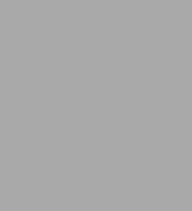
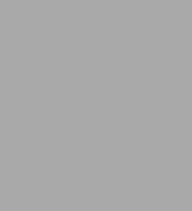
eBook
Related collections and offers
Overview
Punches and chisels
Traditional candlestick
Door latches and bolts
Garden tools
Weather vanes
Fences and railings
Tables
Wheelbarrow
... and many more! A book of ideas and suggestions, rather than an instruction manual on blacksmithing techniques, this volume features eighty detailed figures and diagrams. It also includes lists of materials, step-by-step instructions, and suggestions for variations in design.
Product Details
ISBN-13: | 9780486319100 |
---|---|
Publisher: | Dover Publications |
Publication date: | 03/12/2013 |
Series: | Dover Crafts: Jewelry Making & Metal Wor |
Sold by: | Barnes & Noble |
Format: | eBook |
Pages: | 144 |
Sales rank: | 550,765 |
File size: | 8 MB |
Read an Excerpt
Blacksmithing Projects
By Percy W. Blandford
Dover Publications, Inc.
Copyright © 1988 Percy W. BlandfordAll rights reserved.
ISBN: 978-0-486-31910-0
CHAPTER 1
Set of Punches and Chisels
A metalworker, whatever the particular branch of metalwork that interests him or her, needs a variety of punches and chisels. It might seem that there is never a large enough variety, that there are always different sizes and shapes that would suit a particular job better. Some of these tools also have uses, as they are or slightly modified, in working wood, leather, stone, and other materials. The blacksmith is able to make all these tools for his own or other craftsmen's use, even if his equipment is not as comprehensive as he would like. It should be possible to make most of the tools in this project with only a propane torch as a source of heat and an iron block as an anvil.
The material is high-carbon steel, which may be round, square, octagonal, hexagonal, or almost any other rod section. It need not be new and can be salvaged from discarded tools, springs, and similar things. Some commercially produced punches and chisels are made from special alloy steels. They need precise heat treatment unavailable to most individual blacksmiths, so these steels are better avoided. Ordinary high-carbon steel can be hardened and tempered satisfactorily with simple equipment.
A few punches, but not cutting tools, can be made from mild steel, which cannot be hardened and tempered, because it is unaffected by cooling in water. Remember not to do this with high-carbon steel; cooling in this way not only hardens it, but makes it brittle. Until you intentionally harden the steel it should be allowed to cool slowly.
Although short pieces of rod can be held with tongs, it is always easier to work on the end of a long rod, which can be held and then cut off. Where possible, do not cut the steel to length until after shaping its end.
If you wish to make something from high-carbon steel that has previously formed something else, it is advisable to anneal it to remove its temper and make it as soft and ductile as possible before reforging it. This is done by heating to redness and allowing to cool as slowly as possible. Leaving it in a fire overnight to cool is a good way of achieving ultimate softness.
A simple project is a center punch (Fig. 1-1A). Use rod of any section about ½ inch across. Draw down the end to about 1/8-inch diameter (Fig. 1-1B). Cut off to 5 inches long, and either forge or grind the top with a bevel all round (Fig. 1-1C) to minimize spreading when being hammered.
File or grind the tapered part to a bright finish. Finishing with emery or other abrasive cloth can follow, because the better the surface polish, the easier it is to see oxide colors when tempering.
Start from the end and heat about 1 inch to redness. Hold with tongs and plunge vertically into water (Fig. 1-1D). Be careful not to let the steel go in at an angle, which might cause cracking. Brighten the end again with abrasive cloth. This could not be done if it had not been previously polished; because the point would be very hard and brittle.
To temper, use a propane torch (Fig. 1-1E) or similar flame and heat between 1 and 2 inches from the point. Watch the spread of oxide colors towards the point. Heat will continue to spread, even when you take the flame away. The slower the heat, the greater the widths of the oxide colors, and the greater the width of steel at a particular temperature. The first color to reach the end will be a pale straw, which will deepen. When it has passed through dark straw to brown, plunge the point vertically into water. That should give a suitable hardness for a center punch.
