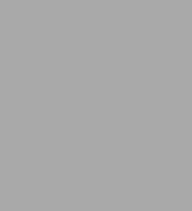
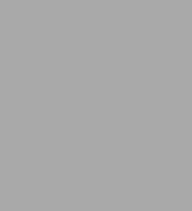
eBook
Available on Compatible NOOK devices, the free NOOK App and in My Digital Library.
Related collections and offers
Overview
Many engraving books on the market illustrate the forms and appearance of finished designs but fail to provide adequate instructions for actual engraving. In sharp contrast, this comprehensive and practical manual by two educators and master craftsmen teaches every step of the engraving process.
Clear, step-by-step instructions, accompanied by scores of illustrations, tell how to cut initials and inscriptions using a variety of alphabets, including script, ribbon, vertical script, and Roman letters as well as block and Old English. You'll also learn how to design and cut initials in monograms, what forms to use for properly decorating and embellishing engraved work, and how to correctly shape and maintain tools, particularly square script gravers — a tool basic to many different kinds of engraving. A glossary of terms and extensive, helpful question-and-answer section round out this immensely beneficial guide.
While practicing artisans will find many useful suggestions for improving their professional work, beginners will especially consider The Jewelry Engravers Manual a valuable tool for mastering the art of engraving.
Product Details
ISBN-13: | 9780486137605 |
---|---|
Publisher: | Dover Publications |
Publication date: | 05/11/2012 |
Series: | Dover Crafts: Jewelry Making & Metal Work |
Sold by: | Barnes & Noble |
Format: | eBook |
Pages: | 160 |
Sales rank: | 755,736 |
File size: | 10 MB |
Read an Excerpt
The Jewelry Engravers Manual
By R. Allen Hardy, John J. Bowman
Dover Publications, Inc.
Copyright © 1976 Van Nostrand Reinhold CompanyAll rights reserved.
ISBN: 978-0-486-13760-5
CHAPTER 1
Correct Shaping and Sharpening of Square Script Gravers
1. Use of mechanical device.
2. Stoning belly and face.
3. Polishing.
4. Cutting parallel straight lines.
5. Cutting curved parallel lines.
6. Cutting circles in hair-lines; synchronizing eye, hand and block.
7. Cutting parallel shaded lines.
8. Cutting curved parallel shaded lines.
9. Cutting shaded circles.
10. Cutting script ovals—hairlines.
11. Cutting script ovals—shaded.
12. Shading beauty-cut; basic script letter formation.
13. Shading beauty-stem; basic script letter formation; balance and proportion.
14. Shading double-C cuts.
15. Shading double-cut.
BEFORE STARTING work on the program, the principal tools involved in the first steps will be described. In Fig. 1 is shown a square script graver and its handle which is of the adjustable type. The graver is clamped into the handle by the split metal ferrule near the front end of the handle, making the total length adjustable to suit large or smaller hands, and to maintain this length as the graver is gradually shortened by regrinding. The graver has a straight end, used on work of flat or convex-curved surfaces, and a bent end, for use on the inside of concave work, such as the inside of watch-case caps, cups, spoon-bowls, etc.
Gravers as manufactured and sold by tool dealers are not ready for use and must be ground to very definite forms and polished to keen-cutting edges, in a variety of forms to be correct for the many different kinds of "cuts" that are required in the art. The mechanical device used for obtaining flat faces in grinding gravers is shown in Fig. 2. Its use will be explained fully in the proper place. Grinding and sharpening gravers is done on flat-faced slabs of abrasive material, either of natural stone or bonded synthetic grains; the latter mostly sold under the manufacturers' trade-marks "India oilstone" and "Carborundum," for quickly grinding to form. The "hard Arkansas" quarried natural stone is always used for the next step in sharpening. These stones may be bought with the two kinds mounted in pairs in a hinged wooden case as in Fig. 2, or each in a separate case. The other of the principal items of equipment needed for engraving is an engraving block, Fig. 3, which is a holder for all kinds of work. It is a mechanical turntable, its heavy iron ball-base resting in the doughnut-shaped, sand-filled leather pad on the bench. The two jaws on the revolving table are adjustable toward each other and the holes in the jaw-tops are used to hold the attachments shown in the box to the right of the block. With these attachments, almost any form of work can be held and the jaws tightened on it so that the work can be turned by one hand resting on the revolving table while the other hand manipulates the graver.
