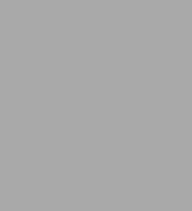
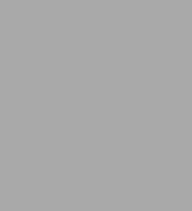
Paperback(Second Edition)
-
PICK UP IN STORECheck Availability at Nearby Stores
Available within 2 business hours
Related collections and offers
Overview
In this comprehensive guide to doubleweave, master-weaver Jennifer Moore revisits the tips and techniques to weaving in multiple layers. Doubleweave Revised & Expanded is filled with new information about doubleweaving and more including:
• More doubleweave technique samples for both 4 and 8-shaft looms, including more overshot patterns.
• Expanded information on how to weave fabric twice, thrice or even four-times the width of your loom, with no seam.
• Beautiful doubleweave project patterns for the home and more!
Expand the abilities of your loom with Doubleweave Revised & Expanded!
Product Details
ISBN-13: | 9781632506443 |
---|---|
Publisher: | Penguin Publishing Group |
Publication date: | 01/15/2019 |
Series: | The Weaver's Studio |
Edition description: | Second Edition |
Pages: | 176 |
Sales rank: | 348,183 |
Product dimensions: | 8.40(w) x 8.70(h) x 0.60(d) |
Read an Excerpt
CHAPTER 1
THE BASICS OF DOUBLEWEAVE
Doubleweave is the weaving of two layers of cloth on the loom at the same time, one above the other. These layers may be completely independent of each other, they may be connected on one or both selvedges, or the two layers may be interwoven through loom-controlled or hand-manipulated layer exchange.
Doubleweave has the reputation of being a difficult weave structure, one that you should only attempt if you're a fairly experienced weaver. This is really quite unfounded — doubleweave is much easier to do than it is to talk about. I've worked out a system of drafting and setting up doubleweave that makes it easy to see what's happening in the cloth by simply looking at the threading and tie-up. All of the parts work together, from the layout of the treadles to the direction in which your shuttles weave. This makes it easy to understand and helps minimize mistakes.
HOW DOUBLEWEAVE WORKS
Imagine that you have a four-shaft loom and you saw it in half. You now have two looms, each of which has two shafts and each of which holds half of the treadles. Each of your looms has the capability of weaving a plain-weave cloth, as well as plain weave's variations such as basket-weave and rep weave. That's essentially what we're going to do, but instead of doing it with a saw, we're going to do it by manipulating threading and tie-up.
I'm going to start with a very simple warp, in which one layer is light and the other layer is dark, so that you can clearly see the contrast between the two layers. Other than being different colors, the two warp yarns are identical, which means that the warp threads can be wound together on one beam, as though they were all just one warp, with light and dark threads alternating.
In the conventional method of setting up doubleweave (FIGURE 1), you would thread the heddles in the following manner: light on shaft 1, dark on 2, light on 3, dark on 4, in a straight twill threading. The reason for threading in this way is that it's simple and easy to remember, and the warp threads for each layer are evenly distributed among the shafts. This is all well and good. However, it's difficult to conceptualize the light and dark layers as being separate from each other when they're interspersed on the loom, and it's difficult to see in the draft how they are separate from each other as well.
To deal with this, we'll switch shafts 2 and 3, and thread light on 1, dark on 3, light on 2, dark on 4. This threading is really no more difficult to remember; the warp threads are still evenly distributed, and the end result is identical. But you can now see the light and dark layers as being separate from each other, both on the loom and in the draft (FIGURE 2).
If you look at only the bottom half of the draft, you can see that the light warp threads are threaded alternately on shafts 1 and 2, in plain-weave fashion. And in the tie-up, there's one treadle that lifts each of that layer's shafts individually, as well as one that lifts the entire layer. Likewise, if you look at only the top half of the draft, you can see that the dark warp threads are threaded alternately on shafts 3 and 4, in plain-weave fashion. And in the tie-up, there's a treadle that lifts each of that layer's shafts individually, as well as one that lifts the entire layer. So here we have (theoretically) our two looms, each of which is capable of weaving a plain-weave cloth, one on shafts 1 and 2 with light threads, and one on shafts 3 and 4 with dark threads.