An alternative method requires quicker action, but with only one heating. Have the tapered part bright and heat to redness as before, but only plunge a short distance into water. While the steel is still hot higher up, brighten the last inch and watch the spread of colors from the hot part. When you get the correct color, quench the steel completely.
If you let the colors go too far with either method, return to hardening before trying to tempter again. Most high-carbon steels can be hardened and tempered in water at room temperature. Some are intended to be quenched in brine (saturated salt solution) and some in oil. If you buy new steel, the supplier will indicate what to use. If you are re-using steel, and water causes the steel of a test piece to crack, use one of the other liquids.
For general purposes, grind the punch point to 60º (Fig. 1-1F). If the punch is intended to pierce sheet metal, as in traditional tinwork, the point may be 30º or up to 45º. For heavy work with a large punch, or for regularly locating the centers for drilling holes, an angle nearer 90º may be used.
Several center punches of different bulk and with different sizes and angles of points can be made. A fine punch with a long taper and small point forms a dot punch for locating spots (Fig. 1-1G). It could also be used for tinplate punching. A stone mason uses a rather longer center punch (Fig. 1-1H). A punch taken to a needle point (Fig. 1-1J) is used for piercing paper or leather. If fitted into a handle it becomes an awl. It could also be used as a scriber.
Punches for setting nails are made like center punches, but with ends square across (Fig. 1-1K). They could be hollowed by driving onto a ball bearing while hot (Fig. 1-1L). Make several, with ends from inch upwards. High-carbon steel is advisable, but a nail punch of mild steel should have a reasonably long life.
You can make drifts like nail punches, but they will be longer and have a more gradual taper (Fig. 1-1M) for pushing through holes that should match and pulling them into line.
Chisels can be made almost like punches, using similar tempering colors. The sections of steel used will depend on the intended width of cutting edge. For light work you can use 3/8-inch rod, but ¾ inch or more is stronger and gives a better grip for heavy work. Length should be sufficient to get your hand around without hitting it; 6 or 8 inches would be suitable.
A cold chisel is used for cutting cold metals, and a hot chisel is used for hot metals. The only difference is that its cutting angle is more acute.
A general-purpose chisel from ¼ to ¾ inch wide can be made by drawing down the end of a rod (Fig. 1-2A). If the cutting edge is to be wider than the body of the chisel, upset the end first. How much you upset depends on the final width (Fig. 1-2B). A cape chisel has a crosscutting form (Fig. 1-2C). Forge and file or grind this narrower behind the cutting edge so it does not bind when cutting grooves. Another type for cutting grooves with curved section is made something like a punch (Fig. 1-2D), but with a flat top surface and a cutting edge sloping to the curved side (Fig. 1-2E). For cutting corrugated sheeting or through other curves, the end of a chisel may be shaped (Fig. 1-2F).
With all chisels, brighten the ends for at least 1 inch so the tempering colors can be seen. Temper to about the same oxide color as punches. Do not grind the cutting edges until after tempering. For general purposes the edge of a cold chisel could be 60º (Fig. 1-2G), for regular use on soft metals it could be slightly less. The edge of a hot chisel may be 45º (Fig. 1-2H) or less. It is the contained angle that matters. For some purposes there might be more slope on one side than the other (Fig. 1-2J).
CHAPTER 2Wood-Cutting Tools
A large range of tools to cut wood, leather, and fabrics can be forged from high-carbon steel. Those that cut on their ends may be hardened and tempered in a similar way to the punches in the previous project. This type of heat treatment is suitable for ends up to about 1 inch across. For wider ends or knives, which have longer cutting edges, more complicated methods of heat treatment are advisable if an even temper at the edge is to be obtained.
