5
1
9781932159349
$54.95
Current price is , Original price is $54.95. You
Class A ERP Implementation: Integrating Lean and Six Sigma available in Hardcover
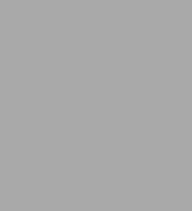
Class A ERP Implementation: Integrating Lean and Six Sigma
by Donald Sheldon
Donald Sheldon
- ISBN-10:
- 1932159347
- ISBN-13:
- 9781932159349
- Pub. Date:
- 05/01/2005
- Publisher:
- Ross, J. Publishing, Incorporated
- ISBN-10:
- 1932159347
- ISBN-13:
- 9781932159349
- Pub. Date:
- 05/01/2005
- Publisher:
- Ross, J. Publishing, Incorporated
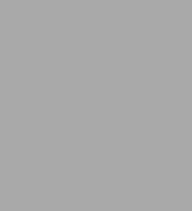
Class A ERP Implementation: Integrating Lean and Six Sigma
by Donald Sheldon
Donald Sheldon
Hardcover
Buy New
$54.95
$54.95
54.95
In Stock
Overview
Class A ERP is often misunderstood and confused with software tools and implementations but is actually a management system for continuous improvement. This book will resolve these myths by thoroughly describing the definition of Class A ERP and giving specifics for achieving Class A performance in a reasonable timeframe. Examples from successes will be referenced to and the author will build a case for breaking the journey to world-class performance into bite-sized, doable focus areas. Class A ERP Implementation will help organizations set the stage for maximum effectiveness of both Lean strategies and Six Sigma and establish ERP disciplines as the prerequisite to success.
Product Details
ISBN-13: | 9781932159349 |
---|---|
Publisher: | Ross, J. Publishing, Incorporated |
Publication date: | 05/01/2005 |
Pages: | 304 |
Product dimensions: | 6.00(w) x 9.00(h) x 0.90(d) |
About the Author
Donald H. Sheldon is president of DH Sheldon & Associates, an international consulting firm headquartered in New York. As a practitioner, this leading expert previously served as Director and General Manager of The Raymond Corporation's Worldwide Aftermarket Services Division and as Vice President of Global Quality and Six Sigma Services for the NCR Corporation. Prior to forming his own firm, Mr. Sheldon was Vice President for BUKER, Inc, of Chicago, a world-recognized leader in management education and consulting. He has been published in numerous magazines and journals and is author of the book Achieving Inventory Accuracy and was co-author of The Road to Class A Manufacturing Resource Planning (MPR II). He has been a frequent speaker at colleges, international conventions and seminars and he is certified by APICS as CFPIM (Certified Fellow in Production and Inventory Management) and as CIRM (Certified in Resource Management).
Table of Contents
Preface | xi | |
About the Author | xiii | |
Acknowledgments | xv | |
About APICS | xvii | |
Web Added Value | xix | |
Chapter 1 | What Is ERP? | 1 |
Top-Management Planning | 2 | |
Master Production Scheduling and Materials Management | 4 | |
Data Accuracy | 7 | |
Bill of Material Accuracy | 7 | |
Inventory Balance Accuracy | 8 | |
Integration with Lean and Six Sigma | 10 | |
ERP as the Starting Point | 12 | |
Chapter 2 | Class A ERP Performance | 17 |
Material Requirements Planning | 17 | |
Manufacturing Resource Planning | 18 | |
The Class A ERP Standard of Today | 24 | |
Class A ERP Certification | 27 | |
Summary | 31 | |
Chapter 3 | Business Planning | 33 |
Business Imperatives | 36 | |
Top-Level Management Systems | 37 | |
Tricks in Building the Right Business Plan | 38 | |
Financial Objectives Planning | 38 | |
Internal Business Process | 40 | |
Learning and Growth | 42 | |
Customer Influences on Business Imperative Choices | 44 | |
Supply Chain Influences on Business Imperative Choices | 45 | |
Technology Affecting Business Imperative Decisions | 46 | |
How Many Business Imperatives Should You End Up With? | 47 | |
Linking the Financial Plans with the S&OP Process | 48 | |
Product Planning in Class A ERP | 49 | |
The Class A Measurement for Business Planning | 49 | |
Talent Review | 51 | |
Process Ownership of the Business Plan | 52 | |
Summary | 52 | |
Chapter 4 | Sales and Marketing Planning: Creating the Demand Plan | 55 |
Business Planning as an Input to Demand Planning | 56 | |
Marketing Plans as an Input to Demand Planning | 57 | |
Sales Planning as an Input to Demand Planning | 59 | |
Historical Inputs to the Demand Planning Process | 61 | |
Understanding the Outputs of Demand Planning | 62 | |
The Weekly Demand Review | 62 | |
Process Ownership in the Demand Plan | 65 | |
The Measurement Process for the Class A Demand Plan | 66 | |
Chapter 5 | Operations Planning | 71 |
Product Families | 74 | |
Elements of Operations Planning | 76 | |