Let's look a little more at the tie-up for doubleweave. All of the treadles for the light layer are on the left side of the loom and the left foot is going to operate these treadles. All of the treadles for the dark layer are on the right side of the loom and the right foot is going to operate these treadles. So with both feet in the center of the loom, in "home" position, if you treadle with your left foot, all of the light layer is lifted, and if you treadle with your right foot, all of the dark layer is lifted. Then on either side of the center, each foot has treadles to operate the individual plain-weave shafts for its layer.
Instead of thinking of these as treadles 1 through 6, think of them as two separate sets of treadles, one for the left foot and one for the right foot. The left foot has a center treadle that lifts all of its layer, plus a pair of pattern treadles, one on the left (1) and one on the right (2). The right foot has a center treadle that lifts all of its layer, plus a pair of pattern treadles, one on the left (3) and one on the right (4).
For some sheds, two treadles will be used at the same time — a center treadle with one foot combined with a single pattern treadle with the other foot. Depending on which structure you're weaving, it's also possible to create a tie-up that gives you all of the combinations using one treadle at a time if you have enough treadles, as discussed in the sidebar on page 15.
How to Weave Two Separate Layers
So how are two cloths actually woven, one above the other, at the same time? Imagine lifting only shaft 1 and weaving with a light-colored weft, then lifting shaft 2 and returning with the same light-colored weft, and repeating these two steps over and over. You would have a light-colored plain-weave cloth with unwoven dark warp threads floating underneath. This is how the light layer on top is woven.
But how do you weave the dark layer on the bottom?
Imagine lifting the entire light-colored layer (shafts 1 and 2) just to get it out of the way. Then in addition to that, lift shaft 3 and weave with the dark weft, then lift shaft 4 and return with the dark weft, and repeat these two steps over and over. The result is a dark plain-weave cloth, with unwoven light threads floating above it.
To weave the bottom layer, the entire top layer must be lifted up out of the way; then the individual shafts for the bottom layer are lifted in turn as you weave that layer.
This is the crux of doubleweave. If you can understand this, you know most of what you need to know about how doubleweave works. Everything else is really just elaboration on this idea.
To weave both cloths at the same time, you'll put these steps together and alternate weaving a row of the top layer, then a row of the bottom layer. Let's look at these steps in the draft. Instead of using a drawdown, as we would for single-layer cloth, we're going to use a cross-section drawing, as though we had cut through the cloth and were looking at the cut warp ends (FIGURE 3).
Notice that in step 1, you're lifting shaft 1 with the left treadle of the two light layer's plain-weave treadles, and you're starting the shuttle with light-colored weft from the left. In step 2, you're lifting shafts 1 and 2 to get them up out of the way, plus shaft 3, which is done with the left treadle of the two dark layer's plain-weave treadles, and you're starting the dark shuttle from the left. In step 3, you're lifting shaft 2, which is done with the right treadle of the two light layer's plain-weave treadles, and you're starting the light shuttle from the right. In step 4, you're lifting shafts 1 and 2 to get them up out of the way, plus shaft 4, which is done with the right treadle of the two dark layer's plain-weave treadles, and you're starting the dark shuttle from the right.
The color and position of the shuttles matches the color and position of the plain-weave treadles. This will help you keep track of where you are in the sequence. If both shuttles are on the left, you must be ready to start step 1. If both shuttles are on the right, you must be ready to start step 3. If the shuttles are on opposite sides, look to see which color your last pick was. You're ready to weave with the opposite color, starting with the plain-weave treadle for the layer that's on the same side as the shuttle.
When you finish this sequence, you've gone back and forth on both layers and completed the plain-weave sequence for both layers. Both shuttles are back on the left, ready to begin the sequence again. This sequence of four steps is one complete unit of two separate layers with the light color on top.