A carpenter's simple marking knife has a cutting edge at one end and a point for use as an awl or scriber at the other end (Fig 2-1A). Rod 5/6-inch -or 3/8-inch diameter is suitable. It would be possible to draw down the end to make a blade about twice as wide as the rod diameter by hammering directly, but it is better to upset the end first and make a wider blade. Cut and draw down the pointed end. In both cases do not go down to too thin a section. Hardening and tempering will be better if you leave a little for grinding to a cutting edge. Brighten both ends with as good a polish as you can get, then harden and temper each end separately. A brown oxide color should be right for the cutting ends. The idea is to leave the center part softer and tougher. Grind and hone both ends.
As a variation, use square rod and twist the center (Fig. 2-1B) for decoration and to provide a grip. In another variation, make the blade with a double angle (Fig. 2-1C).
A marking knife without an awl can be made from flat stock, that is drilled to take wood slabs as a handle (Fig. 2-1D). Steel 1/8-by-¾-inch section is suitable. Spread the end to make a wider blade. With the steel in a fully annealed state, drill two 3/32-inch (or larger) holes for rivets. Harden and temper the end to a brown color.
The rivets could be a soft metal, such as copper. Drill the wood slabs slightly undersize and lightly countersink the holes (Fig. 2-1E). Cut the wire to extend far enough to allow spreading into the countersinks. Rivet a little from each side in turn, with the handle supported on the anvil. Finally, file rivet heads and wood level. For further strength in the joints, put epoxy glue between the wood and metal before rivetting.
Wood chisels not intended to be hit, or to only be hit occasionally and lightly, may be made in a similar way to marking knives. Chisels smaller than those available from tool stores and with ends specially shaped will be welcome for carving and modelmaking. Chisels could be made from flat stock and given wood slab handles, but they are more convenient to use if they have tangs to fit into the more usual round handles. If you cannot make the handles, you can use file handles or pieces of dowel rod.
On each chisel draw down a tang to go into the handle—a length of 2 inches will be about right (Fig. 2-1F). At the other end grind towards the cutting edge, but leave a little thickness (Fig. 2-1G). The working end of the chisel should be smooth, particularly on the underside, so it can be honed to a good cutting edge. If you start with bright-drawn steel there will not have to be much smoothing, but otherwise, grind, file, and polish at least 2 inches from the end. Temper to a brown oxide color.
Chisels of this type can be made from 1/16 inch square up to about 3/8 inch square. For greater widths the stock need not be as thick. For instance, a ½-inch chisel need not be more than ¼ inch thick. For wider chisels, reduce the width of the tang (Fig. 2-1H). For greater strength, square the shoulder at the tang, so the ferrule on the handle can be notched to engage with it (Fig. 2-1J). The end of a chisel does not have to be sharpened straight across. It could be skew (Fig. 2-1K) either way, for carving. It could have a diamond point (Fig. 2-1L). There could be a bevel both sides for woodturning (Fig. 2-1M). Another woodturning tool has a stiff section, and is given an obtuse scraping angle for faceplate turning. Several such tools, with ends square and with different curves (Fig. 2-1N), will be useful to a bowl turner.
When tempering wider sections, keep the spread of oxide colors even by fanning the flame, around the body of the metal. Try to get the bands of color spreading parallel to the ends to achieve an even hardness there.
A carver might want the end of a chisel bent, because sometimes he pulls the tool to cut. A plain tang driven into a hole in wood might not offer much resistance to being pulled out. For these or any other pulling tool, cut teeth in the tang with a cold chisel (Fig. 2-1P).
If a chisel is intended for regular use with a hammer or mallet, a simple tang into a wood handle is not good enough because it would drive in further and split the wood. A chisel could be made without a handle (Fig. 2-2A), or it could have a slab handle (Fig. 2-2B). In both cases the steel takes the blow. A wood handle might go into a socket (Fig. 2-2C), but that is difficult to make. The alternative is a shoulder or bolster on the chisel to prevent it from going further into the handle (Fig. 2-2D).
Whether you can make chisels with bolsters or not depends on your skill and equipment. The tang part can be upset far enough back to form a bolster (Fig. 2-2E), then the tang drawn down (Fig. 2-2F). Another way is to forge the neck of the tang round and weld on a piece of thick-walled tube or drilled rod (Fig. 2-2G). In any case, you will have to finally shape the bolster with a file.
