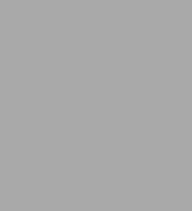
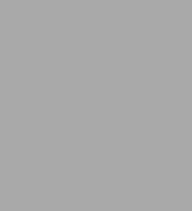
eBook
Available on Compatible NOOK devices, the free NOOK App and in My Digital Library.
Related collections and offers
Overview
Starting with an overview of fundamental principles, the treatment examines the aerodynamicist's basic data and considers aspects of performance, longitudinal stability and control, and lateral stability and control. A selection of problems appears at the end of the book, in addition to a density and pressure altitude conversion chart and a composite performance chart.
Product Details
ISBN-13: | 9780486830223 |
---|---|
Publisher: | Dover Publications |
Publication date: | 05/16/2018 |
Series: | Dover Books on Aeronautical Engineering |
Sold by: | Barnes & Noble |
Format: | eBook |
Pages: | 208 |
Sales rank: | 842,478 |
File size: | 27 MB |
Note: | This product may take a few minutes to download. |
About the Author
Read an Excerpt
CHAPTER 1
FUNDAMENTAL PRINCIPLES
1-1. Aerodynamic Forces; Dimensionless Coefficients
Aerodynamics is one branch of the general subject of fluid mechanics which is to a great extent concerned with the reactions occurring between fluids and solids immersed in them. Before proceeding to a discussion of the more specialized field it will be helpful to consider briefly the general question of the forces which act on a body when it moves through any fluid. Here a very elementary relativity principle is useful. This principle states that the force exerted by the fluid on the body is exactly the same in the following two cases illustrated in Fig. 1·1:
(a) The body moves with a velocity V through the fluid which is at rest far from the body.
(b) The body is at rest and the fluid flows past it, the fluid far from the body moving with a velocity — V.
The principle may be stated somewhat more concisely in the form: The force exerted hy a fluid on a body does not depend on the absolute velocity of either fluid or body, but only on the relative velocity between them. In aeronautics we are usually concerned with the force on an airplane or a part moving through the air which is considered to be at rest far from the airplane. For purposes of visualization, however, it is often more convenient to think of the airplane as at rest with the entire atmosphere moving past it. The relativity principle states that the force on the airplane or part will be identical in the two cases.
With this in mind consider an element of solid surface, ΔS, at rest with a fluid flowing past. The element is taken so small that it may be considered as flat. Figure 1-2 represents a plane perpendicular to ΔS; the fluid is assumed to move in the plane of the paper. The force which the fluid exerts on ΔS may be represented by the vector ΔF, giving both the magnitude and the direction of the force. It is found convenient to resolve this force into its two components normal and tangential to the surface element ΔS. These components are indicated by ΔFn and ΔFt. If the force components are divided by the area, ΔS, of the element, quantities are obtained which have the nature of force per unit area, or stress. The normal stress, ΔFn/ΔS, is called the average pressure, p, over the element, and the tangential stress, ΔFt/ΔS, is referred to as the shearing stress, τ. The values of p and τ at a point on the surface are obtained by determining the limits which the above ratios approach as the area, ΔS, surrounding the point goes to zero.
Later it will be seen that the pressures and shearing stresses at the surface of a body moving in a fluid have very different physical origins, so that it is convenient to separate the resultant forces on the body arising from these two types of stress. The so-called "pressure force" is obtained by adding the force vectors ΔFn due to the action of pressure perpendicular to every element ΔS of the surface of the body. Since each ΔFn is a vector, having both magnitude and direction, the addition must be made vectorially so that the total pressure force is actually the resultant of all the elementary forces ΔFn. Similarly the resultant of all the elementary tangential forces ΔFt may be obtained and is called the friction force or "skin friction" acting on the body.