Notice also that in steps 1 and 3, you're lifting a single shaft. Those single numbers, 1 and 2, refer to the top layer. In steps 2 and 4, you're lifting three shafts at a time, two from the top layer to get them up out of the way, and one of the plain-weave treadles for the bottom layer. When you look at the steps and see a single number, you know you're on the top layer. And when you see three numbers, you know you're on the bottom layer.
This all took a long time and a lot of words to say, but to sit down and weave these four steps takes less than a minute. Now that we've taken a detailed look at the basic four-shaft draft and the four basic steps of weaving doubleweave, it's time to move on to weaving a sampler with this and many more techniques using the basic four-shaft draft. But first, let's take a look at some general considerations for planning and setting up a doubleweave warp.
CHAPTER 2PLANNING AND SETTING UP
We all evolve our own systems for warping a loom based on what we were taught, what type of loom we have, what we weave, and our own personal preferences. There's no right or wrong way to warp a loom, as long as the warp ends up correctly threaded and sleyed, without tangles or twists, under perfectly even tension.
The system that follows is the one that works for me. Follow this in its entirety, pick and choose parts that you like, or use your own system. The instructions are specific for the four-shaft sampler but also serve as general instructions for any doubleweave warp. This chapter does not include basic instructions on winding a warp and setting up a loom; if you need help with this, there are many good resource books, or ask a weaving friend or teacher to guide you.
YARN CONSIDERATIONS
You'll be weaving two layers of cloth at the same time, so the total sett will be twice what it would be for a single layer. This means that you'll be winding on a very dense warp, and the warp will be closely sett in the reed. It's particularly important to get good, clean sheds in doubleweave because you don't want to accidentally catch warp threads from one layer in the other layer, so be sure to weave with tight warp tension.
Your warp yarn can be any type of fiber — wool, cotton, linen, silk, whatever you like — but it is important that the yarn be very strong and fairly smooth. Apply the "break test" to a yarn that you're thinking about using for your warp: If you can break it easily with your hands, it's probably not strong enough to use for a doubleweave warp. And if your yarn is very fuzzy or has lots of texture, such as mohair or a bouclé, you'll probably have problems with warp yarns sticking together and being unwilling to separate easily into sheds.
For many of the samples and projects in this book, I use 5/2 pearl cotton for the warp yarn. Pearl cotton has all of the qualities that I want for this purpose; it's strong and smooth, it's readily available in a wide range of colors, and it's reasonably priced. The 5/2 size is a comfortable scale to work with, is easy to see for threading and pick-up work, and allows clear differentiation of layers.
WARP PLANNING
For a basic two-layered cloth in which the warp yarn is the same for each layer except for the color, the easiest approach is to think in terms of a single layer when planning and making warp calculations. The amount of yarn that you need for a single layer is the same amount that you'll need for your second layer.
Using 5/2 pearl cotton, you'll work with a sett of 16 ends per inch (epi) for each layer, for a total of 32 epi (one inch equals 2.5 centimeters). In calculating the length of the warp, add in the usual loom waste and take-up and shrinkage appropriate for the yarn you're using. A 3 yd (2.75 m) warp is ample for weaving the sampler, with a little extra for experimentation. You'll have 144 warp ends in each layer, or a total of 288 warp ends for the sampler, which is 9 inches (23 cm) wide.
WINDING THE WARP
Once you know how many warp ends you need for each layer and the length of your warp, you're ready to start winding the warp. Measure a guide thread the length of your warp and attach it to the warping board or warping reel in the path your warp will take. Have a cone of yarn ready for each of your two layers. Put the ends of the two colors together and attach them with a slipknot to the bottom end peg opposite the end where you'll have your cross.
Wind the two threads at the same time, keeping a finger between them to keep them from twisting together (FIGURE 1). This means you'll have a pair of threads, light and dark, in each section of the cross (FIGURE 2). Count only the number of warp threads that you need for a single layer, since you're winding the two together as one. Rather than having to count the total number of warp threads, I prefer to count the number of threads in a 1inch (2.5 cm) section and then tie each of these groups tightly into a bundle at the top end peg. This way I only have to count to 16 for each 1-inch (2.5 cm) group (FIGURE 3).
