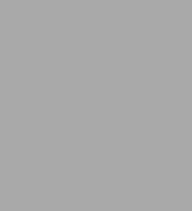
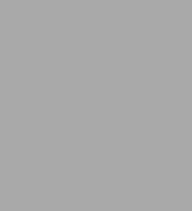
Hardcover
-
PICK UP IN STORECheck Availability at Nearby Stores
Available within 2 business hours
Related collections and offers
Overview
Product Details
ISBN-13: | 9780691633817 |
---|---|
Publisher: | Princeton University Press |
Publication date: | 04/19/2016 |
Series: | Princeton Legacy Library , #907 |
Pages: | 354 |
Product dimensions: | 8.50(w) x 11.00(h) x 1.00(d) |
Read an Excerpt
American Rubber Workers & Organized Labor, 1900-1941
By Daniel Nelson
PRINCETON UNIVERSITY PRESS
Copyright © 1988 Princeton University PressAll rights reserved.
ISBN: 978-0-691-04752-2
CHAPTER 1
Introduction: The Rubber Workers and Organized Labor
The relationship between American rubber workers and organized labor properly dates from the 1880s, when manufacturers responded to the growth of the market with a series of new technologies — "mass production" — and the labor movement embraced an approach to organization based on the craft and, later, the strategic occupation rather than on the wage earner. For many years these developments were only indirectly related. Mass production created armies of "semiskilled" machine operators who were highly paid and reasonably powerful compared with most factory laborers but who lacked a craft or identifiable occupation. To organize strategic workers in such a setting often meant organizing the entire plant. Uncomfortable with that prospect, the American Federation of Labor and its affiliates concentrated on mining, construction, the services, and small-batch manufacturing. By the turn of the century, when the advent of relatively inexpensive automobiles and electrical machinery created a second generation of mass production industries and more semiskilled machine operators, the divorce of mass production and the labor movement was virtually complete. Appropriately, the long and often rancorous debate between "craft" and "industrial" unionists dated from the same period.
At the turn of the century the rubber industry consisted of more than three hundred small plants that employed a mature, labor-intensive technology to produce footwear, belting, hose, druggists' supplies, and related items. The automobile at first simply added another popular product, the pneumatic tire. Beginning about 1909, however, inventors and engineers introduced innovations in manufacturing techniques that distinguished tires from other rubber goods. The central feature of this development, which continued through the 1910s and 1920s, was specialized machinery that increased the speed of manufacture and reduced unit production costs. The boldest of the tire manufacturers fully exploited the new technology and made substantial commitments to crude rubber production and tire marketing; their firms became vertically integrated. The less adventurous simply created large factories and remained single-function manufacturers; unless they found a specialized market niche, they faced an increasingly perilous existence. The many marginal producers who clung to the labor-intensive technology of the turn of the century had even smaller chances of survival.
By the early 1920s, then, the American rubber industry had two major divisions: a tire sector consisting of four big businesses, a handful of large factories, and a few small, marginal firms; and a nontire sector consisting of a few large factories and many small firms. Without a mass production technology, size conferred little or no competitive advantage.
The advent of tire manufacture also transformed the industry's labor force. In contrast to the insecure European immigrants who gave many of the older New England and New Jersey rubber plants a distinctive social cast, brawny farm youths dominated the labor force in the midwestern tire firms. Because the early tire factories used primitive tire-building and curing machines that relied on human energy as much as steam or electrical power, a physical elite was indispensable. The young men who were large and strong enough to qualify earned the wages of skilled workers in other industries. Understandably, they became known for their optimism, self-confidence, and independence. In the 1910s mass production gradually reduced the need for physical stamina, but the simultaneous labor shortage, resulting from the World War I industrial boom, forced manufacturers to look to Appalachia for additional workers. Most of the individuals they recruited shared their predecessors' familiarity with hard physical labor as well as their ambitions and values.
After 1910 the tire workers profoundly influenced the labor organizations that appeared in the industry. Because the elite was large but unskilled, it spurned traditional craft organization. Because it was ethnically and socially homogeneous in the midwestern plants, the industry leaders, it dominated the labor force. And because most tire employees were involved in mass production operations, they made the distinctive "veto" of machine operators in capital-intensive industry a focus of union activity. During the labor upheavals of the World War I era, the elite shared the leader's mantle with other workers. After 1920, it became the vital element in organizing efforts throughout the industry. Only at the end of the 1930s, when a new combination of demand and technology reduced the importance of the tire workers, did its influence lessen.
Though nearly all employers opposed organization, they tempered their hostility with an appreciation of economic and political conditions. The big businesses, with greater resources and more control over the environment, had more options than the large factories or small plants. In the 1920s they experimented with company unions; in the 1930s they embraced diverse approaches to their employees, ranging from "progressive" to "realistic." Though they were also more subject to political pressures than the non-integrated companies, they soon learned to implement their choices in legally and politically acceptable ways. Moreover, they retained a final option, the ability to move their operations to new, more accommodating sites.