The question now arises of determining and making available to the engineer data giving the resultant forces which will occur on the moving bodies with which he must work. The most direct procedure would be to set laboratories to work determining such forces under all the various conditions which could be expected to occur. The results could then be presented tabularly in some sort of handbook form. It is at once obvious that the enormous amount of material which would be required to present the results would make such a collection practically useless. What is first needed is some sort of systematization which will permit an orderly presentation in terms of the various parameters of greatest importance. Such a systematization was accomplished by the great English engineer and physicist, Osborne Reynolds, who laid the foundations for modern fluid mechanics during the latter part of the nineteenth century.
The most important of Reynolds' results in this connection can be obtained quite easily through the application of elementary dimensional analysis. In order to demonstrate this the problem is simplified as follows: One member of a family of geometrically similar solid bodies is considered. The body moves in a given direction with uniform velocity through a homogeneous fluid which extends to infinity and is at rest except for the velocities produced in it by the motion of the body. The force exerted by the fluid on the body as a result of the motion is to be found. In order to proceed all the parameters which can enter into the problem must first be listed. Gravity cannot have any effect since the fluid is homogeneous and any forces due to buoyancy will be independent of the motion, having the same value whether the body is at rest or moving. Since gravity does not enter the problem the various members of the family of geometrically similar bodies are characterized only by their size. In fact, if some characteristic linear dimension l is chosen, e.g., the diameter if the bodies are spheres, the length if they have streamline or fuselage shape, then any member of the family is completely defined by a numerical value for l. The velocity with which the body moves is denoted by V. The force F on the body will then depend on l, V, and on the properties of the fluid through which the body moves. This dependence can be indicated symbolically in the form:
F = F(l, V, fluid properties) [1·1]
The parameters which define the fluid properties must be found. The first is obviously the density which is universally written as ρ = mass of fluid per unit volume. The second is connected with the shearing stress which occurs when adjacent layers of fluid slide past one another. The simple law governing this phenomenon was originally given by Newton and has been so often verified experimentally that it may be considered as an empirical law. It can be understood most readily in connection with the following very simple type of flow. The motion is taken as two-dimensional which means that the velocity at every point has a direction lying in a plane parallel to a fixed reference plane (as, for example, that of the paper). Furthermore the distribution of velocities is identical in all of these planes. The motion is further restricted in that, of the two velocity components in such a plane (u parallel to the x axis and v parallel to the y axis, using the coordinate system indicated in Fig. 1-3) one is required to vanish. We choose the coordinate system so that the v component vanishes and the velocity at any point is completely determined by the value of u at the point.
The type of diagram shown in Fig. 1·3 is very convenient as a means of visualizing the flow conditions and will be used frequently throughout the later discussions. It represents the distribution of velocity over a section x = constant, taken as x = 0 in Fig. 1-3. At each value of y along this line a vector is drawn parallel to the velocity, i.e., to the x axis, the length of the vector being proportional to the magnitude of the velocity at the point. The curve joining the end points of all these vectors is called the velocity profile and gives an immediate visual representation of the dependence of u on y, written symbolically u(y).
Newton's friction law mentioned above gives the relation connecting the shearing stress between two adjacent layers of fluid at an arbitrary height, say y1, and the velocity distribution u(y). It states that this shearing stress is inversely proportional to the slope of the velocity profile, or expressed analytically
τ - μ du/dy [1·2]
where μ = a constant of proportionality, and du/dy = the velocity gradient = the rate of change of u with respect to y = 1/tan θ, where tan θ = the slope of the velocity profile at the value of y in question (in this case y1).
The constant μ is found to depend on the nature and state of the fluid and is called the coefficient of viscosity. It is large for sticky or viscous fluids like lubricating oil and small for "watery" fluids like water itself or air. It is actually the physical constant which determines the nature of any fluid with regard to shearing frictional phenomena.
A third physical property of the fluid which might be expected to be of importance is the compressibility. Liquids like water are, however, so nearly incompressible that this factor does not enter, and even for gases like air compressibility has a negligible effect for many important phenomena. We shall later investigate a little more closely the conditions under which compressibility can be neglected and shall for the present assume that the fluids under consideration may be treated as incompressible.