Tie off your cross and make choke ties in the usual way. Cut the ends of your warp at the opposite end peg from your cross. When chaining the warp to remove it from the warping board or reel, alternate using your left and right hands to pull each section through the loop; this avoids adding extra twists to your warp (FIGURE 4).
WINDING THE WARP ONTO THE LOOM
I wind doubleweave warps onto my loom from back to front — that is, I wind onto the warp beam before threading the heddles and sleying the reed. My warps wind on smoothly this way, and I don't run into problems with twists or uneven tension. When students arrive at my workshops with badly twisted warps or tension problems, they've usually wound on from front to back. If that's the method that you're comfortable with, be extra careful that you aren't adding twists to your warp.
Attach the warp to the warp beam according to the system on your loom. Place lease sticks in the cross and distribute the warp in a raddle to control the warp spacing as you wind it onto the warp beam. If you've already tied off 1inch (2.5 cm) groups of warp threads on your warping board and you have a raddle with 1-inch (2.5 cm) sections, then your tied sections are already counted and ready to go onto the raddle.
Because the warp is sett twice as densely as for a single layer of balanced plain weave, it tends to tangle more in the lease sticks, and winding on is a slower process. Take your time. Wind on a little bit at a time, and when the warp starts to bunch up in the lease sticks, stop and work out tangles by strumming on the warp. You'll want to wind on with firm tension. If you're working with a helper, one of you can pull firmly on the warp while the other winds on. If you're working alone, wind on no more than one rotation of your warp beam, then stop, work out the tangles, and pull firmly on the warp to tighten up the last rotation before proceeding to wind on some more.
THREADING THE HEDDLES
Because of the dense sett for doubleweave, you may find that you use more heddles than you usually do. Before starting a project, check to make sure that you have enough heddles on all your shafts. For the basic four-shaft doubleweave draft, an equal number of heddles is needed for each shaft.
Prop up your shafts to bring them closer to eye level. Remove the reed and beater cap from your loom, as well as the breast beam, if possible. Anything you can do to allow yourself to be close to the heddles and at eye level with them will help make the job of threading more comfortable and relaxing.
I like to pull out a group of 16 heddles — four from each shaft — at a time. From this group, separate out one heddle from each of the shafts. You can also just pull out four heddles at a time, one from each shaft. From this group, pull out two heddles, either from shafts 1 and 3, or from 2 and 4, following the threading plan. With your left hand, pull out a pair of threads from the cross in the lease sticks. Use your index finger to separate the two threads, and then thread the light thread on the front shaft and the dark thread on the back shaft (FIGURE 5). This process becomes quite fast and easy with practice.
(Continues…)
Excerpted from "The Weaver's Studio Doubleweave Revised & Expanded"
by .
Copyright © 2018 Jennifer Moore.
Excerpted by permission of F+W Media, Inc..
All rights reserved. No part of this excerpt may be reproduced or reprinted without permission in writing from the publisher.
Excerpts are provided by Dial-A-Book Inc. solely for the personal use of visitors to this web site.
Table of Contents
INTRODUCTION,
CHAPTER ONE: The Basics of Doubleweave,
CHAPTER TWO: Planning and Setting Up,
CHAPTER THREE: The Four-Shaft Sampler,
PROJECT: Four-Shaft Sampler,
CHAPTER FOUR: Doubleweave Pick-Up,
PROJECT: Graphed Sampler,
CHAPTER FIVE: More Four-Shaft Possibilities,
PROJECT: Log Cabin Tubular Pillows,
PROJECT: Doublewidth Log Cabin Blanket,
PROJECT: Double Rainbow Sampler,
PROJECT: Sun, Moon, and Stars Runner,
CHAPTER SIX: Eight-Shaft Exploration,
PROJECT: Reversible Self-Lined Drawstring Pouch,
PROJECT: Triplewidth Tablecloth with Spot Bronson Center Panel,
PROJECT: Eight-Shaft, Two-Block Sampler,
PROJECT: Autumn Windows Runner,
PROJECT: Double-Block Placemats,
PROJECT: Square Dance Mat,
FINAL THOUGHTS,
BIBLIOGRAPHY,