The executives of large factories and small firms, on the other hand, were captive to their environment. Where the local labor movement was weak and public authorities were committed to industrial expansion, employers resolutely resisted organization. Where the labor movement was strong or the elite divided, they were more flexible. Since most of the successful large factories were in the Akron area, a center of union activity, it is hardly surprising that they became known for good relations with their employees in periods of union growth. By the mid-1930s they had become models of accommodation and "mature" industrial relations. Some small firms in or near Boston, New York, and Philadelphia were also cooperative. But most small companies were in isolated communities with little history of organization and a strong sense of the value of low wages. In these settings, union efforts often became prolonged, violent adventures.
Two other familiar influences had a large and demonstrable impact on the rubber workers' behavior. The first was the business cycle, the critical variable in the ebb and flow of the American labor movement in the pre-World War II years. If the industry influenced the character of union activity, the business cycle largely determined its timing. When jobs became plentiful and the future seemed promising, workers organized. There were no exceptions. Conversely, when the economy declined and opportunities were more limited, workers abandoned their unions and remained deaf to outsiders' appeals. The unique feature of the 1930s was not the breakdown of this pattern but the manufacturers' unparalleled loss of self-esteem and public stature, which allowed unions to operate in a comparatively peaceful environment during the years of economic growth, 1933 to 1937. The workers' activities during those years and afterward, when they faced severe challenges, underlined the close association between the health of the economy and the vitality of the labor movement.
The other influence was a variety of pro-union groups from outside the industry. The most important of these, perhaps surprisingly, was the AFL. While most established unions remained oblivious to the 80–90 percent of rubber workers who did not have an identifiable craft, the Federation itself was reasonably active. Under Samuel Gompers and especially William Green, the Ohio miner, politician, and United Mine Workers official who became AFL president in 1924, the AFL became the focal point for most organizing efforts. Its failures were due partly to conditions that Federation officials could not control and partly to shortcomings in their approach. Two flaws stand out: erratic leadership and the failure of Gompers, Green, and their subordinates to recognize tire builders and pit workers as strategic workers in the tire factories. Ultimately it was not Green or his deputies but the leaders of the cio and another prominent Mine Worker, Allan S. Haywood, who became the external catalysts in the consolidation of the United Rubber Workers. One of the more intriguing features of the rubber workers' experiences in the 1930s was the contrast between the popular images of the rival federations and the behavior of their representatives. In Akron and other rubber manufacturing centers, AFL organizers often seemed irresponsible and unbusinesslike. Cio agents, on the other hand, were unfailingly moderate and cooperative; whatever their personal inclinations, they spoke the language of labor-management harmony and business unionism.
Besides the AFL and cio, various political activists sought to influence the rubber workers and their organizations. This was a common experience among industrial workers, though the results in this case may have been atypical. The avowed radicals — Socialists and Communists — were colorful but ineffectual. Among the rubber workers their militancy was redundant and their ideas unappealing. The Democrats, on the other hand, were less flamboyant but more successful. By the mid-1930s they could claim the active allegiance of most rubber workers. Their relationship with the URW was more turbulent and inconclusive; before 1940 it had little if any effect on the union's prospects.
Government also played a substantial but ambivalent role in the workers' history. The early New Deal legislation, notably the National Industrial Recovery Act, created a favorable climate for union growth and shaped the rubber workers' response at least as long as William Green and the AFL guided their actions. The Wagner Act of 1935 had a similar effect in the late 1930s. It is more difficult to show that any law or executive action directly advanced the workers' prospects. Ohio Governor James M. Cox had set the stage in 1913 by carefully hedging his assistance to Akron workers during a major strike. The New Dealers of the 1930s similarly operated in accordance with conceptions of public service and professional responsibility that stopped well short of offering meaningful aid.
By 1941 the rubber workers' relationship with organized labor reflected influences that affected a substantial minority of all industrial workers (mass production technology), virtually all workers (the business cycle), and most of the 10 million organized workers (politics, federal government policy, and the labor movement). Their experiences had been similar to those of other industrial workers who had come of age in the 1910s and 1920s and who had witnessed the spread of mass production, the exhilaration of the World War I boom, the anxieties of the 1920s and early 1930s, and the seemingly unique opportunities of the 1930s to do something for themselves.
CHAPTER 2New Industry, New Workers, 1900–1913
She looks out from faded drawings and photographs with the fierce determination that was her hallmark. A Canadian who had migrated to Boston as a teenager, Marguerite T. Prevey (1869– ?) became a seamstress and later an optician. In 1901 she and her husband Frank, a jeweler, moved to the fast-growing industrial city of Akron, Ohio, and opened a jewelry and optometry shop on bustling Main Street. Business was good and they bought a large house on High Street, a block from the shop. As they became more prosperous, Marguerite devoted more of her energies to another of her interests, the Socialist Party of America. She became a close personal friend of Eugene Debs, the Socialists' leader and presidential candidate, and made her house his informal Ohio headquarters. In 1908 and 1909 Prevey headed the party's Woman's National Committee. Brimming with indignation, she preached a secular gospel of salvation through political action that was especially appealing to wealthy sympathizers. Ironically, she would find her greatest opportunity virtually in her backyard, among the more humble men and women who worked in the giant rubber plants that dominated the local economy.