Now let us start work, following the steps listed at the front of the chapter.
1. Use of Mechanical Device
When sharpening a graver, the foot of the graver sharpener slides back and forth over a section of plate glass. The position of the glass section is most satisfactory when used as shown in Fig. 2. It can, however, be placed on top of the open part of the oilstone case, providing the hinge joints do not interfere by tilting the glass off level.
The graver sharpener (Fig. 2) enables the engraver to obtain mechanically accurate faces. The construction and theoretical operation of the graver sharpener is simple but actual manipulation requires a close study of technique. See Figs. 4, 5, 6, and 7. Here we see the faces presented to the stone in various ways to obtain desired conditions or results. Adjustments made to the graver sharpener in relation to the position of the graver with the stone, determine the accuracy of these faces.
The graver sharpener shown in Fig. 2 has three wing-nuts. One controls the adjustment of the belly angle; one controls the position or shape of the various faces; the other wing-nut serves to hold the graver firmly. With only two real adjustments to consider, sharpening the graver appears to be less of a problem than it really is. If the reader will keep it clear in his mind that the adjustments are made while holding the sharpener bottom upward, and the actual stoning is done with the position inverted (Fig. 2) no confusion will arise.
The cutting points of square script gravers have three faces. The two faces on the bottom or underside will be referred to as "the belly"; the one face on the top of the graver will be referred to as "the face." When sharpening, the steel graver is removed from the handle and placed in position in the graver sharpener.
To face either side of the belly (Fig. 4 and Fig. 5), first place the graver securely in the sharpener by tightening the wing-nut governing this adjustment. The next step is to line up the graver parallel or flat with the India stone. Since this type of graver is actually square and the slot in the sharpener forms a right angle, it is comparatively easy to position one side flat with the stone and the other side perpendicular to it. If a straight-faced belly is desired, the sharpener may be set in this position by tightening the wing-nut governing this adjustment. If a slant-faced belly is wanted, the vertical side of the graver may be tilted slightly away from its upright position, depending on the direction of the slant desired.
To tilt the graver, notice the right-angle slot in the sharpener. This will serve as a guide. Also, most sharpeners are marked with graduations, and the amount of tilt may be controlled accurately.
The next step is deciding on the amount of belly angle and setting the sharpener accordingly. For beginners, belly angles should best be on the low side. Average belly angles will fall between 8° and 12°. To set the angle, loosen the wing-nut governing this adjustment; allow the graver to lie flat on the India stone; raise the end attached to the sharpener slightly, and tighten the wing-nut. Exact belly angles may be measured by using an ordinary geometric protractor.
Sharpening "the face" of the graver is a less complicated job. See Fig. 6 and Fig. 7. A 45° face angle is what is wanted for all beginning work, shown in Fig. 6B. Figures 7A, B, and C show three conditions; A and B being acceptable shapes and C indicating a shape to avoid. Since the student is interested solely in an average graver at this point, a combination of Fig. 6B and Fig. 7B is the shape and face angle wanted.
2. Stoning Belly and Face
Before using either stone, saturate them with oil. This may be done by pouring and spreading on a little oil at a time, allowing it to soak into the stone, and repeating the procedure until the stone will absorb no more. Oil, especially prepared for oilstones, may be bought from any dealer in jewelers' supplies, or the automobile motor oil sold as "Grade SAE 10," may be used.
The India stone is used to "rough out" or grind the faces. The Arkansas stone is used to "smooth out" or polish away the coarse lines remaining from the India stone. Emery paper is the final polishing agent, and should be used in grit 4-0.
After grinding a face, using the India stone, it should be immediately presented to the Arkansas stone, no further adjustment to the graver sharpener being necessary. Care must be taken to level up the stones so that no change results when turned over from one side to the other. The three faces are ground on the two stones first. When all three are complete, the graver is placed in the handle and polished by hand on 4-0 emery paper placed on top of a flat piece of glass (Fig. 13). Fig. 8 shows a graver sharpened for average work. The belly is always sharpened first and the two sides must meet at a point as in Fig. 8B. The same amount of metal is ground away on both sides so that the line of centers (L-L') is not disturbed. If more is ground away on one side, then the line of centers is disturbed causing it to bend sharply to the right or left as the case may be.