It appears that the properties of the fluid are completely given for the purposes of this study by the values of the two parameters ρ and μ. The symbolic equation 1·1 may then be written
F = F(V, l, ρ, μ) [1·3]
The relation between the force F and the four independent parameters, V, l, ρ, μ, can now be given a much more precise form through the application of the principle of dimensional homogeneity. This principle may be stated very crudely as follows: "In any equation of the form
A + B + C + D + ... = M
each of the terms A, B, C, D, ..., M must have the same dimensions if the equation has any physical significance."
No proof of this principle will be attempted here, but its fundamental importance in two quite different connections must be emphasized. First its application leads to the relatively simple derivation of many fundamental physical laws like that below. Second its continued use during the analysis of any physical problem can be of immense assistance in bringing to light errors which might otherwise be very difficult to discover. This application of the principle is especially valuable in routine aerodynamic calculations.
For purposes of dimensional analysis a very convenient notational convention is introduced, namely, the surrounding of a symbol by bars to indicate that only the dimensions of the quantity are to be considered. Thus |A| is to be read the dimensions of A. With this convention the application of the principle of dimensional homogeneity to the equation above would lead to the set of equations
|A| = |B| = |C| = |D| = ... = |M|
In applying the principle to equation 1 3 a more useful form for the function F is needed. A very general expression is
[MATHEMATICAL EXPRESSION OMITTED] [1·4]
where the exponents ai ... di can have any values and the coefficients Ci are dimensionless numbers. The symbol [summation over i] means that all the terms for any number of values of the index i are to be added. Writing out a few of the terms results in
[MATHEMATICAL EXPRESSION OMITTED]
The principle of dimensional homogeneity requires that each term in the series have the same dimensions, hence
\ F \ = \ PybV°ld \ [1-5]
where a ... d represent any one set of the values ai ... di The only dimensions which appear in any branch of dynamics are Mass, M, Length, L, and Time, T. Of the various terms in equation 1·5, only μ is unfamiliar, so its dimensions will first be determined. From equation 1·2
[MATHEMATICAL EXPRESSION OMITTED]
and applying the dimensional homogeneity principle
[MATHEMATICAL EXPRESSION OMITTED]
Now |force/area| = |mass X acceleration/area| = ML/T2L2 = M/LT2
|Velocity/Length| = L/T/L = 1/T
Therefore
|μ| = M/LT2/1/T = M/LT
All the other terms are familiar:
[MATHEMATICAL EXPRESSION OMITTED]
By substituting in equation 1·5
[MATHEMATICAL EXPRESSION OMITTED]
and by collecting terms
[MATHEMATICAL EXPRESSION OMITTED]
Now if the dimensions on the two sides are equal the following is true:
a + b = 1; c + d - 3a - b = 1; b + c = 2
Here there are three equations with four unknowns, so that it is possible to solve for any three of the unknowns in terms of the fourth. By solving for a, c, and d, in terms of b, we easily obtain
a = 1 - b, c = 2 - b, d = 2 - b
so that the typical term of the series for F becomes
[MATHEMATICAL EXPRESSION OMITTED]
The relations just found between a, b, c, d will obviously hold for any set ai, bi, ci, di; so that the series (1·4) for F becomes
[MATHEMATICAL EXPRESSION OMITTED]
The ratio μ/ρ occurs so frequently in fluid mechanics that it is given a name and symbol:
v = μ/ρ = Kinematic viscosity
Furthermore the ratio ρVl/μ = Vl/v, which is readily seen to be a dimensionless or pure number, is of such fundamental importance that it has been named in honor of its discoverer, Osborne Reynolds:
R = Vl/v Reynolds number
The series [MATHEMATICAL EXPRESSION OMITTED] where the values of Ci and bi are quite arbitrary can represent any reasonable function of R, say F(R). Hence equation 1·4 may be written
F = F(R)ρV2l2
It is customary to call the dimensionless function F(R) a force coefficient and write it as 1/2CF or 1/2CF(R), the latter form being used when the dependence on Reynolds number is to be emphasized. (The reason for the 1/2 will appear later.)