Origins of the Industry
The industry that Marguerite Prevey would confront had appeared in the 1830s and developed with little fanfare for three quarters of a century. Traditional histories of the rubber industry are stories of heroic entrepreneurship, particularly that of Charles Goodyear, the tragic figure whose discovery of vulcanization, the process of heating rubber and sulfur to make the rubber stable and elastic, was the foundation of the industry. This emphasis has not been wholly misplaced, for the pioneers dominated the industry on both sides of the Atlantic for a half century. Yet it has tended to obscure the fact that the development of rubber manufacture, like the growth of many nineteenth-century industries, simply reflected the potential of crude empirical experimentation and mechanization.
If the origins of the industry were less novel than the founders and their nineteenth-century chroniclers believed, the subsequent history of rubber manufacture was wholly unexceptional. After the 1840s there were no major technical or organizational innovations; "progress resulted from continuous improvements by the practical man." When bales of wild rubber arrived at a factory, workers removed dirt and impurities; milled and "compounded" the rubber by adding sulfur and other chemicals; calendered the mixture into thin sheets, often combined with cotton fabric; cut the sheets into pieces and in the case of boots and shoes assembled the pieces; vulcanized the resulting product; finished it, usually by adding varnish to improve the appearance; and shipped it to wholesalers for resale and distribution. The manufacture of industrial and druggists' products was similar, except for the assembly stage. The work was labor intensive, particularly in the manufacture of footwear, where the hand assembler or "maker" was the central figure in the production process. Together with the uncertain quality of the raw material, intense competition created a hazardous, speculative atmosphere. Manufacturers reacted by setting up informal associations and cartels. Between 1865 and 1892, the history of the rubber boot and shoe industry was largely the history of these anticompetitive combinations.
Finally, in 1892, Charles R. Flint, a wholesale rubber merchant and speculator, merged nine boot and shoe companies into the United States Rubber Company, one of the first of the great horizontal combinations of that era. Other acquisitions in 1893 raised U.S. Rubber's market share to 50 percent, and the purchase in 1898 of the Boston Rubber Shoe Company, the industry leader, boosted U.S. Rubber's output to three quarters of the industry total. In 1898 Flint also engineered the formation of the Rubber Goods Manufacturing Company, a combination of mechanical goods producers that soon embraced half the market and most major producers except for a group of Trenton, New Jersey, firms and the B. F. Goodrich Company of Akron, Ohio. By 1905, when U.S. Rubber acquired a controlling interest in Rubber Goods Manufacturing, it was as large as its new parent.
Like other architects of late-nineteenth-century combinations, Flint and his associates discovered that mergers provided only a temporary antidote to price competition. Their failure to embrace the "managerial revolution," specifically, to centralize and rationalize production, encouraged manufacturers who had sold out to the trust to form new companies and undercut the inefficient giant. U.S. Rubber's profits declined after 1895 and it paid no dividends from 1900 to 1911. Though it remained the industry leader in boots and shoes and mechanical goods, it continued to decline until the 1920s, when severe losses forced a major overhaul of the company.
(Continues...)
Excerpted from American Rubber Workers & Organized Labor, 1900-1941 by Daniel Nelson. Copyright © 1988 Princeton University Press. Excerpted by permission of PRINCETON UNIVERSITY PRESS.
All rights reserved. No part of this excerpt may be reproduced or reprinted without permission in writing from the publisher.
Excerpts are provided by Dial-A-Book Inc. solely for the personal use of visitors to this web site.
Table of Contents
- FrontMatter, pg. i
- CONTENTS, pg. v
- ILLUSTRATIONS, pg. vii
- PREFACE, pg. ix
- ABBREVIATIONS, pg. xi
- CHAPTER ONE. Introduction: The Rubber Workers and Organized Labor, pg. 1
- CHAPTER TWO. New Industry, New Workers, 1900-1913, pg. 8
- CHAPTER THREE. Innovations, 1913-1920, pg. 44
- CHAPTER FOUR. Maturity, 1920-1929, pg. 77
- CHAPTER FOUR. Maturity, 1920-1929, pg. 111
- CHAPTER SIX. Labor in Transition, 1934-1935, pg. 143
- CHAPTER SEVEN. Union Revival, 1936, pg. 170
- CHAPTER EIGHT. Labor on the March, 1936-1937, pg. 204
- CHAPTER NINE. Labor on the March: Outlying Cities, 1936-1937, pg. 234
- CHAPTER TEN. Setbacks, 1937-1938, pg. 263
- CHAPTER ELEVEN. Stagnation and Rebirth, 1938-1941, pg. 289
- EPILOGUE: The Rubber Workers in Retrospect, pg. 322
- BIBLIOGRAPHIC NOTE, pg. 326
- INDEX, pg. 329