As the two sides of the belly are ground away, an important condition arises which we will call "belly angle" (Fig. 10). The amount of belly angle depends entirely on how much metal is ground away on both sides. Belly angle is a very important feature, since it directly involves "lift" (Fig. 10C).
Lift decides for you how high or low you must hold your graver to the article or plate when making a cut. This should be carefully studied and experimented with, because herein lies the source of most graver troubles. You would find that a very low degree of lift or belly angle will cause difficulty in cutting. Also an extremely high degree is next to impossible to handle. The reader will find his happy medium through experimenting. In discussing lift, it is in relation to average cutting on average work. As the learner progresses and begins cutting on curved surfaces, he will find the lift will have to be changed to suit the surface. Curved surfaces usually demand an increased lift whether concave or convex. Flat surfaces can be cut with a lower lift. The reader should adapt the graver to suit his hand. The lift for average work should be at least high enough for the engraver to get his fingers comfortably underneath the graver handle.
Fig. 11 is self-explanatory, but here a word of caution. Avoid extremes as in Fig. 11C. For average work, Fig. 11B is ideal. If Fig. 11C were matched with a belly as in Fig. 9A, the two extremes would be of no value. If a wide shade line is desired, it must be remembered that the result is obtained by altering the belly and not the face. The right edge of the graver is brought slightly forward, because all of the cutting is done on that side, and this helps the tool to cut more readily. To execute a shade line in script, the graver is laid over on the right side considerably. By bringing the right edge slightly forward (Fig. 11B) it is not necessary to lay the graver over quite so far to get the desired width of shade line.
Fig. 12 is also self-explanatory. It is only necessary to add that a higher face angle is desired on cutting hard or tough metals. A low angle would break too many points. A graver with a low face angle cuts more readily and makes a smoother cut and should be used on all softer metals that will not endanger the point.
3. Polishing
Great care should be taken to develop correct polishing methods because therein lies the reason for the success or failure of a smoothly executed cut. Assuming that a graver has been properly faced, the problem of obtaining a good polish is undertaken. First, place the graver in the handle and polish the belly as shown in Fig. 13. This must be done by placing the side or face to be polished perfectly flat on 4-0 emery paper; pull toward you, always away from the point of the graver. Placing the fingers as shown in the illustration, press lightly as the motion is begun. In polishing thusly, always place the emery paper over the glass piece or section over which the graver sharpener slides when facing gravers. This guarantees a firm, hard, and smooth surface which will minimize the risk of rounding the edges.
Short careful strokes of about one-half inch in length are more easily controlled than long strokes and the risk of rounding the edges is reduced. However, the beginner must be very preserving in this particular task. This is hand work and requires skill to execute successfully. Much practice is required before a beginner can complete the job without rounding the edges. Many strokes are not necessary. A few slow, careful strokes are enough to insure an adequate polish. The amount of hand polishing will depend to a degree on the fineness of the Arkansas stone.
It is advisable when polishing new faces to use a fresh piece of emery paper. The first polishing stroke will leave a trail on the paper, which should show an even stroke, perfectly uniform. If the graver face is not contacting the emery paper in a flat position, the trail will show deeper on one side than on the other. This demands an immediate correction if rounded edges are to be avoided. After a considerable amount of practice, the student will develop in his finger tips a "feel" or "touch" for flatness and this "feel" may be relied upon more and more as experience is gained.
Among finished engravers, different viewpoints are often held on polishing methods. Many contend the correct way to polish the belly is to drag the graver sideways, away from the point, over the emery paper. In this manner the motion of the strokes is parallel to the cutting edges. This method is very good; results are excellent, but beginners usually have great difficulty in preserving flat faces. It is not suggested that beginners try this method until more experience is acquired.
