit your dentist!
Get to know the proper names of the burs, familiarize yourself with the task that each performs, and take care of them. I have some that I have used for several years and they will last several more.
Diamond Pencil
The diamond scriber or "pencil" is used to inscribe the design on the glass as a guide for the engraving. It is also used for engraving various tiny lines and for the stippling technique.
There are two types of diamond scribers. The first is made with a small sliver of uncut industrial-grade diamond set in either a wooden or plastic handle. Since the scriber has a rough, irregular-shaped diamond point, some edges of the diamond will cut small, sharp lines, while others will cut heavier or irregular lines. It is necessary to roll the scriber in your fingers while cutting on a piece of scrap glass to find a suitable cutting edge. Once this cutting point has been located, a mark can be placed on the holder for quick future reference.
The second type of scriber has a diamond that is precision ground to a point of either 60, 70, or 90 degrees and set in a plastic or aluminum holder. Some makers offer a model similar to a writing pen, complete with a clip and retractable point. The apex of the diamond cone in this type is always the cutting point, the advantage being that no matter which way the holder is turned, the point remains in a cutting position. This is the scriber I prefer. I use the one with a 90 degree angle point simply because, with the wider angle, it is the strongest and least likely to be damaged. Should your diamond become chipped or dulled, some manufacturers offer a sharpening service. A good diamond scriber can be purchased for under $10. Although diamond is the hardest substance known, it is brittle and can be chipped and damaged, so use it with a light touch.
Tungsten Carbide Steel Scriber
Used for the same purpose as and similar in appearance to a diamond scriber, the tungsten carbide-tipped scriber is less expensive. The cutting point is made of hardened tungsten carbide steel and is set in a holder of aluminum or plastic. The hard steel shaft protrudes about 3/16 inch (4.8 mm) from the holder. The shaft is about the size of a pencil lead and is shaped at a 30 degree angle to an exceedingly sharp point. Occasionally I use the carbide steel scriber with a straightedge to make long straight lines because the steel point glides smoothly against it without interruption. If the steel point becomes damaged and useless, the only choice is to buy a new one for two or three dollars.
(Continues...)
Excerpted from Engraving Glass by Boyd Graham. Copyright © 1982 Van Nostrand Reinhold Company Inc.. Excerpted by permission of Dover Publications, Inc..
All rights reserved. No part of this excerpt may be reproduced or reprinted without permission in writing from the publisher.
Excerpts are provided by Dial-A-Book Inc. solely for the personal use of visitors to this web site.
Table of Contents
Contents
PREFACE,INTRODUCTION,
1 GLASS ENGRAVING TECHNIQUES AND EQUIPMENT,
2 GETTING STARTED,
3 ENGRAVING FORMS: PROJECTS,
4 CHOOSING GLASS BLANKS AND DESIGNS TO ENGRAVE,
5 ENGRAVING A VASE: DEMONSTRATION,
6 OTHER TECHNIQUES AND TOOLS,
7 DISPLAYING YOUR WORK,
IN CLOSING,
MATERIALS AND WHERE TO OBTAIN THEM,
INDEX,