The dimensional analysis has therefore led to a very definite form for the relation between forces due to the motion of solids through fluids and the physical parameters involved. This relation is usually written
F = CF1/2ρV2S; CF = CF(R) [1·6]
where the coefficient CF is a pure number depending on the Reynolds number Vl/v, and S is a characteristic area of the body in question (proportional to l2). Actually it is found experimentally that in many cases the variation of CF with R is negligible, so that in such cases CF becomes a simple numerical constant.
The problem of determining and classifying experimental data for the tise of the engineer is now enormously simplified. For a given shape of body at a given attitude it is only necessary to obtain experimentally the dependence of CF on R. Then for any combination of size, speed, density, and viscosity, the force F can be calculated from equation 1·6. If CF is a constant a single experimental value suffices to give all the required information.
In aeronautics the engineer is primarily concerned with two components of force and one moment. These are
Lift = L = force perpendicular to the direction of motion, and usually vertical.
Drag = D = force in the direction of motion, taken as positive when the force is in the down- stream direction.
Pitching moment = M = moment about an axis perpendicular to the direction of motion and to the lift vector, tending to raise the leading edge of the body.
The question of dimensionless coefficients corresponding to moments has not been considered but since | moment | = (force X length | it is clear that in the expression for moment analogous to equation 1·6 there must be one more length on the right side. This length is usually chosen as the l which appears in the definition of Reynolds number. When airplane wings or complete airplanes are under discussion, S is taken as the wing area and l is replaced by c, the mean chord of the wing. For the three primary airplane coefficients we therefore have
[MATHEMATICAL EXPRESSION OMITTED] [1·7]
where the usual definition of Reynolds number has also been included for the sake of completeness. It must be remembered that in general all of these coefficients are functions of the shape and attitude of the body under consideration. For a given shape of wing or airplane the attitude is generally described by the angle between the direction of motion V and a reference axis often chosen as the chord line. This angle is called the angle of attack and is denoted by α. Figure 1·4 illustrates the various quantities defined above, for an airplane wing.
1-2. Experimental Determination of Forces and Moments; Scale Effect
through a fluid would be to tow the body, or a geometrically similar model of it, through the fluid and measure the forces exerted on the towing members. This is actually the standard procedure in naval architecture where ship models are tested in a towing basin. In aeronautics it is primarily used in connection with seaplane float and hull characteristics. Fig. 1·5 shows a diagram of the large N.A.C.A. towing basin at Langley Field. A somewhat more convenient technique for the measurement of air forces involves the use of the whirling arm, which is Both the above methods have obvious restrictions and difficulties which very early led to the adoption of a quite different technique based on the elementary relativity principle already discussed. Since only the relative motion between the body and fluid is of importance the desired result is obtained if the model is held fixed and a uniform stream of fluid is driven over it. When the fluid in question is air the device for accomplishing this is called the wind tunnel. Many different types of wind tunnel have been built, three of which are illustrated in Fig. 1·7-1·9. All have the purpose of creating a very uniform stream of air moving at high velocity through a working section in which a model is mounted (Fig. 1·10). The model supports are attached to a system of balances which give the forces and moments acting on the model at various attitudes and tunnel air speeds (Fig. 1·11). From the measured forces, the geometrical characteristics of the model (giving S and c), the observed tunnel air speed (F), and the properties of the air in the tunnel (giving p and p) the appropriate dimensionless coefficients corresponding to equations 1·7 can be determined. The resulting data are presented in tabular form or in graphs like that of Fig. 1·12 which corresponds to tests on a conventional airplane model.
(Continues…)
Excerpted from "Aerodynamics Of The Airplane"
by .
Copyright © 2018 Clark B. Millikan.
Excerpted by permission of Dover Publications, Inc..
All rights reserved. No part of this excerpt may be reproduced or reprinted without permission in writing from the publisher.
Excerpts are provided by Dial-A-Book Inc. solely for the personal use of visitors to this web site.