How much to polish the faces? Looking down at the two sides or faces of the belly, the left side is the cutting edge and deserves more attention. This face should receive more actual polishing or rubbing on emery. The edge must be smooth, free of scratches and burrs. The right face may be polished just enough to remove lines and burrs created by the stones. The one face on top of the graver, "the face" of the tool, does not necessarily require any polishing other than that done on the Arkansas stone. If burrs are showing on this face, it is naturally wise to rub it over emery paper once or twice but not for the purpose of polishing. Remember that a brilliant cut depends on the brilliance of the polish on the left side of the belly (the left side of the belly when viewing both sides at once becomes the right side when in actual cutting position). Acquiring a high polish on the face is not only of no real value, but is generally detrimental to good results.
To summarize, the left face of the belly (viewing both sides) receives more polishing attention; the right side of the belly is less important, and "the face" of the graver receives little or no polishing on emery paper.
In following the program outline up to this point, the reader has become familiar with such essential equipment as the engraving block, gravers, oilstones, graver sharpener, and emery paper. Next to consider is the engraver's magnifying eyeglass or loupe, and the metal to be cut.
The correct loupe for an engraver should allow the eye to be 4 inches from the work and magnify 2½ times. The loupe should be one that is marked 4 in. x 2½X. It is important for the beginner to make sure he has the correct loupe before attempting to cut.
The best material on which to begin practice work is commercial sheet copper, cut to any convenient size to be held in the engraving block, say about two by three inches. The trade specification for a suitable metal is: "cold-rolled flat sheet copper, polished on one side, thickness 14 ounces per square foot, or .0189 inch." This thickness is minimum for properly standing up under the graver cuts. Thicker metal may be used, but it would cost more per square inch with no advantage in working qualities. Copper of this specification has a cutting quality that is probably nearest of all to averaging that of the metals of which most articles are made, that are engraved in the jewelry trade; gold of various karat-fineness, solid or filled; silver; platinum; certain non-precious metals used as a base for electroplating, etc. Plates of this kind of copper are stocked for sale by some of the jewelers' supply dealers. However, if you buy the metal in larger sheets as sold by metal dealers, it is well to have it cut to usable size by a sheet-metal workshop on their large power-shear so that the practice plates will be perfectly flat. It is impossible to maintain flatness in pieces cut with hand shears.
Holding the graver correctly is of utmost importance. The correct position is shown in Figs. 14 and 15. Fig. 16 shows the hand in relation to the copper plate and executing a straight cut. Fig. 17 shows the copper plate clamped securely in the engraving block with the aid of four small grooved pins; also showing the hands in their correct position on the block preparatory to making a cut.
Figs. 17 and 18 show correct hand posture for beginning all cutting. The difference in the thumb positions should be noted in the two illustrations. Both are correct. As cutting progresses, the student may unconsciously find himself changing from one position to the other. For extra steadiness, the left thumb serves this purpose well.
Fig. 19 shows the engraver with elbows resting on the table top, arms relaxed, with the block slightly tilted toward his body. The chair or stool should never be so high as to cause the engraver to be directly over his work; neither should it be so low that it would become necessary to overtilt the block in order to approach the work. Bad posture causes early fatigue. The engraver should keep his spine as straight as possible by selecting a chair or stool of just the right height.
(Continues...)
Excerpted from The Jewelry Engravers Manual by R. Allen Hardy, John J. Bowman. Copyright © 1976 Van Nostrand Reinhold Company. Excerpted by permission of Dover Publications, Inc..
All rights reserved. No part of this excerpt may be reproduced or reprinted without permission in writing from the publisher.
Excerpts are provided by Dial-A-Book Inc. solely for the personal use of visitors to this web site.
Table of Contents
Contents
Title Page,Copyright Page,
Preface,
Chapter 1 - Correct Shaping and Sharpening of Square Script Gravers,
Chapter 2 - Cutting Script Letters,
Chapter 3 - Cutting Ribbon Letters,
Chapter 4 - Vertical Script Letters,
Chapter 5 - Roman Letters,
Chapter 6 - Hardening and Tempering Steel,
Chapter 7 - Cutting Block Alphabets,
Chapter 8 - Cutting Old English Alphabet,
Chapter 9 - Designing and Cutting Monograms,
Chapter 10 - Final General Instructions,
Glossary of Engraving Terms,
Questions and Answers,
Index,