Chapter 6 | Sales and Operations Planning | 87 |
Participants to the S&OP and Their Roles in Larger Multiplant Environment | 89 | |
Some Thoughts on Alternative Labels for S&OP | 91 | |
Roles in the S&OP Meeting | 91 | |
Timing for the S&OP Process and the "Monthly Closing of the Books" | 94 | |
Agenda for the Pre-S&OP | 96 | |
The Spreadsheets for Both the Pre-S&OP and the S&OP Processes | 98 | |
Summary: Keys to the Success of the S&OP Process | 99 | |
Chapter 7 | Master Scheduling | 103 |
The Master Production Schedule | 103 | |
Capacity Planning in the Master Production Schedule | 108 | |
Rules for Level Loading | 114 | |
Linking to the Operations Plan | 115 | |
Master Scheduler's Role | 119 | |
Master Scheduling Metrics | 121 | |
Management Systems Requirements | 123 | |
Process Ownership | 125 | |
Chapter 8 | Class A ERP Material Planning | 127 |
Order Policy Decisions | 129 | |
ABC Stratification | 131 | |
Process Ownership in Material Planning | 131 | |
Material Planning Metrics | 132 | |
Integration with Lean and Six Sigma | 132 | |
Running the Net-Change Calculation | 134 | |
Inventory Management | 136 | |
Chapter 9 | Class A ERP Data Accuracy Requirements | 139 |
Inventory Location Balance Accuracy | 139 | |
Inventory as an Asset | 140 | |
Allowing the Elimination of Buffer Inventory | 140 | |
Control Groups | 141 | |
Physical Inventory | 148 | |
Eliminating the Physical Inventory Forever | 148 | |
Process Owner of Inventory Accuracy | 149 | |
Inventory Accuracy Metrics | 150 | |
Bill of Material and Routing Record Accuracy | 151 | |
Summary | 158 | |
Chapter 10 | Class A ERP Procurement Process | 159 |
Why Develop Partnerships with Suppliers? | 161 | |
Selecting Suppliers for Partnerships | 162 | |
Implementing Supplier Partnerships | 165 | |
Aligning the Sales and Operations Planning Processes | 167 | |
Information Sharing | 168 | |
A Word About Reverse Auctions | 168 | |
Logistics as a Competitive Advantage | 169 | |
Supplier Performance Ratings and Certification | 170 | |
Integration of Lean and Six Sigma in Procurement | 172 | |
Process Ownership in Procurement | 172 | |
Class A Metrics in Procurement | 173 | |
Chapter 11 | Shop Floor Control | 175 |
Communicating the Schedule to the Factory | 177 | |
The Role of Material Requirements Planning | 179 | |
Functional Manufacturing Versus Process Flow | 180 | |
Dealing with the Word "Can't" | 183 | |
Setup/Changeover Reduction | 184 | |
Customer-Focused Six Sigma Quality | 186 | |
Employee Involvement | 188 | |
Team Planning and Management | 189 | |
Kaizen Events on the Factory Floor | 192 | |
Areas of Waste | 194 | |
5-S Housekeeping and Workplace Organization | 195 | |
Simple Problem-Solving Tools | 196 | |
Process Owners for Shop Floor Control | 197 | |
The Metrics in Shop Floor Control | 198 | |
First-Time Quality | 199 | |
Safety | 200 | |
Chapter 12 | Customer Service | 201 |
Rules of Engagement | 203 | |
Customer Service Exceptions | 204 | |
Deliver on Time or Ship on Time | 204 | |
Process Ownership for Customer Service | 205 | |
The Metric for Customer Service | 206 | |
Shipping Ahead of the Promise Date | 206 | |
Chapter 13 | Class A ERP Project Management/Six Sigma Process Integration | 207 |
Class A Project Management | 208 | |
Lean-Focused Project Management | 209 | |
Six Sigma-Focused Project Management | 212 | |
Defects | 215 | |
Project Management Structure | 215 | |
Chapter 14 | Class A ERP Management System | 219 |
Weekly Performance Review | 220 | |
Clear-to-Build | 224 | |
Weekly Project Review | 224 | |
Daily Management System Events | 224 | |
Other Management Systems in the Business | 229 | |
Chapter 15 | Education and Training | 231 |
Class A ERP Education | 231 | |
Training Requirements | 234 | |
DVD Education for ERP | 243 | |
Chapter 16 | Class A ERP Performance Metrics | 245 |
Barometric and Diagnostic Measures | 245 | |
Starting the Metric Process in Class A | 249 | |
Weekly Performance Review | 250 | |
Posting the Metrics | 250 | |
Chapter 17 | A Word About ERP Software | 253 |
Chapter 18 | Class A ERP Implementation | 257 |
Steps for Successful Class A ERP Implementation | 257 | |
Summary | 265 | |
Chapter 19 | Class A ERP Integration with Lean and Six Sigma | 267 |
Best-in-Class Lean | 267 | |
Lean Tools | 271 | |
Customer-Focused Quality (Six Sigma) | 273 | |
Other Six Sigma Tools | 278 | |
Chapter 20 | The Role of Consultants in Class A ERP | 281 |
Payback | 282 | |
Appendix A | Summary of Class A ERP Certification Criteria | 285 |
Appendix B | Steps for Successful Class A ERP Implementation | 292 |
Index | 293 |
From the B&N Reads Blog
Page 1 of