In general woodwork, gouges are not used as often as chisels. However, a turner needs gouges, and a carver's kit of tools might include 100 gouges.
Making a long gouge of even section by hand is difficult, involving careful work with fuller and swage (Fig. 2-2H). Fortunately, a smooth inner surface for a great length is not so important, but the outside should be ground smooth.
For carving, many gouges have wider cutting ends (Fig. 2-2J). These spade gouges can be made in two ways. You can start with a rod and upset the end before spreading and curving it (Fig. 2-2K), then make a tang at the other end. The other way is to start with wider flat stock and reduce the neck. This will also lengthen it and you can finish with a tang (Fig. 2-2L). In both cases the tang should be square to prevent twisting, but at least part of the neck should be round (Fig. 2-2M).
Some spade tools have the neck or blade curved in the length—either up or down—and there might even be a double bend. Within each width a carver needs gouges of many different curves. The range of gouge shapes now available from commercial sources has been reduced considerably; this is where a blacksmith can step in.
Of the sources of high-carbon steel for re-use, old files seem an obvious choice for making chisels. However, care is needed. Files are sold almost fully hard, which means they are brittle. Do not be tempted to merely grind off the teeth and sharpen the end. When trying to use a file as a wood chisel, the edge would quickly crumble and if hit hard the tool might break, possibly with hazardous consequences. Before you make a chisel or anything else from an old file, anneal it, then harden and temper later to the condition that suits its use.
CHAPTER 3Garden Tools
Most hand tools needed in the garden can be made by a blacksmith, but some of the larger ones, such as spades and forks, would be difficult to make unless you have more advanced equipment than usually possessed by a smith. This leaves a large range of other tools, including some that could not be bought.
There is some sheet metalwork and a few joints that are better brazed than welded, but otherwise the work is straightforward forging of mostly fairly light sections. Mild steel can be used throughout, although high-carbon steel might be chosen for parts that have to cut or are liable to heavy wear.
Most tools need handles. You might choose to forge a tang to go into a hole in a wood handle. If the tool will be pulled, cut teeth in the tang (Fig. 2-1P) to strengthen the joint. Another good joint, particularly for attaching a long wood handle, uses a conical socket (Fig. 3-1A). Draw a view of the shape you want and repeat it each side (Fig. 3-1B). This gives almost a full circle and there can be a gap between the edges after shaping. If you want the edges to meet, allow a little more than three widths. Curve the ends. Appearance is improved if you shape the top. Shoulder the end of the tool to fit in the cone (Fig. 3-1C). Roll the cone to shape and weld it to the shouldered rod with the gap between the sheet metal edges underneath. Drill the cone for two or more wood screws into the handle. The choice of metal sizes depends on the tool, but for ½-inch rod the cone may be made of 16-gauge steel.
(Continues...)
Excerpted from Blacksmithing Projects by Percy W. Blandford. Copyright © 1988 Percy W. Blandford. Excerpted by permission of Dover Publications, Inc..
All rights reserved. No part of this excerpt may be reproduced or reprinted without permission in writing from the publisher.
Excerpts are provided by Dial-A-Book Inc. solely for the personal use of visitors to this web site.
Table of Contents
Contents
Introduction,1 Set of Punches and Chisels,
2 Wood-Cutting Tools,
3 Garden Tools,
4 Plant Pot Hanger,
5 Plant Stands,
6 Yard Seat,
7 Trestles,
8 Outdoor Table,
9 Glass-Topped Table,
10 Pokers,
11 Door Hinges,
12 Door Latches and Bolts,
13 Simple Wind Vane,
14 Ornate Wind Vane,
15 Exterior Lamp Bracket,
16 Domestic Hook Hardware,
17 Fireplace Smithing,
18 Boot Aids,
19 Coat and Umbrella Stand,
20 Small Gate,
21 Scrolled Gate,
22 Fences and Railings,
23 Wheelbarrow,
24 Traditional Candlestick,
Index,